The ductile iron front cover is made of QT700-2 and is produced using a green sand process. Because the hardness of the green sand mold is not as good as that of the iron sand coating process, the self-replenishment of ductile iron cannot be fully realized in the solidification process of the casting, and corresponding anti-shrinkage measures need to be taken. In the early stage of production, our factory uses cold iron process to solve the problem of shrinkage porosity inside the casting. However, in mass production, it was found that the cold iron process was not only costly, but also unstable in quality, and the porosity and crater were wasted The proportion of products is high. The original process has been improved, and the problem of shrinkage and porosity inside the front cover has been completely solved to ensure the stable production of the product.
1 Initial casting process design
The front cover is made of QT700-2 with a basic wall thickness of 9 mm, a bottom flange wall thickness of 40 mm, and a top wall thickness of 23 mm, with four independent hitches with uneven wall thickness (Fig. 1). The parting surface is selected at the flange surface position near the middle according to the conventional design, the small end of the casting is placed in the upper box, the large flange and the sand core head are placed in the lower box (Fig. 2), the inner sprue enters the cavity from the large flange face, and the inner cavity adopts manual self-hardening sand integral sand core. According to the structural characteristics of the front cover, the diameter of the outer flange is about 450 mm, the average wall thickness is 40 mm, and there is a thick annular hot joint, so the process design adopts the combination of riser and external cold iron to eliminate the hot joint at this position. The two side risers are designed as 60 mm×80 mm× 70 mm crimping risers, and six external cooling irons are set in the sand core for quenching, so as to eliminate the hot joints at the flange ring position and make the whole flange ring solidify sequentially. The top flange hot joints are concentrated at four independent laps, and the design uses the placement of internal cooling iron to solve the shrinkage and porosity, and the front cover mold is shown in Figure 3.
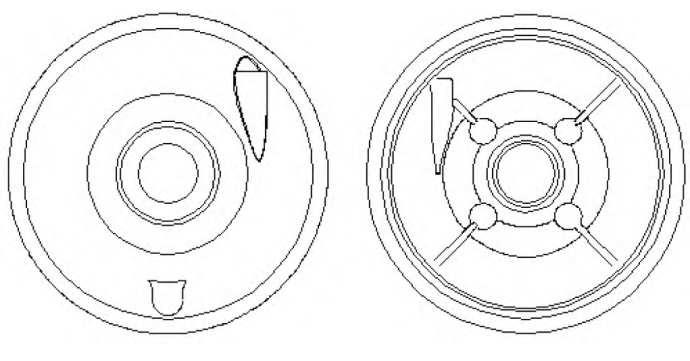
Fig.1 Front cover structure
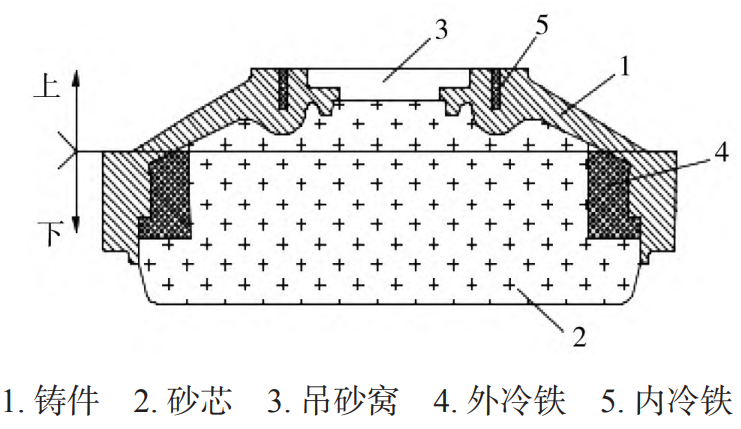
Fig.2. Initial process of front cover
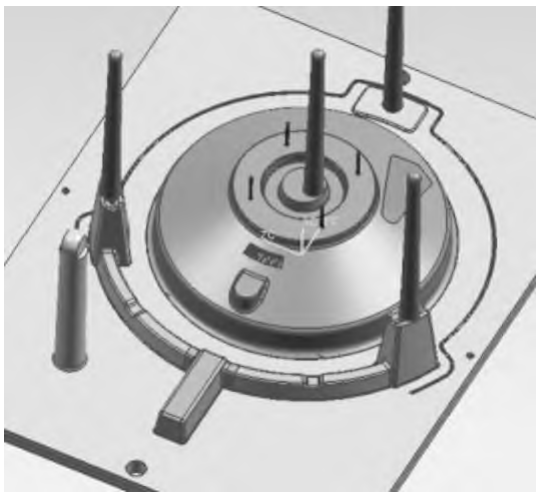
Fig.3. Front cover mold
In the trial production stage, there were no shrinkage defects inside the product after dissection, and it was recognized by customers. However, in the mass production stage, the product quality fluctuates greatly: (1) the quality is unstable. In the product concentration, there are waste products such as shrinkage holes (Fig. 4), porosity, and cold iron deflection at the top of the cold iron, and the comprehensive scrap rate is as high 15%。 After dissection, it was found that although the top four independent hitchhikers were placed under the inner cold iron, there was always a certain proportion of the product that would still have shrinkage and looseness in the cold iron position; In addition, the pores at the location of the internal cooling iron are also relatively concentrated. (2) Low production efficiency. During the production of this product, 6 pieces of cold iron are required in the core (Fig. 5), and the core making efficiency is low. During the molding production, it is also necessary to manually lower the internal cooling iron, which is complex to operate and seriously affects the production efficiency.
