According to the L9 (3 ^ 4) orthogonal experiment, the results of the orthogonal experiment are shown in Table 1. Perform mean and range analysis on the experimental results, and determine the optimal combination of process parameters through discussion of various quality evaluation indicators.
Number | A | B | C | D | Porosity (%) | Porosity S/N | SDAS/ μm | SDAS S/N | Setting time/s | Setting time S/N |
1 | 1 | 1 | 1 | 1 | 10.040 | -20.003 | 58.210 | -35.300 | 367.1 | -51.3 |
2 | 1 | 2 | 2 | 2 | 1.907 | -5.607 | 59.190 | -35.445 | 390.0 | -51.8 |
3 | 1 | 3 | 3 | 3 | 0.833 | 1.587 | 60.440 | -35.626 | 419.3 | -52.5 |
4 | 2 | 1 | 2 | 3 | 2.199 | -6.523 | 59.060 | -35.426 | 409.3 | -52.2 |
5 | 2 | 2 | 3 | 1 | 1.139 | 1.130 | 60.900 | -35.692 | 433.1 | -52.7 |
6 | 2 | 3 | 1 | 2 | 1.977 | -6.008 | 60.320 | -35.609 | 425.4 | -52.6 |
7 | 3 | 1 | 3 | 2 | 0.872 | 1.190 | 61.200 | -35.735 | 455.1 | -53.2 |
8 | 3 | 2 | 1 | 3 | 2.233 | -6.978 | 60.580 | -35.647 | 446.1 | -53.0 |
9 | 3 | 3 | 2 | 1 | 1.301 | -2.286 | 61.400 | -35.904 | 473.9 | -53.5 |
(1) Porosity
Through the analysis of Table 2, it can be seen that for porosity, the weights of the influencing factors from high to low are the preheating temperature of the lower mold (C), the preheating temperature of the upper mold (B), the pouring temperature (A), and the filling time (D). The lower mold is in contact with the spokes of the low-pressure casting of the wheel hub, and the temperature change of the lower mold will affect the solidification rate of the spokes of the wheel hub, thereby affecting the feeding of areas such as the wheel rim. It can also be seen from the Main effect diagram of the response of the influencing factors that the porosity signal noise ratio value increases with the increase of mold temperature and pouring temperature, indicating that the increase of temperature can increase the fluidity of liquid metal in the mold and enhance the feeding ability. As the filling time increases, the signal-to-noise ratio of porosity shows a trend of first increasing and then decreasing, but its overall impact on porosity has the smallest weight.
Porosity A | Porosity B | Porosity C | Porosity D | SDAS A | SDAS B | SDAS C | SDAS D | Setting time A | Setting time B | Setting time C | Setting time D | |
K1 | -8.008 | -8.445 | -10.996 | -7.053 | -35.457 | -35.487 | -35.529 | -35.632 | -51.9 | -52.2 | -52.3 | -52.5 |
K2 | -3.799 | -3.818 | -4.805 | -3.475 | -35.576 | -35.595 | -35.592 | -35.60 | -52.5 | -52.5 | -52.5 | -52.5 |
K3 | -2.691 | -2.236 | 1.303 | -3.971 | -35.762 | -35.704 | -35.684 | -35.566 | -53.2 | -52.8 | -52.8 | -52.6 |
Range R | 5.317 | 6.209 | 12.299 | 3.578 | 0.305 | 0.217 | 0.165 | 0.066 | 1.30 | 0.6 | 0.5 | 0.1 |
Order | 3 | 2 | 1 | 4 | 1 | 2 | 3 | 4 | 1 | 2 | 3 | 4 |
Optimal solution | A3 | B3 | C3 | D2 | A1 | B1 | C1 | D3 | A1 | B1 | C1 | D1 |
(2) Secondary dendrite arm spacing (SDAS)
For SDAS, the influence weights from high to low are pouring temperature (A), upper mold preheating temperature (B), lower mold preheating temperature (C), and filling time (D). The signal-to-noise ratio of the secondary dendrite arm spacing is mainly affected by the pouring temperature, and decreases with the increase of pouring temperature and mold preheating temperature, which is exactly opposite to the porosity. Although increasing temperature can improve the feeding capacity, it can cause coarse grain structure of the molten metal during solidification, resulting in a decrease in mechanical properties. As the filling time increases, the signal-to-noise ratio of SDAS values gradually increases, indicating that a smooth filling process can improve the mechanical properties of low-pressure castings.
