Compared with conventional titanium alloys, TiAl-based alloys have low density, comprehensive properties of both metal and ceramic materials during service, high specific stiffness/specific stiffness at high temperature, and better creep resistance and oxidation resistance. In recent years, TiAl-based alloys have become the international research hotspot in the field of titanium alloys.
Alloy (x/%) | Yield strength/MPa | Breaking strength/MPa | Elongation/% |
Ti–48Al–2Nb–2Cr | 324 | 422 | 2.3 |
Ti–48Al–1V(100~200) | 430 | 500 | 1.2 |
Ti–48Al–1V(300~500) | 400 | 475 | 1.8 |
Ti–48Al | 390 | 483 | 0.3-2.1 |
Ti–48Al–1V | 400 | 507 | 2.3 |
Ti–44Al–1V | 754 | — | 0.6 |
Ti–48Al(1~3)V | 520 | — | 1.5-3.5 |
Ti–48Al–2Nb–2Mn | 392 | 460 | 0.9 |
Ti–47Al–5Nb | 480 | 510 | 0.5 |
TiAl-based alloys are mainly divided into high-temperature TiAl-based intermetallic compounds (high Nb-TiAl alloys) and ordinary TiAl-based intermetallic compounds. The mechanical properties of several typical TiAl-based alloys are shown in the table below. The melting of TiAl alloy mainly includes three ways: induction induction melting (ISM), vacuum arc melting (VAM) and plasma beam melting (PM). The LEVICAST technology developed by Datong Special Steel Company of Japan and TARAMM Company of France effectively combines suspension melting with vacuum suction casting, vacuum die-casting and centrifugal casting, It can realize the complete forming of titanium alloy investment precision castings with a minimum wall thickness of 0.5mm. At present, electric arc furnace and electron beam furnace are mostly used for the preparation of domestic TiAl alloy. The water-cooled copper crucible vacuum induction melting furnace imported by Harbin Institute of Technology from German ALD Company has a relatively advanced level.
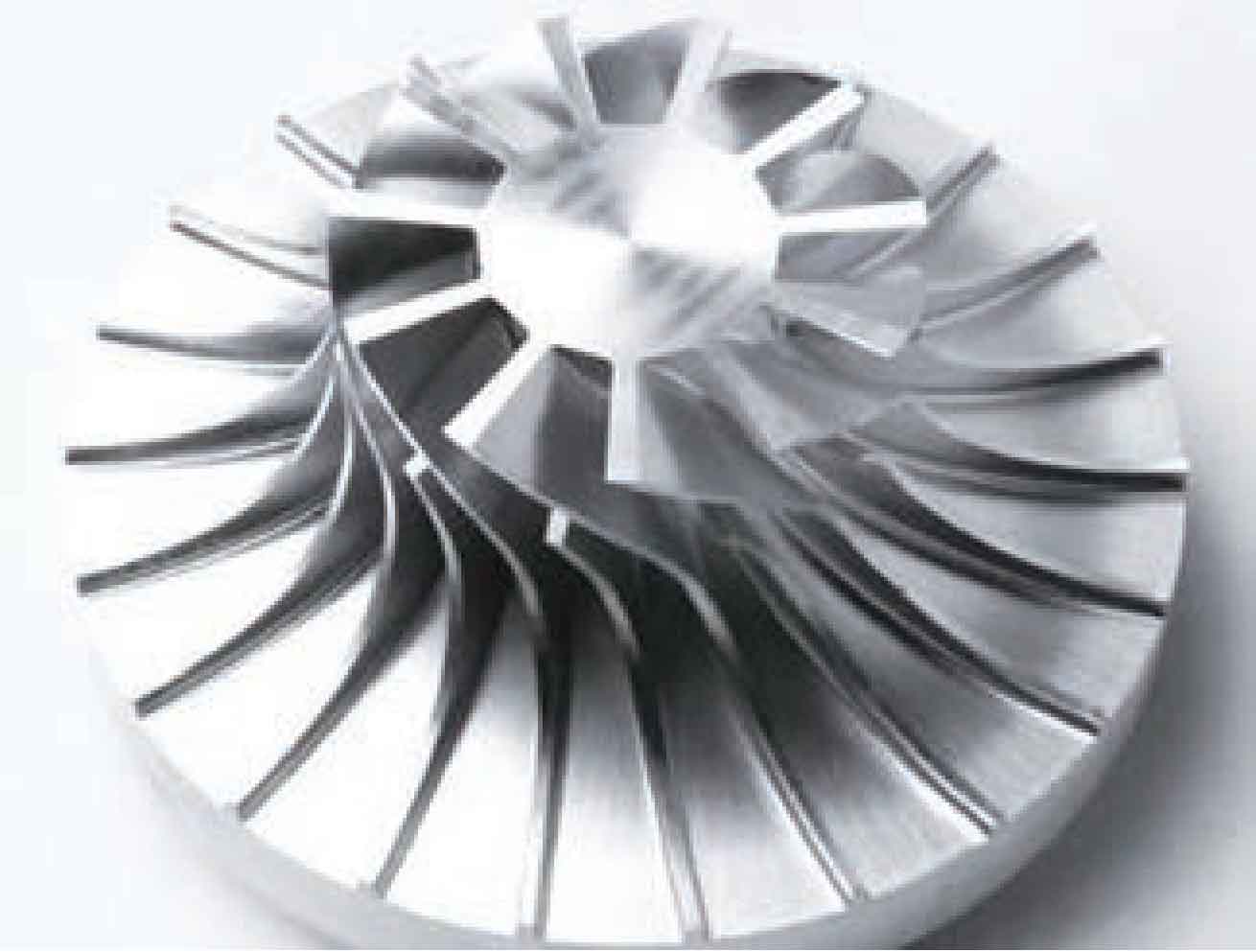
