ZL101A aluminum alloy is a commonly used cast aluminum-silicon-magnesium alloy, which has good fluidity, small shrinkage, low hot cracking tendency, and good mechanical properties and corrosion resistance after metamorphic refinement and T6 heat treatment. The material has It is widely used in the field of commercial vehicle parts, providing effective material support for the lightweight of commercial vehicles. The low-pressure casting process is an anti-gravity casting method, in which the molten metal is filled from the bottom up, and the filling speed is controllable and effective It avoids churning, impact and splashing of molten metal, and reduces the formation of oxidized slag. The molten metal is filled under pressure, which can improve the fluidity of the molten metal, and the formability of the casting is good, which is conducive to the formation of high-performance castings with clear contours, smooth surfaces and dense structures. The author of the low-pressure casting ZL101A variant The shrinkage defects of the castings in the back cover of the speeder are analyzed, the causes of the defects are analyzed and the corresponding improvement measures are proposed, so as to provide effective technical support for the production of high-quality castings.
1 Introduction to transmission back cover castings
The transmission back cover casting produced by the author is mainly used in AT automatic transmissions for commercial vehicles, the material is ZL101A, the casting dimensions are 420 mm×410 mm×160 mm, and the structure is shown in Figure 1. The castings are produced by metal low-pressure casting process, and the mold structure is shown in Figure 2show.
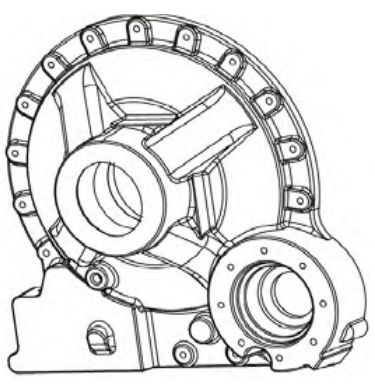
Figure 1 3D model of the casting
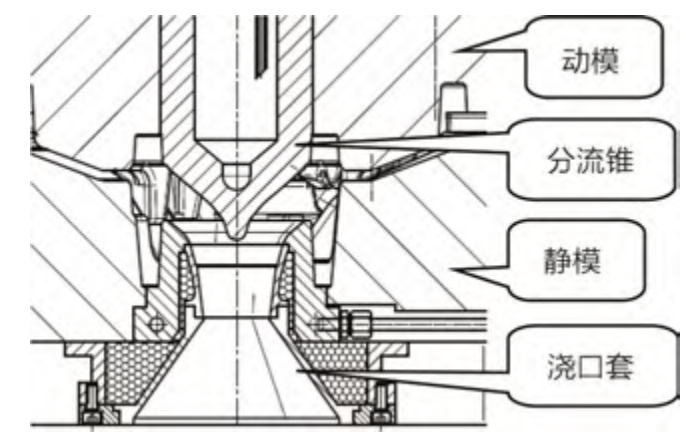
Figure 2 Schematic diagram of the mold structure
2 Analysis of porosity defects and their causes
The casting was detected by X-ray flaw detection, and the crater part is shown in Figure 3, and the anatomical porosity defect of the casting body is shown in Figure 4. The grade of the crater defect in this area has exceeded the ASTM E155 standard Level 3 or above requirements, unacceptable defects for customers.
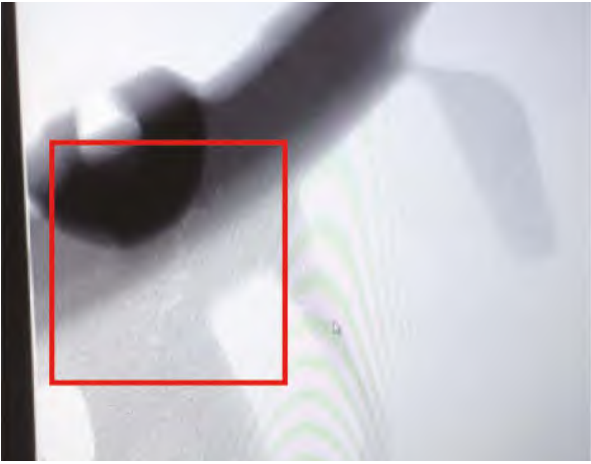
Figure 3 X-ray of a casting to detect crater defects

Figure 4 Anatomical porosity defects in castings
The main reason for the crater defects in this part was preliminarily analyzed, and the average wall thickness of the casting was 7 mm, but the diameter of the hot joint here exceeded 30 mm, and the molten aluminum could not be effectively reshuffled during the pouring process. In order to eliminate the crater defect in this part, it is necessary to improve the filling conditions of this part, which can be increased by adding local cooling or increasing The way to solve the problem of the retracting channel.
