The performance of aluminum alloy wheel hub produced by low pressure casting is much better than that of gravity casting, but people are still exploring: on the one hand, to further improve the mechanical properties of the wheel hub; on the other hand, to reduce the quality of the wheel hub
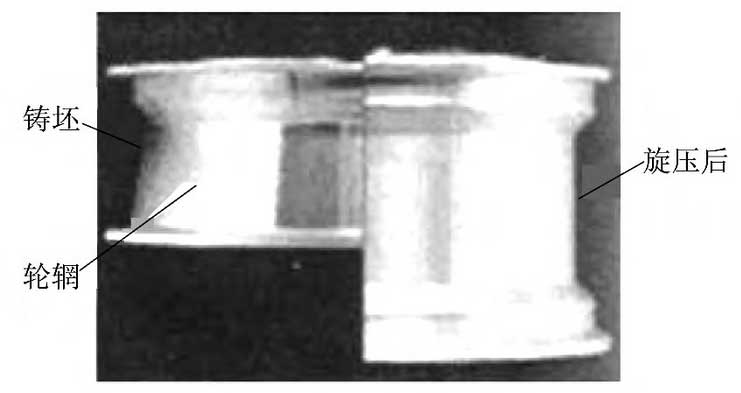
The casting hot spinning process was born in Japan in the late 1990s. The main process is: at a certain temperature, the aluminum alloy wheel casting blank of low-pressure casting is finally formed by spinning, as shown in the figure. The hot spinning temperature is usually set at 380 ~ 400 ℃, which is mainly related to the tensile properties of A356.2 aluminum alloy, as shown in the figure. As can be seen from the figure, it starts from 350 ℃, The tensile properties of the alloy increase sharply, but the high temperature will make the metal flow difficult to control.
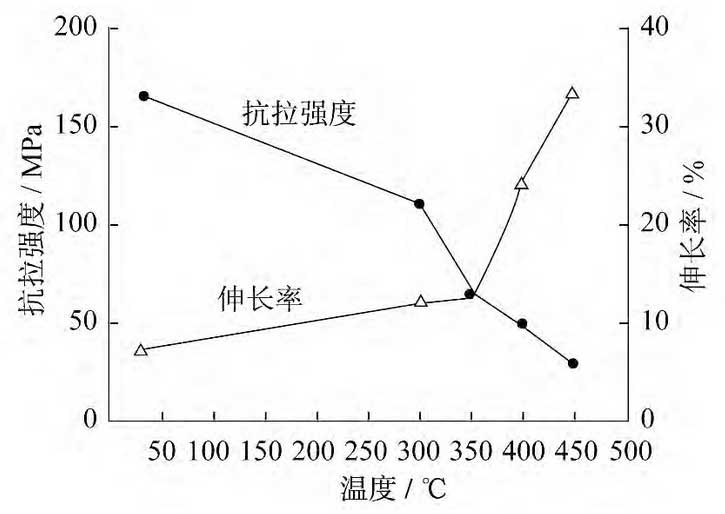
ZHY casting research shows that under the same conditions, the performance of aluminum alloy wheel hub produced by casting hot spinning is much better than that of low-pressure casting, as shown in Table 3. The strengthening mechanism in Table 3 is thermoplastic deformation. The deformation activation energy of A356.2 aluminum alloy is calculated by high-temperature deformation dynamics analysis: Q = 279.03 kJ · mol-1 at low strain rate, q = 149.60 kJ · mol-1 at high strain rate, It is concluded that high strain rate is the dynamic recovery mechanism of position slip control, and plastic deformation is more suitable for high strain rate.
High temperature plastic deformation can effectively improve the morphology and distribution of eutectic Si phase in A356.2 aluminum alloy. If SR is added to the alloy, the change of eutectic Si morphology will be weakened by hot spinning, which will mainly affect its distribution and effectively break the bad rod-like Fe phase. The increase in strength means that the cross-sectional area required to carry the same amount of force becomes smaller, so the mass of the same size cast hot spinning hub can be reduced by about 15% compared with that of the low-pressure cast hub.
The casting hot spinning aluminum alloy wheel hub has excellent performance, but the hot spinning process is a complex process integrating plastic deformation and numerical control processing, so it adds a certain degree of difficulty to production. If we want to produce high-quality products efficiently, The forming angle of the wheel, the feed rate of the wheel, the reduction rate of the wall thickness of the wheel hub and the effective speed change rate of the wheel hub must be coordinated comprehensively. Generally, the forming angle of the wheel is between 20 ° ~ 30 °, and the feed rate of the wheel is usually 0.5 ~ 1.5 mm · R-1. In addition, there are corresponding formulas for the calculation of the reduction rate of the wall thickness of the wheel hub and the effective speed change rate of the wheel hub.
Calculation formula of spinning deformation (wall thickness reduction rate) of hub:

Where: t0 is the original wall thickness of the wheel hub casting, TR is the wall thickness after spinning.
The calculation formula of equal effect speed change rate in the process of hub deformation:
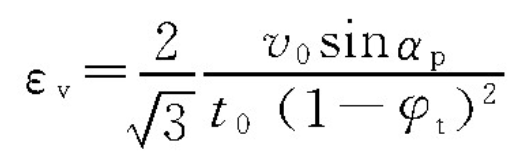
Where t0 is the initial billet thickness, V0 is the feed speed, α P is the forming angle of the spinning wheel, and φ t is the wall thickness reduction rate.