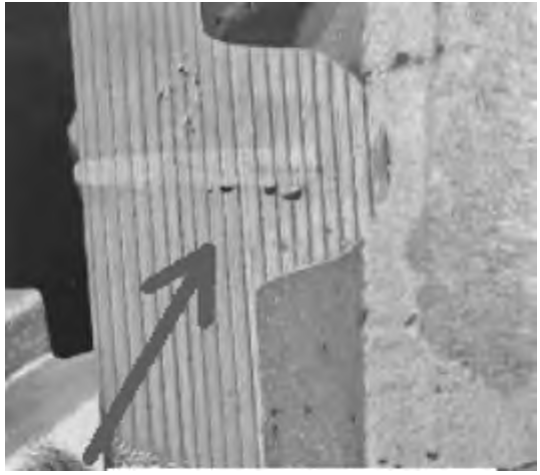
Fig.4. Shrinkage porosity of castings
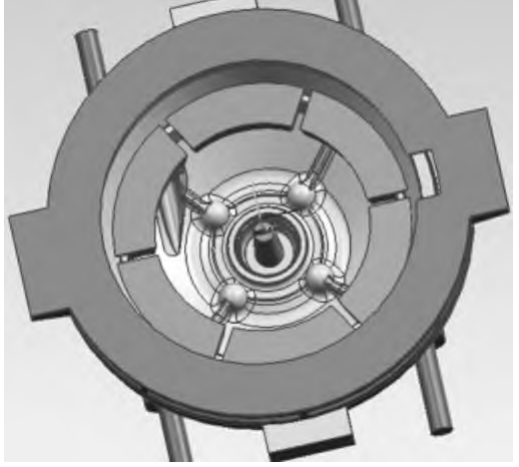
Fig.5. Self-hardening sand core box and chilled iron
2 Analysis of results
The main reason for the low production efficiency of this process is that a large number of cold iron is used in production, in which the outer cold iron needs to be manually put into the core box when the self-hardening sand core is made, which seriously restricts the core making efficiency of manual self-hardening sand core; The inner cooling iron at the top four independent laps needs to be manually inserted during modeling cavities, which greatly affect the production efficiency during molding. The main reasons for the unstable product quality and the concentrated casting defects at the top four laps (Fig. 6) are: (1) The quality of the inner chilled iron entering the cavity is not controlled. According to the product structure, the process design of the inner cold iron needs to be vertically lowered into the upper box cavity, which has strict requirements for the depth and verticality of the cold iron inserted into the cavity. However, limited by the current production line, the internal cooling iron is inserted into the cavity by artificial means, and the quality of the cold iron entering the cavity has a great deviation: the size of the casting under the internal cooling iron is too short, and the shrinkage can not be eliminated, and it is too long or too skewed, so it can not be completely processed, resulting in the scrapping of the casting. (2) The quality of the chilled iron is not controlled. The internal cooling iron is the purchase of finished parts, and its dimensions are A certain deviation, when the deviation is too large, it will affect the cooling effect of the cold iron; The internal cooling iron needs to be re-baked before use to remove surface moisture. However, it is inevitable that there will be rust and pollution on the surface during the production, storage and use, and a large amount of gas will be produced when the molten iron is poured, resulting in pores around the cold iron, and the casting will be scrapped when the area is too large. (3) Destroy the cavity. When the internal cooling iron is manually inserted into the cavity, it is easy to touch the sand tire at the root of the cold iron bad, resulting in sand hole defects around the cold iron.