3 Improvement measures and analysis
3.1 Increase local cooling of the mold
According to the structural characteristics of the mold, the insert is cut to increase local cooling at the position of the upper mold core corresponding to the shrinkage hole of the casting, as shown in Figure 5.
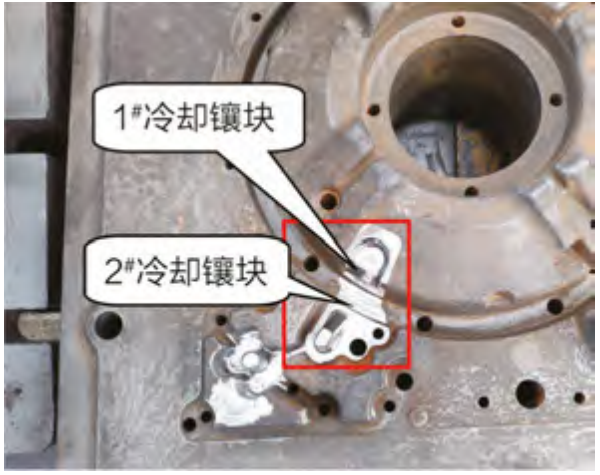
Fig. 5 Cooling inserts are added to the mold
After the mold is changed, the pouring verification is carried out, and the main idea of the pouring process parameter setting is to use a larger holding pressure and a faster pouring speed to solidify the casting under higher pressure, improve the density of the structure, and reduce shrinkage
pore tendency; The 1# insert is air-cooled, and the 2# insert is water-cooled to improve the local cooling rate of the casting and reduce the crater defects.
During the pouring process, it was found that after the cooling was opened, the pouring rhythm was particularly sensitive to the influence of the casting quality, and the appearance of the casting would be cracked if there was a slight pause in the pouring process. The overall yield of castings is not ideal, and trial production It turned out that porosity defects could not be completely eliminated by adding local cooling to the mold alone.
3.2 Optimization of local structure of castings
In order to completely eliminate the crater defects, it is necessary to optimize the local structure of the back cover casting to increase the aluminum-liquid shrinkage channel. The solidification simulation analysis of the structure before and after optimization was carried out with MAGMA software, and the structure before and after optimization was compared Solidification simulation results of castings to determine the optimal change scenario.
(1) Before the solidification simulation analysis of the original scheme (as shown in Figure 6), the solidification simulation analysis was carried out by MAGMA software in the scheme before the optimization of the casting structure, and the final shrinkage porosity tendency value of the casting after solidification is shown in Figure 7, and the “shrinkage porosity value” of a defective part is “11 622”, which is the part It is also the shrinkage hole part in actual production; b. The “shrinkage porosity” of the defective part is “5”. 872″, the B part can be completely eliminated by air cooling measures in the actual production process.
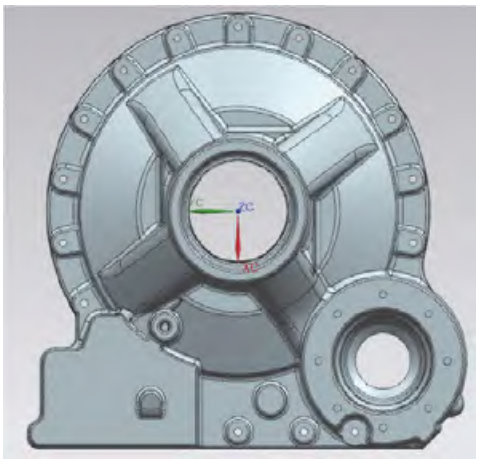
Figure 6 The original structure of the casting
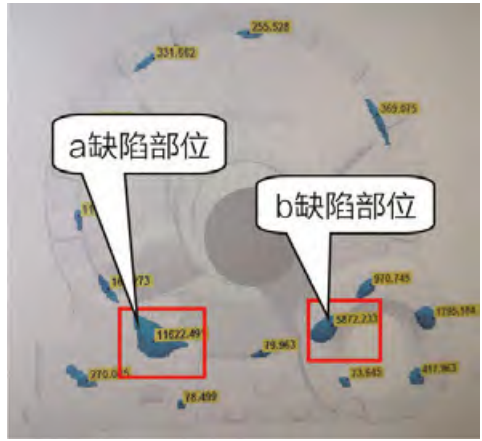
Fig. 7 Simulation results of solidification of the original structure of the casting
(2) Optimization scheme 1: solidification simulation analysis
The first structural optimization scheme is to fill the filling channel 3~5 mm upwards (as shown in Figure 8). After the simulation, the “shrinkage porosity” of the defective part A is “10 006” (as shown in Fig. 9), and it is judged that the shrinkage porosity defect cannot be completely eliminated by cooling fit according to the experience of preliminary trial production.
