During the casting process of a batch of castings with a nominal pressure of 26 MPa and super dual-phase steel special material task, the shell strength and air tightness tests were carried out after the casting finished the machining stage, and it was found that the pressure in the middle cavity could not be maintained. It is found that there is shrinkage defect at the connection between the valve body and the rib plate after inspection with the macro display. See Fig. 1 for the specific location.
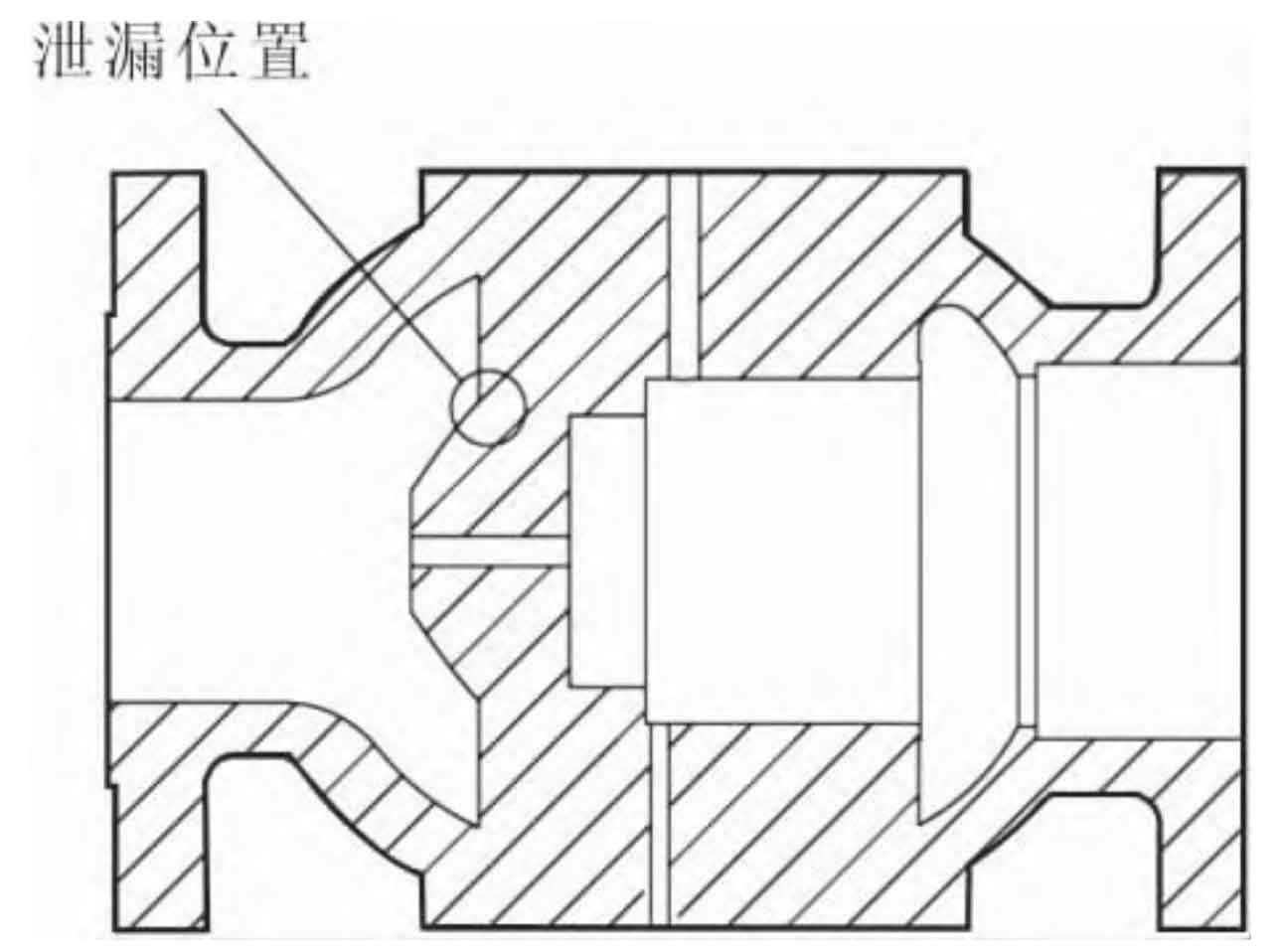
In view of the above situation, the current casting process was simulated and analyzed using the MAGMA casting simulation software to explore the causes of shrinkage porosity. According to the simulation results of the MAGMA casting simulation software, under the current casting process, there are many shrinkage holes and porosity defects in the valve body cavity, and the defect rate reaches about 20%. The dark part in Figure 2 indicates the position where the defect is prone to occur. As shown in Figure 2, the defect at the connection between the rib plate and the inner cavity is the most