This article focuses on the critical issue of connecting rod bolt fractures in engines. It comprehensively analyzes the root causes of such fractures, including material – related problems, machining precision issues, appearance quality defects, assembly – quality – related factors, and improper engine usage. Through detailed examination of fracture diagnosis methods and practical prevention measures, it aims to provide a comprehensive understanding for engine manufacturers, maintenance personnel, and users. By implementing these measures, the occurrence of connecting rod bolt fractures can be effectively reduced, enhancing engine reliability and safety.
1. Introduction
Connecting rod bolts are vital components in engines, despite their relatively small size. They endure complex alternating loads during the engine’s operation, which are generated from the combustion – explosion force at the piston top converted into rotational motion. A fracture of a connecting rod bolt can lead to severe consequences, ranging from engine damage to potential threats to human life and property. Therefore, a thorough understanding of the causes of connecting rod bolt fractures, accurate diagnosis of such failures, and effective prevention measures are of great significance.
2. Root Causes of Connecting Rod Bolt Fractures
2.1 Material – related Problems
Connecting rod bolts typically require materials with high strength and impact resistance, such as 38Cr, 40Cr, 35CrMo, etc. These materials are usually quenched and tempered to refine the microstructure, improving toughness and achieving the desired mechanical properties. However, if sub – standard materials are used during manufacturing or if the heat treatment process does not follow the specified procedures, it can create potential hazards for bolt fractures. Table 1 summarizes the common materials for connecting rod bolts and their properties.
Material | Tensile Strength (MPa) | Yield Strength (MPa) | Impact Toughness (J/cm²) |
---|---|---|---|
38Cr | 980 – 1176 | 835 – 980 | ≥49 |
40Cr | 980 – 1080 | 785 – 885 | ≥47 |
35CrMo | 980 – 1176 | 835 – 980 | ≥63 |
35CrMoA | 980 – 1176 | 835 – 980 | ≥71 |
35CrMoV | 1080 – 1275 | 930 – 1080 | ≥55 |
40CrMo | 1080 – 1275 | 980 – 1176 | ≥63 |
2.2 Machining Precision Issues
2.2.1 Perpendicularity and concentricity issues
According to the design requirements of connecting rod bolts, in addition to thread dimensions, positioning dimensions, and effective length dimensions, requirements such as perpendicularity of the hexagonal head shoulder support surface relative to the positioning journal and coaxiality of the thread part relative to the positioning journal are also specified. If the perpendicularity of the shoulder support surface does not meet the requirements, the shoulder support surface cannot be evenly stressed when in contact with the connecting rod cover end face. Instead, it may result in point – contact at the outer edge of the shoulder support surface and the connecting rod cover end face, as shown in Figure 1. This converts the locking tension of the bolt into a bending moment at a single point on the shoulder support surface. Coupled with the load during engine operation, the right – angled part of the hexagonal head shoulder may fracture.
[Insert Figure 1 here: A diagram showing the point – contact between the shoulder support surface and the connecting rod cover end face when the perpendicularity is not met]
If the coaxiality of the thread part and the rod – part positioning journal is not ensured during machining, it can cause interference during assembly with the connecting rod cover bolt hole. This may lead to a “false tight” situation even when the torque wrench is used to reach the specified torque. In operation, the connecting rod cover and the body may loosen, subjecting the bolt to additional impact tension and increasing the risk of fracture.
2.2.2 Fillet transitions and surface roughness issues
The intersection of the rod part and the hexagonal head shoulder support surface, as well as the intersection of the thread position and the fixed journal, are required to have rounded – off transitions and high surface roughness requirements. If the rounded – off transition is not achieved or the surface roughness is poor at the intersection of the shoulder support surface and the rod part, it can become a notch for stress concentration. Once the bolt is subjected to working loads, it is likely to crack or break from this weak area. The same principle applies to other non – equal – diameter intersections. Additionally, a rough bolt surface can also be a source of stress concentration under alternating loads, contributing to bolt fractures.
2.3 Appearance Quality Defects
The appearance of connecting rod bolts should not have burrs, cracks, scars, rust, or other defects. Burrs, whether on the positioning journal or in the threads, can cause significant resistance or even seizing during bolt locking, resulting in false tightness and eventually fatigue fracture. Cracks are a direct cause of bolt fracture. Scars and rust can also cause stress concentration under alternating loads, ultimately leading to fatigue fractures. Table 2 lists the appearance quality defects and their potential impacts.
