This article focuses on the casting process and defect mechanism of magnesium-aluminum alloy. It analyzes the common defects in the casting process, such as pores, cracks, inclusions, and residual slag, and explores their causes. Corresponding solutions are proposed, including improving the casting process, optimizing the alloy composition, enhancing material properties, and improving the organizational structure. The article also emphasizes the importance of preventing and controlling casting defects to improve the quality and reliability of products.
1. Introduction
Magnesium-aluminum alloy is a new type of material with excellent comprehensive properties. It has the characteristics of high strength, low density, good corrosion resistance, and small thermal expansion coefficient, so it is widely used in aerospace, automotive, electronic appliances, construction, and other fields. However, the preparation method of magnesium-aluminum alloy is limited, and the cost is relatively high. Therefore, it is necessary to find an economical and practical method to manufacture magnesium-aluminum alloy products. Casting is one of the main methods for the preparation of magnesium-aluminum alloy, which can quickly and efficiently convert the metal liquid into solid products. However, due to the special characteristics of magnesium-aluminum alloy, such as easy to produce bubbles and uneven sintering, there are also many difficulties in the casting process.
2. Magnesium Aluminum Alloy Casting Defect Analysis
2.1 Magnesium Aluminum Alloy Overview
Magnesium-aluminum alloy is an important high-strength and lightweight metal material with excellent comprehensive properties and broad application prospects. Its main components are magnesium (Mg) and aluminum (Al), with the magnesium content generally between 30% and 60%, and the aluminum content relatively low, usually not exceeding 20%. The characteristics of magnesium-aluminum alloy include high strength, high toughness, corrosion resistance, and good heat treatment performance, so it is widely used in aerospace, automobile manufacturing, electronic devices, and other aspects. The casting technology of magnesium-aluminum alloy mainly includes melt casting method and extrusion molding method.
2.2 Casting Defect Types
In the casting process of magnesium-aluminum alloy, common defects include pores, cracks, inclusions, and residual slag. Pores are one of the most serious defects affecting the quality of castings, usually caused by too fast pouring speed or too high temperature. To avoid the formation of pores, the pouring speed and temperature should be controlled. In addition, vacuum extraction technology can also be used to reduce the gas content. Cracks are also a common problem in magnesium-aluminum alloy casting, mainly caused by too slow cooling rate or excessive cooling. Therefore, it is necessary to ensure an appropriate cooling rate and maintain an appropriate cooling time. In addition, attention should be paid to preventing thermal damage to the metal surface to reduce the possibility of cracks. Inclusions refer to the phenomenon of other substances mixed in the melt, which may lead to a decline in the quality of the casting. Therefore, measures need to be taken to remove impurities. Finally, residual slag refers to the unmelted solid particles remaining inside the casting, which will cause problems such as low hardness and poor strength of the casting. To solve this problem, a remover can be used for treatment. In short, for the casting process of magnesium-aluminum alloy, it is necessary to pay attention to various defects and their causes and take corresponding measures to prevent and correct them.
2.3 Casting Defect Causes
In the casting process of magnesium-aluminum alloy, due to the influence of various factors, various casting defects may occur. The most common ones are pores and cracks, which not only affect the quality and performance of the casting but also lead to problems such as increased production costs and potential safety hazards. Therefore, in-depth research and discussion on the casting defects of magnesium-aluminum alloy are needed. First, the escape of gas is a common casting defect. When the molten metal is poured, it will expand under the action of external pressure. If the factors such as the flow rate and temperature of the melt are not controlled in time, the gas cannot be discharged smoothly, resulting in the formation of bubbles or pores. Secondly, cracks are also a common casting defect, mainly caused by too fast cooling rate or improper cooling method. In addition, there are some other casting defects such as residual inclusions and oxide layers. Through detailed analysis and research on the causes of the above casting defects, and through the comparison and analysis of experimental data, it is found that the reason for the gas escape is the insufficient fluidity of the melt and the too high cooling rate; while the cracks are caused by the too slow cooling rate or the incorrect cooling method.
2.4 Casting Defect Hazards
In the casting process of magnesium-aluminum alloy, various defects may occur in the casting. These defects not only affect the quality and performance of the product but also affect production efficiency and cost control. Therefore, the research on casting defects is very important. Casting defects mainly include three types: surface defects, internal defects, and mechanical defects. Surface defects include cracks, crazing, and sand holes; internal defects include pores, inclusions, and residues; and mechanical defects refer to defects caused by improper casting process or uneven materials. Casting defects will cause serious harm to the product. For example, surface defects will lead to damage to the appearance of the product and shorten its service life; internal defects may affect the strength and durability of the product; and problems in mechanical properties will directly affect the use effect and safety performance of the product. Therefore, it is very important to study casting defects. By in-depth study of their causes and mechanisms, corresponding measures can be taken to reduce or avoid their occurrence. At the same time, the quality and reliability of the product can also be improved.