serious, which corresponds to the actual leakage position. At the same time, the simulation results show that there is also the possibility of different degrees of looseness at other positions, and the distribution is scattered, which is not easy to repair. This is due to the following two reasons:
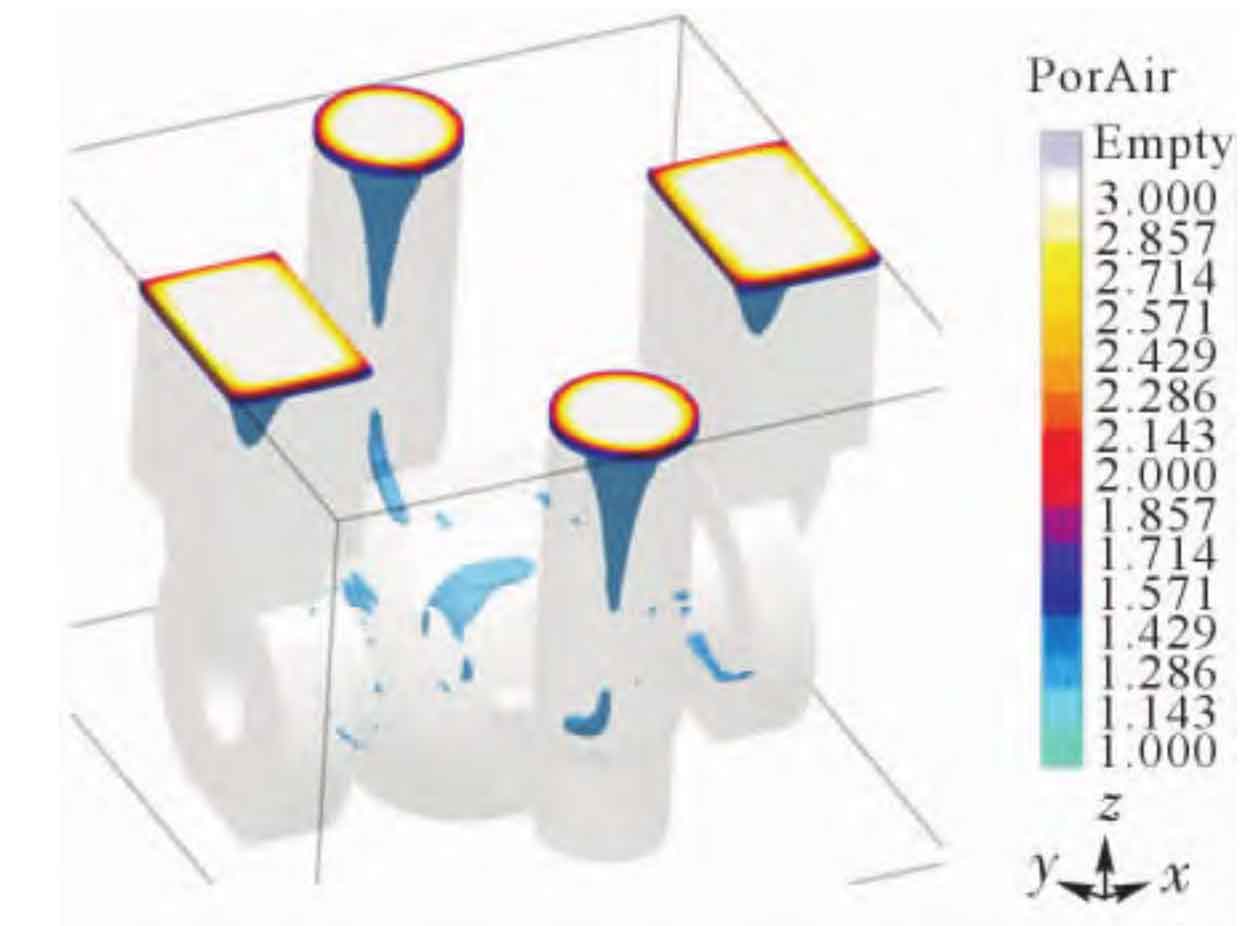
① The design of the gating riser in the gating system is too small. The valve body has a complex internal cavity structure. During the design of the gating system, the gating and riser can only be set at 2 flanges and 4 upper and lower bosses for easy fixation. Therefore, the gating channel is limited, and the castable cannot fill the entire mold in time.
② The feeding system design is not fully considered. In this task, the nominal pressure of the valve body reaches 26 MPa, the wall thickness exceeds 45 mm, and the wall thickness of the valve body at different positions varies by about 15 mm. During pouring, it is very easy to cause the pouring channel to cool and solidify first, resulting in insufficient shrinkage at the leakage, thus forming loose casting defects during solidification.