Appearance Defect | Impact on Bolt |
---|---|
Burrs | Causes resistance during locking, may lead to false tightness and fatigue fracture |
Cracks | Direct cause of bolt fracture |
Scars | Induce stress concentration under alternating loads, increase the risk of fatigue fracture |
Rust | Induce stress concentration under alternating loads, increase the risk of fatigue fracture |
2.4 Assembly – quality – related Factors
2.4.1 Cleanliness issues
During the assembly of connecting rod components, cleanliness is crucial. Foreign matter on the bolt, especially on the positioning rod journal, thread – engaging part, or the shoulder support surface, can cause false tightness when the bolt is tightened. This false tightness can lead to stress concentration at the location of the foreign matter under working loads, resulting in fatigue fracture.
2.4.2 Locking torque issues
The locking torque of connecting rod bolts should be in accordance with the design specifications of each engine model. Insufficient locking torque can cause gaps to form between the connecting rod big end and the cover under alternating loads. This subjects the bolt to additional impact forces and tensile stress, and if the stress exceeds the allowable tensile strength of the bolt, fatigue fracture may occur. On the other hand, excessive locking torque can cause the bolt to yield and deform. This reduces the locking force, and the bolt may be damaged or fractured due to excessive elongation under impact loads during engine operation.
2.4.3 Mate clearance issues
If the fit between the positioning journal on the connecting rod bolt and the bolt hole on the connecting rod cover is not tight and the clearance is too large, the cover may shift due to centrifugal force during engine operation. This subjects the bolt to additional shear forces, increasing the likelihood of bolt fracture. A large clearance between the connecting rod bearing hole and the journal can also generate significant additional impact loads, which may cause the bolt to break. Table 3 summarizes the assembly – quality – related factors and their impacts.
Assembly – related Factor | Impact on Bolt |
---|---|
Foreign matter in assembly | Causes false tightness, leads to stress concentration and fatigue fracture |
Insufficient locking torque | Causes gaps between the connecting rod big end and the cover, subjects the bolt to additional impact and tensile forces, may lead to fatigue fracture |
Excessive locking torque | Causes bolt yield and deformation, reduces locking force, may lead to bolt damage or fracture due to excessive elongation |
Large fit clearance between positioning journal and bolt hole | Causes cover shift, subjects the bolt to additional shear forces, may lead to bolt fracture |
Large fit clearance between bearing hole and journal | Generates additional impact loads, may cause bolt fracture |
2.5 Improper Engine Usage
Long – term overloading, excessive loading, or long – term runaway of the engine can subject the connecting rod to extreme alternating loads. In such cases, the bolt, as the weakest part of the connecting rod, is likely to fracture.
3. Diagnosis of Connecting Rod Bolt Fracture Accidents
3.1 Examination of the Fracture Macro – structure
3.1.1 View the location of the fracture
By observing the location of the fracture, it is possible to infer the potential causes. If the fracture occurs at the intersection of the hexagonal head shoulder and the rod part, it may be due to issues such as non – compliant rounded – off corners, rough surfaces, cutting tool marks, or cracks. A fracture in the rod part may be related to material defects, poor surface roughness, or heat treatment processes. Fractures in the thread part are common. Residual tool marks or sharp corners during thread machining, burrs or uncleanliness during assembly, and improper locking forces can all cause fractures in this area. Table 4 summarizes the relationship between fracture locations and potential causes.
Fracture Location | Potential Causes |
---|---|
Intersection of hexagonal head shoulder and rod part | Non – compliant rounded – off corners, rough surface, cutting tool marks, cracks |
Rod part | Material defects, poor surface roughness, heat treatment issues |
Thread part | Residual tool marks or sharp corners during machining, burrs or uncleanliness during assembly, improper locking forces |
3.1.2 Check the fracture status
If the fracture shows obvious plastic deformation, it may indicate problems with the bolt locking force. Insufficient locking force can cause the connecting rod and the cover to have a gap, increasing the load on the bolt and leading to fatigue fracture. Excessive locking force can cause the bolt to yield and deform, and under load, it may break due to excessive elongation. If the engine has been operating under long – term overload or runaway conditions, the bolt may also show signs of fatigue fracture with plastic deformation.
If there is no obvious plastic deformation, further examination of the fatigue lines and regions can be carried out. A fatigue – fractured bolt typically consists of two regions: a fatigue crack initiation and propagation region with fine and bright metal grains and shell – like stripes, and a sudden fracture region with coarse metal grains. If the fracture is caused by stress concentration due to external damage marks, small notches during machining, or internal material defects, the fatigue crack propagation region is usually smaller, and the sudden fracture region is larger. Figure 2 shows a typical fatigue – fracture appearance.
[Insert Figure 2 here: A diagram showing the two regions of a fatigue – fractured bolt]
3.2 Testing of Residual Connecting Rod Bolt Parts
3.2.1 Tensile test
If a tensile test can be performed on the remaining bolt, if the tensile strength is insufficient, it can be directly determined that there is a material problem. However, if the tensile strength is sufficient, other factors need to be considered in combination with existing phenomena.