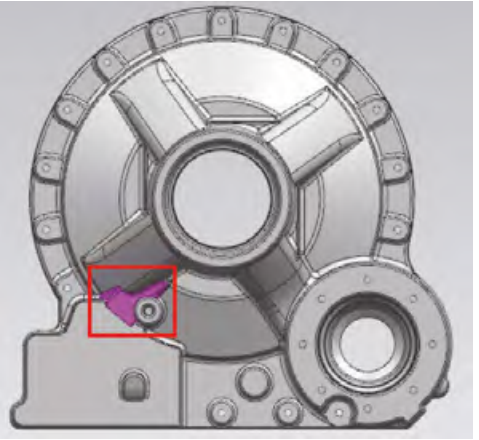
Figure 8 Structural Optimization Scheme 1
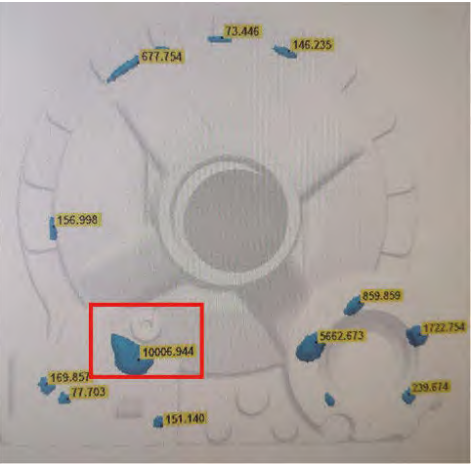
Figure 9 Optimization scheme 1 solidification simulation results
(3) Solidification simulation analysis of optimization scheme 2
The second option is to add a 15 mm × 5 mm retraction boss (as shown in Figure 10) to the first option, which is the maximum size of the structure that can be changed to the customer. After the simulation, the “porosity value” of the defect part of a is “8”.025″ (Fig. 11), judging from experience, with the cooling of the insert on the mold, the shrinkage hole defect can be eliminated.
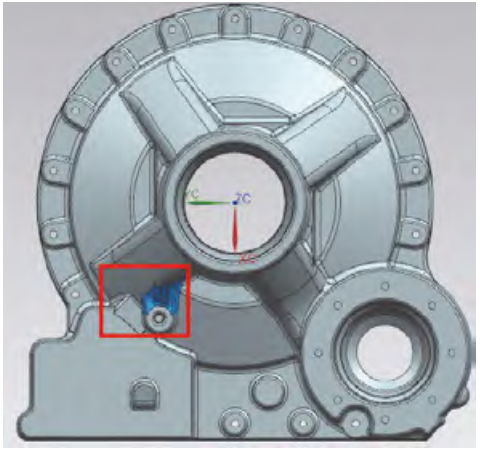
Figure 10 Structural Optimization Scheme 2
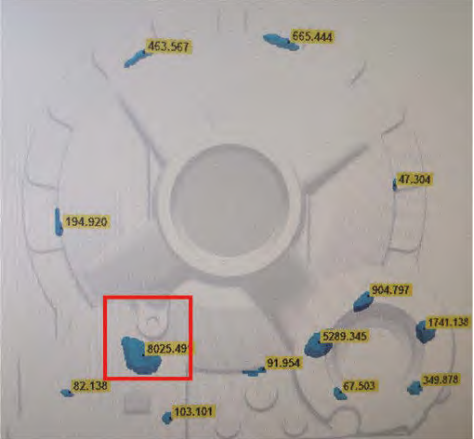
Figure 11 Solidification simulation results of optimization scheme 2
In summary, the second structural optimization scheme was used for production verification.
4 Production verification and effect
After the casting structure optimization scheme is determined, the mold is changed, and the pouring process parameters are optimized according to the quality of the previous pouring process: the original 4-stage pouring process is changed to 5 stages, and the molten aluminum rises When the height of the shrinkage porosity defect is reached, the pouring speed is reduced to reduce the back pressure in the cavity, and the filling pressure and time of each stage are corrected. The pouring temperature of the molten aluminum was reduced by 10 °C to increase the pace of pouring production; To stabilize the mold temperature gradient, the 2# insert cooling is set to air cooling. 6 shifts in continuous production, X-ray flaw detection on all castings, The first shift begins pouring, and there is an outside during the ironing process Observe the shrinkage crack defects, and gradually return to normal after pouring 3 molds. The trial production verification was carried out in 6 shifts, 195 pieces were poured, 188 pieces were qualified, the casting pass rate reached 96.4%, and the shrinkage hole defects were significantly improved.
5 Conclusion
By optimizing the local structure of the casting, adding the shrinkage channel, combining the air-cooled inserts and optimizing the pouring process parameters, the shrinkage porosity defects can be effectively improved. However, the influence of the pouring rhythm on the shrinkage porosity of the casting still exists Completely eliminate porosity defects and minimize pauses during the pouring process.