2.5 Casting Defect Prevention Measures
In the production of magnesium-aluminum alloy castings, common casting defects include pores, cracks, inclusions, and residual slag. These defects not only affect the quality and performance of the casting but also increase production costs and reduce product competitiveness. Therefore, how to effectively prevent and control casting defects is an important issue in the casting process. For different casting defects, corresponding preventive measures can be taken. The main cause of pores is the pressure fluctuation caused by too fast pouring speed or too high cooling rate, resulting in gas escape and the formation of bubbles. To avoid this situation, the pouring speed and temperature can be controlled appropriately during the pouring process, and sufficient cooling time should be maintained to reduce the impact of pressure fluctuation. In addition, the pouring method can be adjusted to reduce the impact of pressure fluctuation, such as using stratified pouring method or spray pouring method. The main causes of cracks are poor material quality, unreasonable mold design, and improper operation. To avoid cracks, high-quality raw materials should be selected, and the operating procedures should be strictly followed. At the same time, the design and manufacturing of the mold should be strengthened. The main cause of inclusions is the poor flow of the melt. To avoid inclusions, the shape of the molten pool can be optimized and the fluidity of the melt can be improved. Finally, the main cause of residual slag is that the melting material is not completely liquefied. To avoid residual slag, it is necessary to ensure that the melting material is fully dissolved before starting the pouring process.
3. Magnesium Aluminum Alloy Casting Defect Prevention and Control Measures
3.1 Improve Pouring Process
In the casting process of magnesium-aluminum alloy, pouring is one of the most critical links. Due to the high melting point and crystallization temperature of magnesium-aluminum alloy, blast furnace or arc melting technology is usually used for melting treatment. However, this method often leads to serious crack and pore problems on the surface of the casting. To solve this problem, this study proposes an improved pouring process scheme. Specifically, the following measures are adopted: First, a certain cooling rate is increased during the pouring process to reduce the stress distribution inside the casting. Secondly, the pouring speed and pressure are optimized to make the pouring process more stable and uniform. Finally, some special additives are used to enhance the strength and hardness of the casting. Through the application of these measures, the number of defects in the casting can be effectively reduced, and the overall quality level can be improved. At the same time, a reasonable pouring process can greatly shorten the production cycle and significantly reduce costs.
3.2 Optimize Alloy Composition
In the casting process of magnesium-aluminum alloy, alloy composition is one of the important factors affecting the quality of the casting. To reduce the number of defects in the casting and improve the performance of the casting, it is necessary to optimize the alloy composition. Specifically, the alloy composition can be optimized in the following ways: First, increase the magnesium content to improve the strength and hardness of the alloy. At the same time, the aluminum content can be appropriately reduced to ensure the fluidity and formability of the casting. In addition, a small amount of other elements such as copper and zinc can be added to enhance the comprehensive performance of the alloy. In addition, for the casting process of magnesium-aluminum alloy, temperature control is also a very important aspect. Due to the high solid-liquid interface reaction rate of magnesium-aluminum alloy, bubbles and cracks are prone to occur at high temperatures. Therefore, the casting should be heated to a certain temperature before pouring. This can effectively avoid various problems in the casting.
3.3 Improve Material Properties
In the casting process of magnesium-aluminum alloy, due to the influence of various factors such as temperature, pressure, and time, some common defects may occur on the surface of the casting. To effectively prevent the occurrence of these defects and ensure the quality of the casting, a series of effective measures need to be taken to improve the performance of the material. First, the crystallinity and microstructure of the casting can be controlled by adjusting the pouring speed and temperature. When the pouring speed is too fast or too high, the internal cooling of the casting will be uneven, resulting in cracks; while if it is too slow or too low, the grain size and shape of the casting will be affected, thus affecting its mechanical properties. Therefore, an appropriate pouring speed and temperature should be selected for the pouring operation. Secondly, heat treatment technology can be used to improve the performance of the casting. By regulating the heating and cooling process, the microstructure and morphological characteristics of the casting can be changed, thereby enhancing its strength and hardness. In addition, additives or modification methods can be used to increase the toughness and corrosion resistance of the casting. Finally, it should be noted that in actual production, different means and strategies should be flexibly used in combination with the actual situation to achieve the best results.
