Through analysis and research on the structure and technical requirements of the steel casting, the following casting difficulties are obtained:
(1) The minimum width of the steam inlet chamber is only 55 mm, and there is a large flange on the back, with a maximum thickness of 280 mm. Here, the hot spot is large, which is prone to sand and slag inclusions. The chamber is small and difficult to clean, and the cleanliness requirements for the steam inlet chamber are high, as shown in Figure 1.
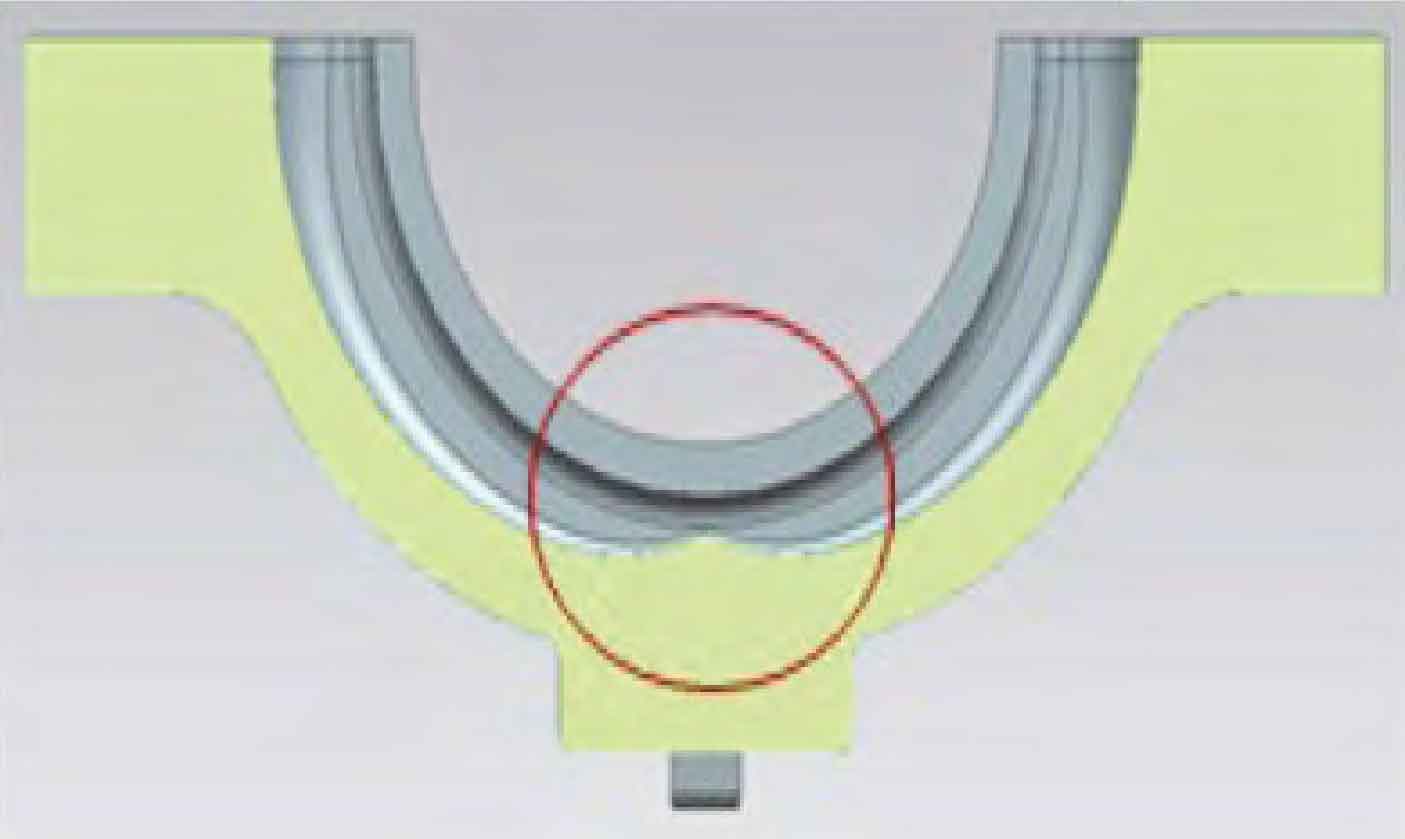
Solution: To ensure the shrinkage of the large flange on the back and reduce the risk of sand sticking in the inner cavity, a riser wall and low carbon insulation bricks are used for the inner cavity.
(2) The large flange at the back of the cylinder has a large hot spot, making it difficult for the liquid steel to feed in the circumferential direction, as shown in Figure 2.