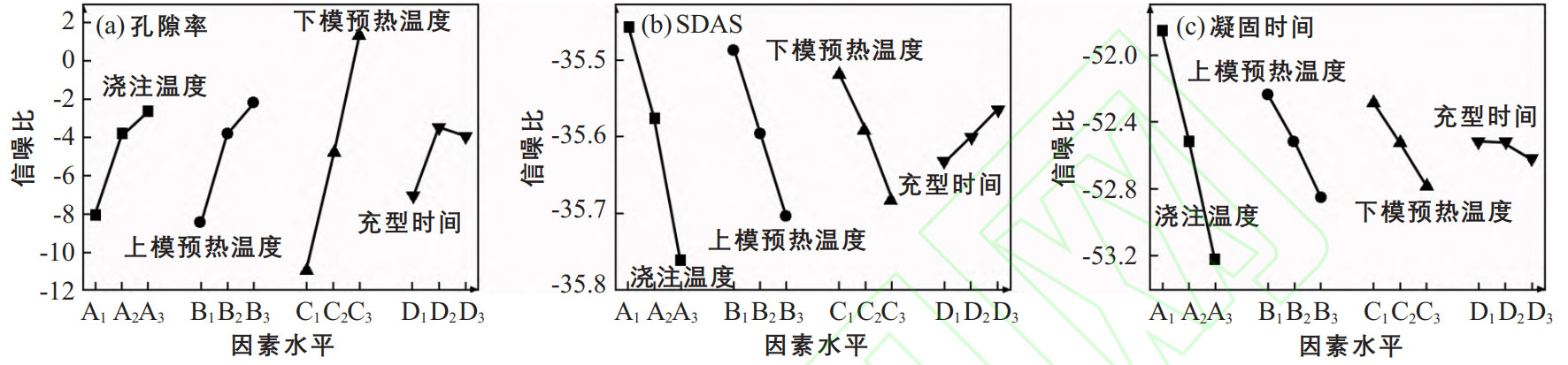
(3) Setting time
For solidification time, the influence weights from high to low are pouring temperature (A), upper mold preheating temperature (B), lower mold preheating temperature (C), and filling time (D). The lower the pouring temperature and mold preheating temperature, the faster the solidification process of low-pressure castings, improving production efficiency, and reducing single piece costs. Lowering the pouring temperature and preheating temperature of the mold can significantly reduce the solidification time, but it can cause undercooling during the filling and solidification process, slow down the fluidity of the aluminum liquid in the cavity, and affect the quality of the filling and casting. The effect of filling time on solidification time is relatively small.
In summary, the parameter combination for obtaining the optimal porosity is the pouring temperature of 710 ℃, the preheating temperature of the upper mold of 280 ℃, the preheating temperature of the lower mold of 340 ℃, and the filling time of 25 seconds, namely A3B3C3D2 (Scheme 1); Obtain the optimal combination of secondary dendrite arm spacing parameters, which is the pouring temperature of 650 ℃, the preheating temperature of the upper mold of 200 ℃, the preheating temperature of the lower mold of 260 ℃, and the filling time of 20 seconds, namely A1B1C1D1 (Scheme 2). For the production of low-pressure casting wheel hubs, it is necessary to improve production efficiency while ensuring the quality and mechanical properties of the castings. Therefore, after referring to the influence weights of various factors on the evaluation indicators, the optimal parameter combination was selected: pouring temperature 650 ℃, upper mold preheating temperature 280 ℃, lower mold preheating temperature 340 ℃, and filling time 20 seconds, namely A1B3C3D1 (Scheme 3).