3.4 Improve Organizational Structure
In the casting process of magnesium-aluminum alloy, due to the action of high temperature and pressure, various types of defects are prone to occur inside the casting. One of the most common defects is pores or cracks. These defects not only affect the quality of the casting but also lead to a shortened service life or even failure of the casting. Therefore, how to effectively prevent and control these defects is one of the very important issues. To solve this problem, we need to fundamentally change the organizational structure of the casting. Specifically, the organizational structure of the casting can be optimized by adjusting the pouring speed, temperature, and cooling rate. For example, if the pouring speed is reduced to a certain extent, the generation rate of bubbles can be reduced; at the same time, appropriately increasing the cooling rate can also accelerate the solidification process, so that the casting has better organizational stability. In addition, other methods such as spraying technology and vacuum casting can also be used to improve the performance of the casting.
4. Magnesium Aluminum Alloy Casting Defect Treatment
4.1 Improve Pouring Temperature
In the casting process of magnesium-aluminum alloy, pouring temperature is a very important factor. If the pouring temperature is too high or too low, various types of defects will occur on the surface of the casting, such as cracks, pores, and residual slag. Therefore, in order to improve the quality of the casting, it is necessary to achieve better control by adjusting the pouring temperature. First, we should understand the influence of different pouring temperatures on the casting. Generally speaking, the higher the pouring temperature, the faster the internal crystallization speed of the casting, thus reducing the size and number of grains and improving the strength and hardness of the casting. However, if the pouring temperature is too high, the gas in the molten metal will escape, forming bubbles, which will expand and rupture during the cooling process, ultimately resulting in cracks on the surface of the casting. In addition, too low pouring temperature will also affect the quality of the casting. Because when the pouring temperature is too low, the gas precipitated in the molten metal will occupy more space, increasing the number of pores inside the casting. This will not only affect the mechanical properties of the casting but also increase the weight and cost of the casting. Therefore, selecting an appropriate pouring temperature is one of the important means to prepare high-quality magnesium-aluminum alloy castings. To solve this problem, some methods can be used to adjust the pouring temperature. For example, the pouring temperature can be reduced by changing the pouring rate. At the same time, appropriate additives can be used to inhibit the generation of bubbles. In addition, vacuum extraction technology can also be used to remove oxygen and other impurity substances in the air to achieve the purpose of reducing the pouring temperature.
4.2 Optimize Pouring System
In the casting process of magnesium-aluminum alloy, the design and debugging of the pouring system are crucial. A reasonable pouring system can effectively reduce the defects in the casting and improve the quality and performance of the casting. Therefore, how to optimize the pouring system has become one of the important research directions at present. First, the structure and parameters of the pouring system need to be considered. The traditional pouring system usually adopts a nozzle-type pouring method driven by a hydraulic pump. Although this method is simple and easy to operate, it is prone to oil leakage, resulting in cracks or carburization on the surface of the casting. To solve this problem, a nozzle-type pouring method controlled by a solenoid valve can be considered. This method can achieve different pressure outputs by adjusting the size of the solenoid valve, thus achieving better pouring results. In addition, attention should also be paid to the influence of factors such as pouring speed and temperature to ensure the maximization of the quality and performance of the casting. Secondly, the stability and reliability of the pouring system should be emphasized. Due to the high melting point and crystallization rate of magnesium-aluminum alloy, it is necessary to maintain a certain temperature and pressure level during pouring. At the same time, the maintenance and 保养 of the pouring equipment should also be considered. Finally, adjustments and improvements should be made in combination with the actual situation. Through continuous testing and practice, the most suitable pouring scheme for oneself should be found, and the pouring system should be continuously improved and upgraded to ensure the maximization of the quality and performance of the casting.
4.3 Reasonably Design Pouring Speed
In the casting process of magnesium-aluminum alloy, pouring speed is a very important factor. A reasonable pouring speed can effectively reduce the defects and cracks in the casting and improve the quality and performance of the casting. Therefore, how to reasonably control the pouring speed has become an important issue. First, the influence factors of pouring speed and melt flow need to be considered. Generally speaking, the faster the pouring speed, the higher the fluidity of the melt, and bubbles and inclusions are prone to occur. At the same time, too fast pouring speed will also lead to too high surface temperature of the casting, thus affecting the quality and appearance of the casting. Therefore, an appropriate pouring speed should be selected to ensure the quality and performance of the casting. Secondly, the influence of pouring speed on the melt flow of different parts should also be considered. Different parts have different cooling rates and crystallinity distribution, so the pouring speed should also be different. Finally, attention should also be paid to the change law of pouring speed and its relationship with other process parameters. By comprehensively considering these factors, a more scientific and reasonable pouring speed scheme can be formulated to achieve better results.