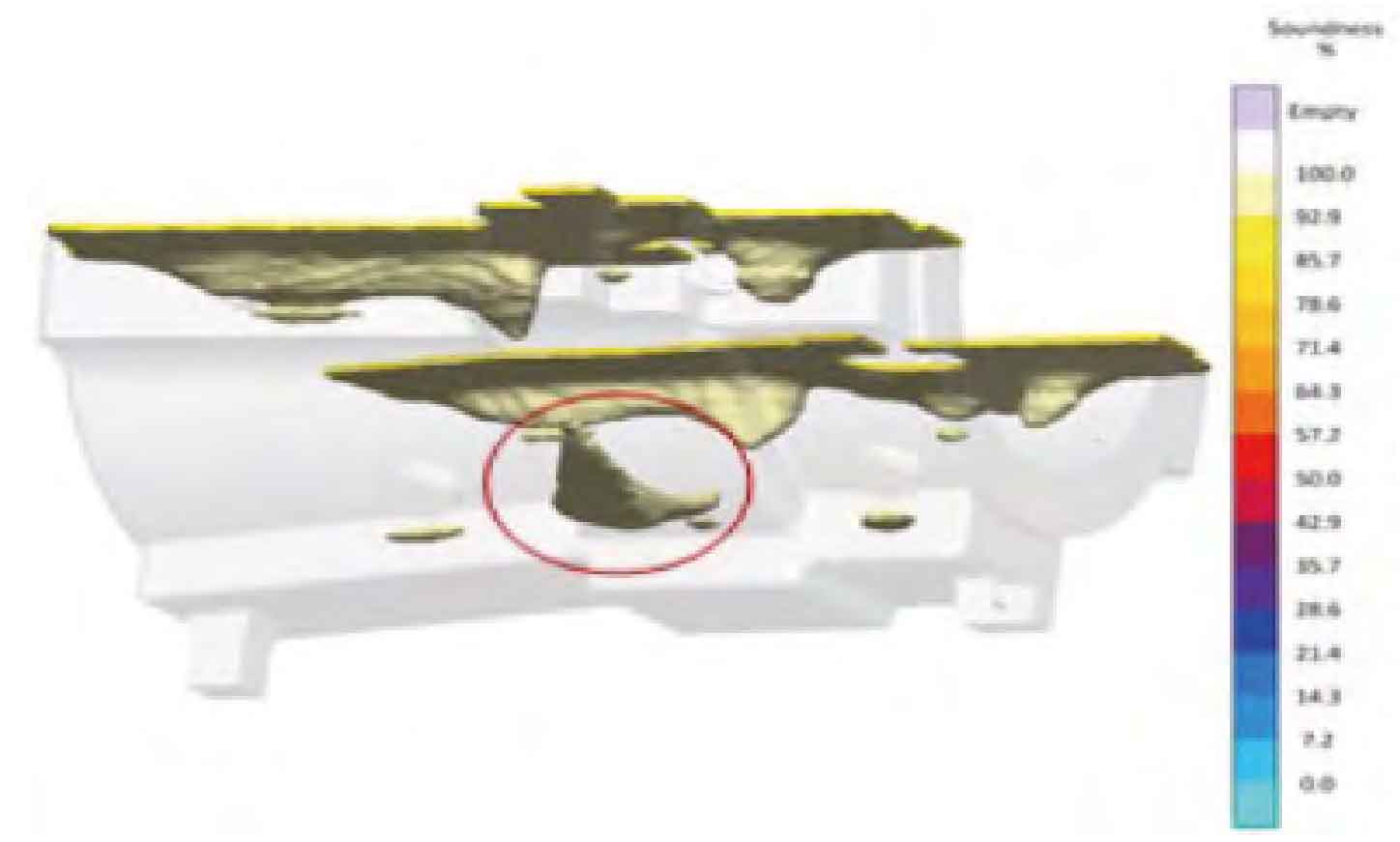
Solution: Open risers are provided at the split flange, and thermal insulation risers are used for feeding.
(3) There are two L-shaped grooves in the rear half of the inner chamber of the cylinder, with a very small width, and the wall thickness here can reach a maximum of 200 mm, making it extremely easy to adhere to sand.
Solution: Due to the large wall thickness and easy sintering of steel castings, the back pipe orifice and inner cavity L-shaped grooves are all solidly cast.
(4) The wall thickness of the steam inlet chamber of steel castings differs greatly from the thickness of three flanges, which is prone to casting defects such as slag holes, air holes, shrinkage porosity, and cracks. Moreover, the steam inlet chamber is narrow and difficult to handle, seriously affecting the production cycle.
Solution: Adopt the “dichotomy” method to design the bottom pouring system, and set up a slag collecting runner to prevent secondary oxidation slag inclusion defects caused by turbulence and other phenomena during pouring and filling; The flange surface is provided with exhaust holes or slag collecting grooves.