3.2.2Material composition test
Material composition analysis can be carried out to check if there is a mismatch in material grades.
3.2.3Metallographic structure inspection and hardness testing
Metallographic structure inspection and hardness testing can be used to determine whether the material structure after heat treatment meets the requirements. Through comprehensive analysis of fracture inspection, location observation, material grade confirmation, and metallographic structure and mechanical property tests, it is possible to accurately determine whether the problem lies in the material, machining, or assembly process.
4. Prevention Measures
4.1 Supplier Evaluation and Agreement
When purchasing connecting rod bolts or connecting rod assemblies, the user should assess the production capacity and quality of the supplier and sign technical and quality assurance agreements. This helps to ensure that the purchased products meet the required standards.
4.2 Incoming Inspection
For each batch of incoming goods, sampling inspections should be carried out in accordance with national standards. These inspections should include material composition analysis, tensile strength testing, metallographic structure inspection, hardness testing, and non – destructive testing to ensure that the materials meet the requirements. Table 5 shows a sample incoming inspection plan.
Inspection Item | Inspection Method | Standard Requirement |
---|---|---|
Material Composition | Chemical analysis | Conform to specified material grade |
Tensile Strength | Tensile test | Meet the minimum specified value |
Metallographic Structure | Metallographic microscopy | Conform to the standard microstructure after heat treatment |
Hardness | Hardness testing | Within the specified hardness range |
Non – destructive Testing | Ultrasonic testing, magnetic particle testing, etc. | No cracks or other defects detected |
4.3 Dimensional acceptance
Dimensions should be inspected according to the design drawings. Special attention should be paid to checking items such as the perpendicularity of the bolt shoulder support surface, rounded – off transitions, positioning journal dimensions, thread dimensions, coaxiality of the thread with respect to the positioning journal, surface roughness, and burrs. Records should be kept for each inspection item.
4.4 Cleaning process
Before assembly, a cleaning process should be carried out to remove impurities and cutting residues adhering to the threads. This helps to ensure proper tightening and prevent false tightness.
4.5 Assembly process control
During the assembly of connecting rod bolts, attention should be paid to the fit between the bolt and the cover. If the fit is too tight or too loose, the bolt should be removed, set aside, and not used. A torque wrench or locking torque device should be used correctly according to the assembly technical specifications and process requirements. The two bolts on the connecting rod should be tightened gradually, alternately, and evenly to the specified torque to ensure that the connecting rod bolts are properly tightened through ideal elastic deformation.
4.6 Commissioning and anomaly detection
Although connecting rod bolt fractures are sudden events, experienced or careful test – run operators may notice abnormal engine operation before a major failure occurs. Signs such as unstable engine operation, abnormal noises, poor combustion or non – combustion in the faulty cylinder (resulting in black smoke emission) can be indicators of potential problems. Early detection of such abnormalities during the engine test – run and prompt shutdown for inspection and repair can prevent dangerous accidents and reduce economic losses.
4.7 Regular maintenance
During regular engine maintenance, attention should be paid to checking whether the connecting rod bolts are loose, worn, deformed, or have any appearance quality issues. Bolts with defects should not be used and should be replaced in a timely manner.
5. Conclusion
Connecting rod bolts play a crucial role in engine operation. Although it is difficult to detect potential fractures in advance, by understanding the root causes of connecting rod bolt fractures, accurately diagnosing fracture accidents, and implementing effective prevention measures, the occurrence rate of connecting rod bolt fractures can be significantly reduced. This helps to enhance the reliability and safety of engines, ensuring smooth operation and minimizing the risk of accidents. Engine manufacturers, maintenance personnel, and users should all pay close attention to these aspects to ensure the long – term stable operation of engines.
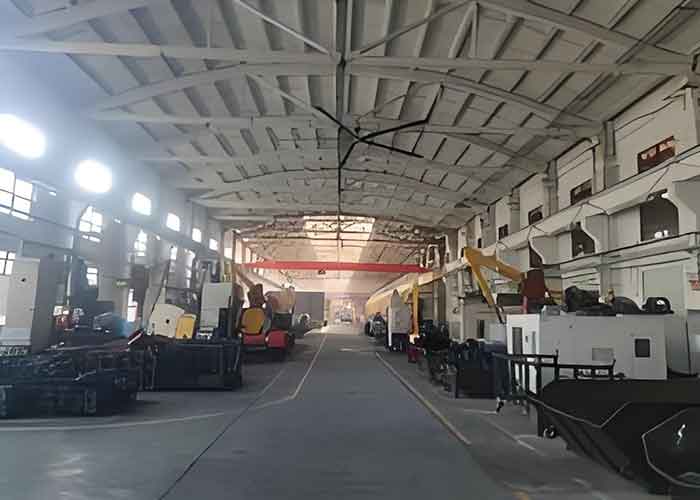