5. Conclusion
This study has conducted in-depth research on the casting process and casting quality of magnesium-aluminum alloy and drawn the following main conclusions: First, in the casting process of magnesium-aluminum alloy, due to the influence of factors such as high melting point and easy oxidation, common defects such as bubbles and cracks are prone to occur. Secondly, to avoid these defects, effective measures need to be taken for treatment. For example, the quality of the casting can be controlled by adjusting parameters such as pouring speed, temperature, and pressure; vacuum or inert gas technology can also be used to reduce the gas content. In addition, the selection of materials and the design of formulations also need to be strengthened. Finally, it is also found that magnesium-aluminum alloy has high strength and corrosion resistance, so it can be widely used in practical applications. However, it should be noted that under different production conditions, there may be some special problems that need to be further solved.
In the future, with the continuous development of science and technology, the casting process of magnesium-aluminum alloy will be further improved and optimized, and the quality and performance of magnesium-aluminum alloy castings will also be continuously improved. At the same time, more attention should be paid to the research and development of new magnesium-aluminum alloy materials to meet the needs of different fields.
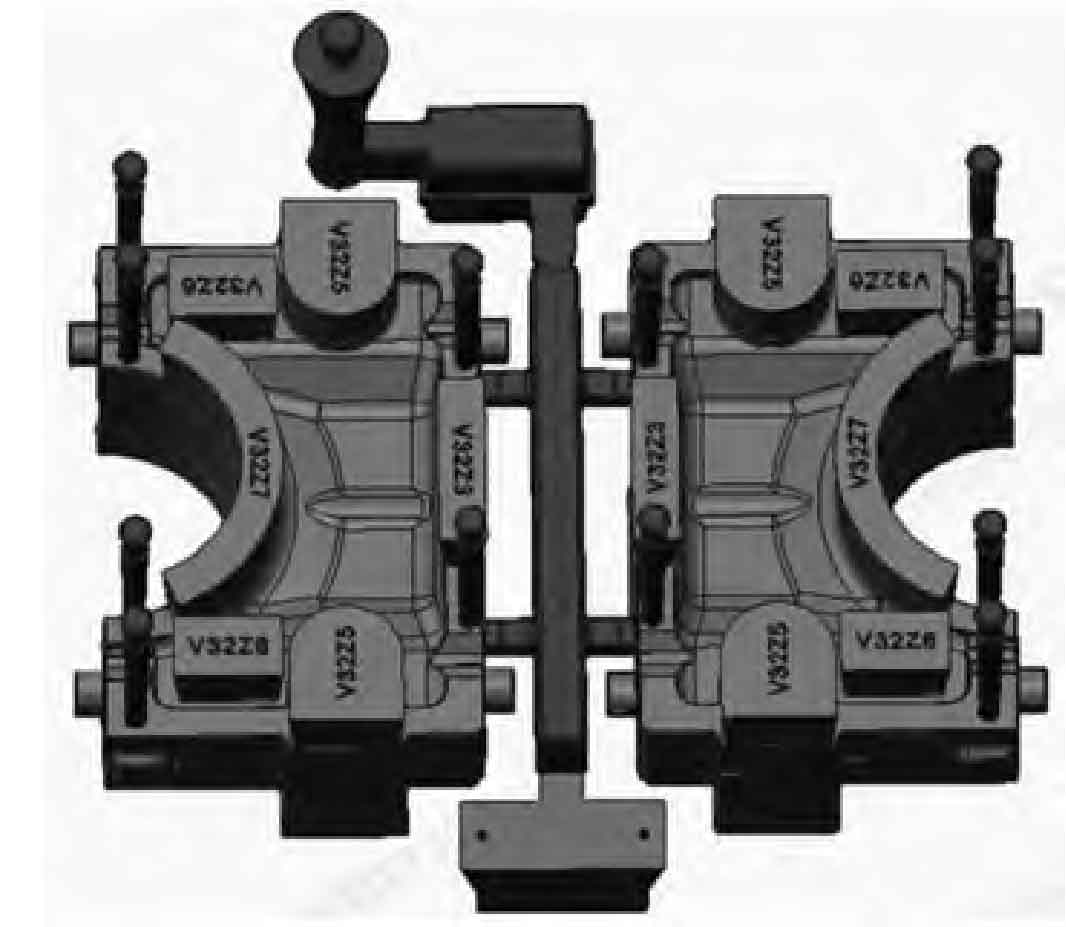