As shown in Figure 1: after the investment casting pouring starts, the liquid fills the main sprue in about t = 2.5s and the transverse sprue and inner gate in about t = 3.1s under the action of gravity to reach the bottom of the part. After that, the liquid is divided into two tributaries for pouring. One is filled along the upper three trunk lines, and the other is filled along the lower bottom plate. They meet at t = 6.0s and T = 7.1S respectively, and merge into one at t = 8.8s to fill the front end of the support. At about 13.0s, the filling is completed, and the whole filling process is relatively stable and complete.
Shrinkage porosity, shrinkage cavity, hot crack, segregation, inclusion and other common casting defects are produced in the solidification process of investment casting. Therefore, mastering the solidification law of castings is of great significance to prevent shrinkage porosity and shrinkage cavity casting defects, improve the mechanical properties of investment castings and improve the microstructure of investment castings. Studying the temperature field change during solidification mainly solves the following problems:
(1) The temperature change trend of each part of the casting during solidification of investment casting is shown in Figure 2;
(2) The location and distribution of shrinkage porosity and shrinkage cavity in investment casting are shown in Figure 3.
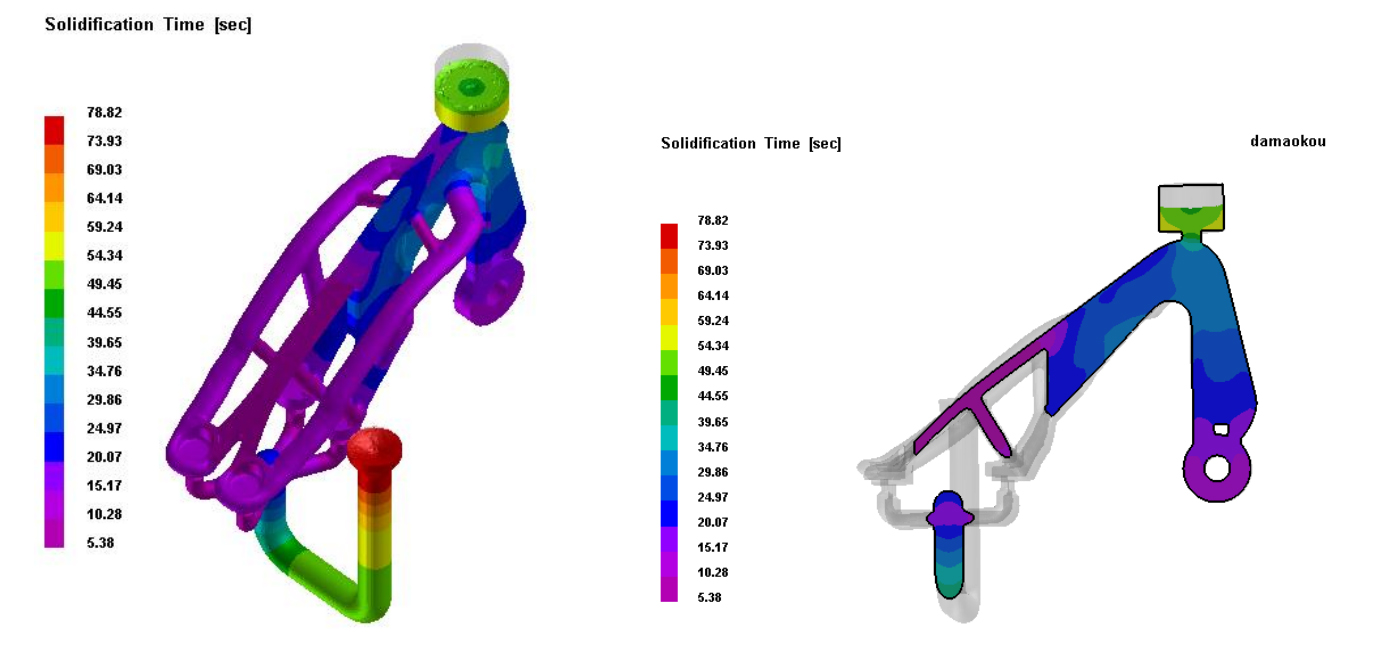
As shown in the above figure, the solidification time of the whole solidification process is 78.82s, which conforms to the principle of sequential solidification. The part far from the riser solidifies first, and the part connected between the three main stems and the lower main board solidifies earlier, which is prone to shrinkage. As shown in Figure 3, the location and size of shrinkage cavity that may occur in the casting are shown. According to ProCAST statistics, the shrinkage cavity and shrinkage casting defects generated by the casting account for 0.7% of the volume of the whole casting.