Abroad, Pratt – Whitney Laboratories of the United States, GE, Howmet, GKSS Research Institute of Germany, University of Hamburg, Aachen University of Technology, University of Birmingham, ABB in Europe, IHI in Japan, Northeastern University and Kawasaki Heavy Industries Co., Ltd. have carried out research on TiAl-based alloys and have successfully been widely used. In 1993, GE successfully carried out the simulation flight test of Ti – 47Al – 2Cr – 2Nb cast low pressure turbine blades (LPTBs), and assembled 98 TiAl-based alloy blades onto the CF6 – 80C2 commercial transport aircraft engine. After 1000 cycles, the blades were not damaged; Then, seven TiAl-based alloy blades with other components were installed for 500 cycles, and the blades were still intact (see figure). The success of this test was a milestone in the history of TiAl-based alloy research. Since then, TiAl-based alloy precision castings have been widely used in the field of aero-engine. The exhaust nozzle of the high speed civil transport (HSCT) engine led by NASA in the United States uses a large number of TiAl alloy precision castings of Ti – 4822.
Kawasaki Heavy Industry Co., Ltd. of Japan and Datong Special Steel of Japan jointly adopt investment casting method to produce TiAl-based alloy impeller. Compared with heat-resistant alloy impeller, the rotation speed of 110000 r/min can be reduced by 16%, and the total time of 170000 r/min can be reduced to 74%, which confirms the application advantages of TiAl alloy. Beijing Institute of Aeronautical Materials, together with Beijing General Institute of Iron and Steel Research, Shenyang Metal Research Institute of the Chinese Academy of Sciences, Harbin Institute of Technology, Tsinghua University and other domestic research institutes and universities, also carried out a lot of research on investment casting of TiAl intermetallics. The TiAl alloy grid precision casting jointly developed by the Beijing Institute of Aeronautical Materials and Chen Yuyong of Harbin Institute of Technology has now achieved mass production and delivery on a missile of Aerospace Science and Engineering.