Cast diaphragms are the main stator components in centrifugal compressors. According to the different arrangement positions and functions of cast diaphragms, they are divided into intake diaphragms, exhaust diaphragms, interstage diaphragms and intermediate diaphragms. The object of study is the intake baffle, which is used to form an intake chamber with the cylinder to guide the medium gas to the impeller inlet. In the process of gas flow, the gas pressure gradually increases, which forms a pressure difference on both sides of the casting diaphragm. The pressure difference increases the stress at the joint between the outer side of the casting diaphragm and the casing, and at the same time causes a large axial deformation and radial deformation of the casting diaphragm. In some units, there have been accidents such as the fracture of the stop position of the casting diaphragm, the rubbing between the casting diaphragm and the adjacent impeller due to the axial deformation, and the damage of the seal of the mouth ring due to the radial deformation of the casting diaphragm.
The analysis of the researchers on the casting diaphragms mainly focuses on the design stage of the casting diaphragms and the accident analysis stage after the casting diaphragms are damaged. Liu Chaoshan used the fault analysis theory to diagnose the looseness of the casting diaphragm of the CO2 compressor. Gu Hailing and Wang Guangxiang analyzed the damage of the casting diaphragm of the high-pressure cylinder of the feed gas compressor. Kuang Zhonghua et al. put forward two reliability design and calculation methods for casting diaphragms in view of the accident caused by the problems of casting diaphragms in the field operation of centrifugal compressors. Hou Yong analyzed the failure of high-pressure cylinder diaphragm of cracked gas compressor. However, there is little research on the analysis and treatment methods of casting diaphragms after problems occur in production and manufacturing.
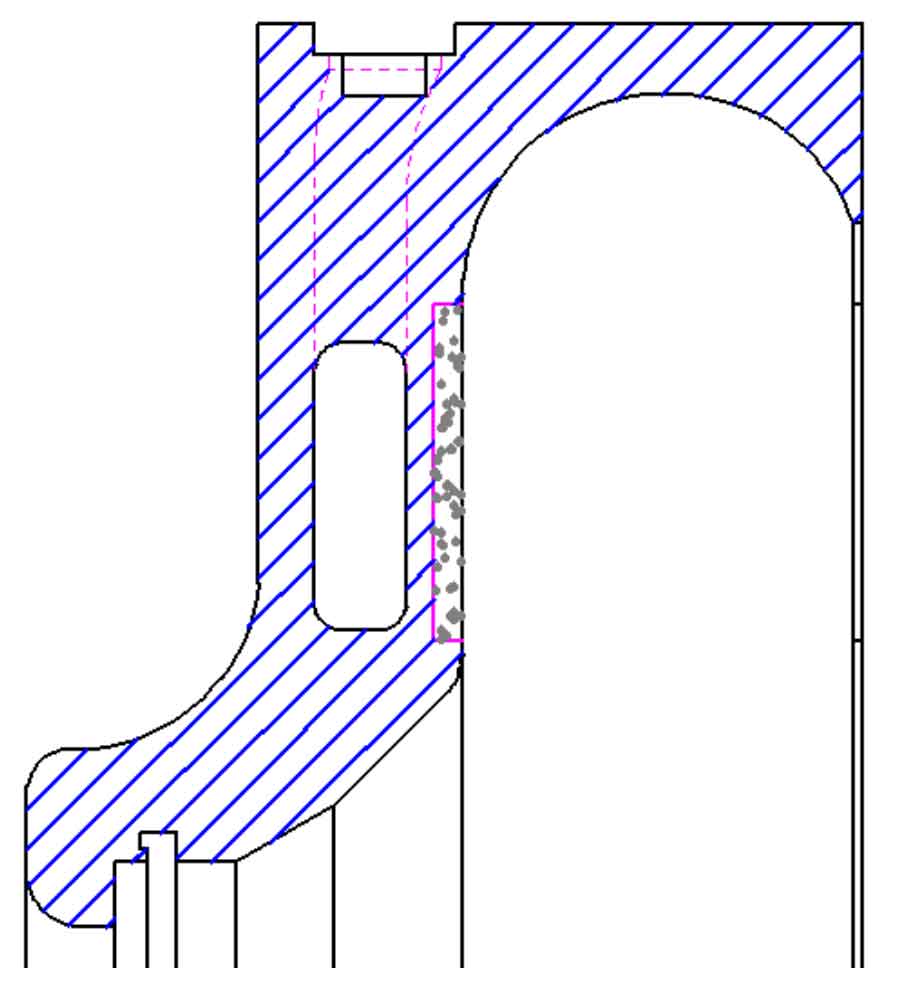
In addition, there are several special points between the analyzed casting diaphragm and the conventional design casting diaphragm, which should be noted in the analysis. First, the casting diaphragm adopts hollow design. A cavity is formed in the middle of the casting diaphragm, and rib plates are used to connect the casting diaphragm in the cavity area.
The repair method for sand hole is to mill out the sand hole area, and then repair weld the components with the same size. The stress and deformation of the repaired cast diaphragms will be different from those before repair welding. In order to know whether the cast diaphragms after structural modification can meet the operation requirements of the unit without problems such as rubbing and damage, it is necessary to analyze the mechanical properties of the cast diaphragms before and after repair welding. In this paper, the finite element method is used to analyze the casting diaphragms, so as to determine the appropriate cutting thickness to make the casting diaphragms meet the requirements of stress and deformation.