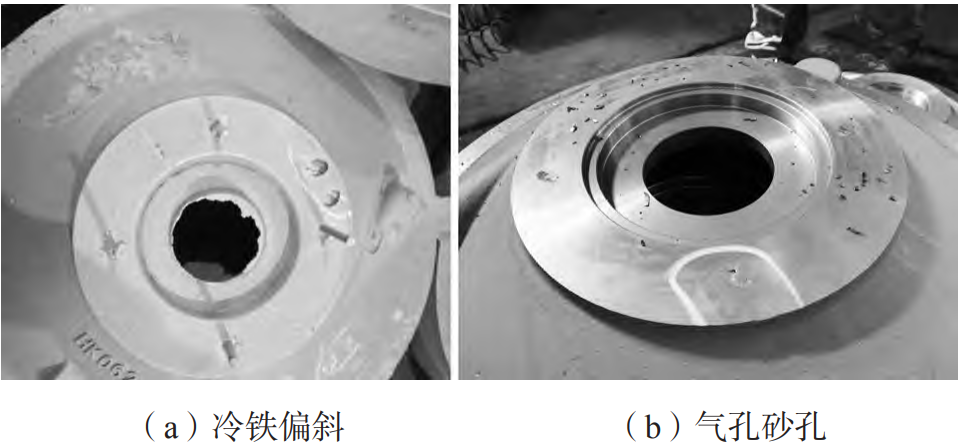
Fig.6. Defects caused by internal cooled iron
3 Process optimization plan
The process improvement is mainly carried out from two aspects: (1) reduce the amount of cold iron, and the hot joint at the flange ring is repaired and shrunk through the riser as much as possible; Internally cooled iron is changed to externally cooled iron. (2) The overall sand core is changed to hanging sand to reduce costs and improve production efficiency. The specific improvement plan is as follows.
(1) Improvement of anti-shrinkage design of castings. For the annular hot joint at the flange ring, the cold iron in the inner cavity is canceled, and a large riser is set on the side of the flange for reshuffling. Through the calculation of the modulus and hot joint of the casting, in order to meet the requirements of the casting, the riser size is designed to be Φ80 mm×140 mm, and the riser diameter The dimensions are designed to be Φ25 mm×20 mm. For the top flange hitch In the hot section, the internal cooling iron is canceled and the external cooling iron is replaced by the external cooling iron, and the side riser is replenished and contracted. Since the four hitters are four independent thick hot joints relative to the top flange, the outer cold iron cannot be simply designed as an annular sheet cold iron, because the annular cold iron has the same cooling effect on the flange and the hitch, and the four hitters are still in a relative hot joint state at this time. Therefore, the cold iron is designed into four independent ones Block chilled iron, quenched for each of the four hitches.
(2) The overall sand core is changed to hanging sand. After the flange ring cold iron is canceled, only the oil groove in the inner cavity of the front cover needs to use a sand core, and the rest of the parts can be realized by the sand hanging process. Therefore, the process design of the product is re-designed, the parting surface is still selected on the flange surface, the castings are all placed in the lower box, the inner cavity of the casting is formed by hanging sand, and a small sand core is placed in the local oil groove. This design reduces the weight of the sand core from 33 kg to 0.5 kg, which greatly reduces the cost of core making. After process optimization, through production verification, the problem of shrinkage porosity of castings has been better solved, and the waste products such as sand holes and porosity of the product have also been significantly reduced. The mass production quality of the products is stable, which well meets the needs of customers.
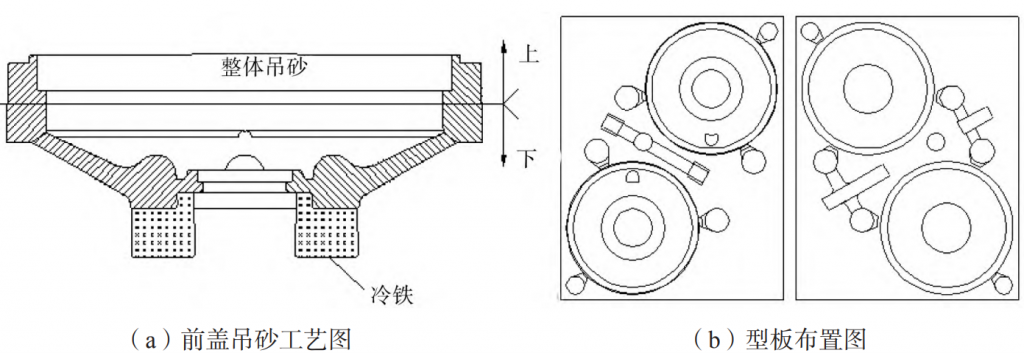
Fig.7. Optimize the process
4 Conclusion
(1) When the internal cooling iron is manually lowered into the cavity, it is not suitable for mass production. When solving the problem of shrinkage porosity of castings, internal coolant iron has high requirements for the depth and verticality of the inserted cavity, which is only suitable for single
piece or small batch production verification. In mass production, internal cooling iron is easy to cause unstable product quality, and there are waste products such as skew, porosity, and sand holes
Product.
(2) The use of external cooling iron will reduce the production efficiency of the product, because:
Therefore, when designing the casting shrinkage, the hot riser is used as much as possible
Shrinkage, which can greatly improve production efficiency.