Casting is a complex process that involves numerous steps. With each step comes the potential for things to go wrong, leading to defects in the final product. Understanding these casting defects and knowing how to address them is vital to maintaining quality and efficiency in manufacturing. This article provides an in-depth look into common casting defects and how to mitigate them.
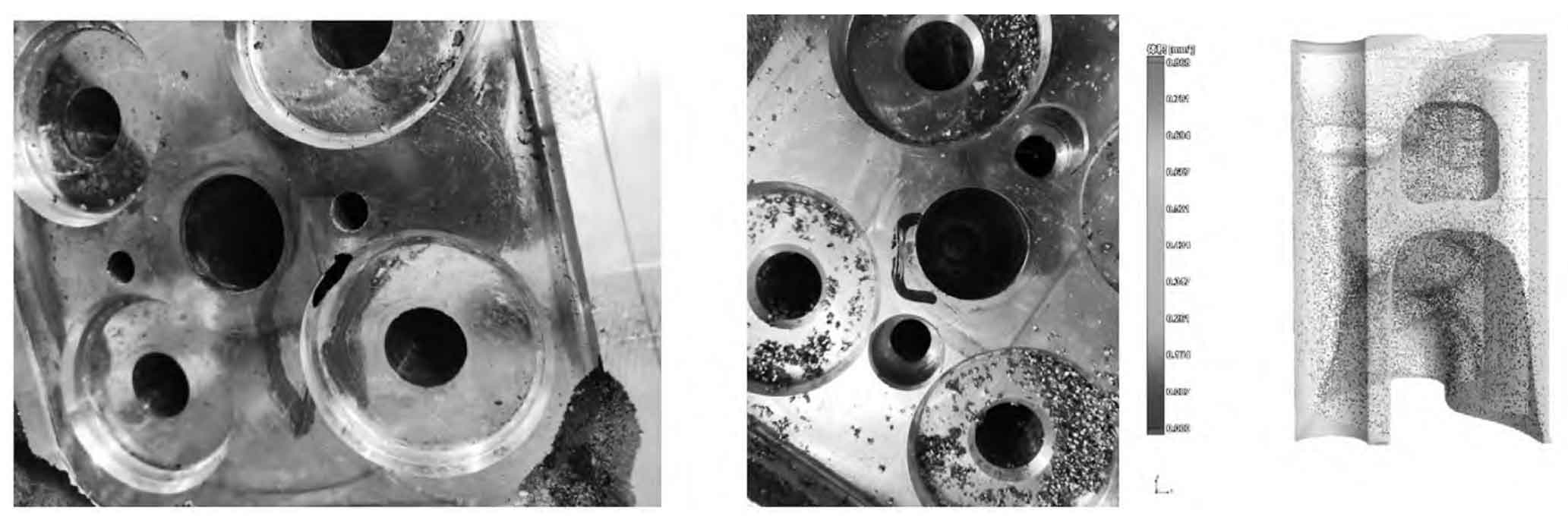
- Porosity: Porosity refers to the formation of cavities or bubbles in the casting, often due to gases trapped during the casting process or shrinkage during cooling. Properly degassing the molten metal, ensuring effective ventilation in the molds, and controlling the cooling process can help reduce porosity.
- Shrinkage Defects: Shrinkage occurs when the metal contracts as it cools and solidifies, resulting in voids in the casting. These defects can be minimized by proper design of the casting process, including the placement of risers to supply additional molten metal, and controlling the cooling rate to allow for uniform solidification.
- Hot Tears: Hot tears are cracks that appear during the solidification process when thermal stress exceeds the metal’s strength. To prevent these, it’s crucial to design the casting mold and process to ensure even cooling and minimize stress on the part.
- Cold Shuts: Cold shuts occur when two streams of molten metal in the mold fail to fuse properly, leaving a visible seam or line. Ensuring the metal is at the correct temperature and improving the flow within the mold can help prevent cold shuts.
- Misruns: Misruns happen when the molten metal does not completely fill the mold before solidifying. This can be prevented by maintaining the correct pouring temperature and speed and designing an effective gating system to guide the flow of metal into the mold.
- Inclusions: Inclusions are foreign particles, such as sand or slag, that become trapped in the casting. Maintaining clean casting materials and molds, and using filters can help prevent inclusions.
- Mold Material Defects: Defects such as cuts, washes, or scabs can occur due to issues with the mold material or preparation. Using the appropriate mold materials and ensuring proper mold preparation can help avoid these issues.
Understanding and addressing casting defects is crucial for maintaining product quality and manufacturing efficiency. It involves careful design and control of the casting process, regular inspection and testing, and a commitment to continuous improvement. By understanding the common defects and their causes, manufacturers can take steps to prevent these issues, resulting in higher quality, more reliable products.