(1) During the mold filling process, the steering knuckle steel casting process uses sand gravity casting. Through the analysis of the mold filling simulation results, it can be seen that the product has a high pouring temperature and a short mold filling time. When the casting cavity is fully filled with liquid steel, the temperature of the steering knuckle steel casting is still above the liquidus, without insufficient pouring. Figure 1 shows the filling process of liquid steel. As can be seen from Figure 1 (a), at the beginning of pouring, molten steel smoothly enters the pouring system from the gate tube. As can be seen from Figure 1 (b), when molten steel enters the casting cavity from the inner runner, it directly washes out the intermediate molding sand platform, and then the molten steel fills the mold downward along the casting cavity wall. As shown in Figure 1 (c~d), the molten steel finally fills the casting cavity from bottom to top.
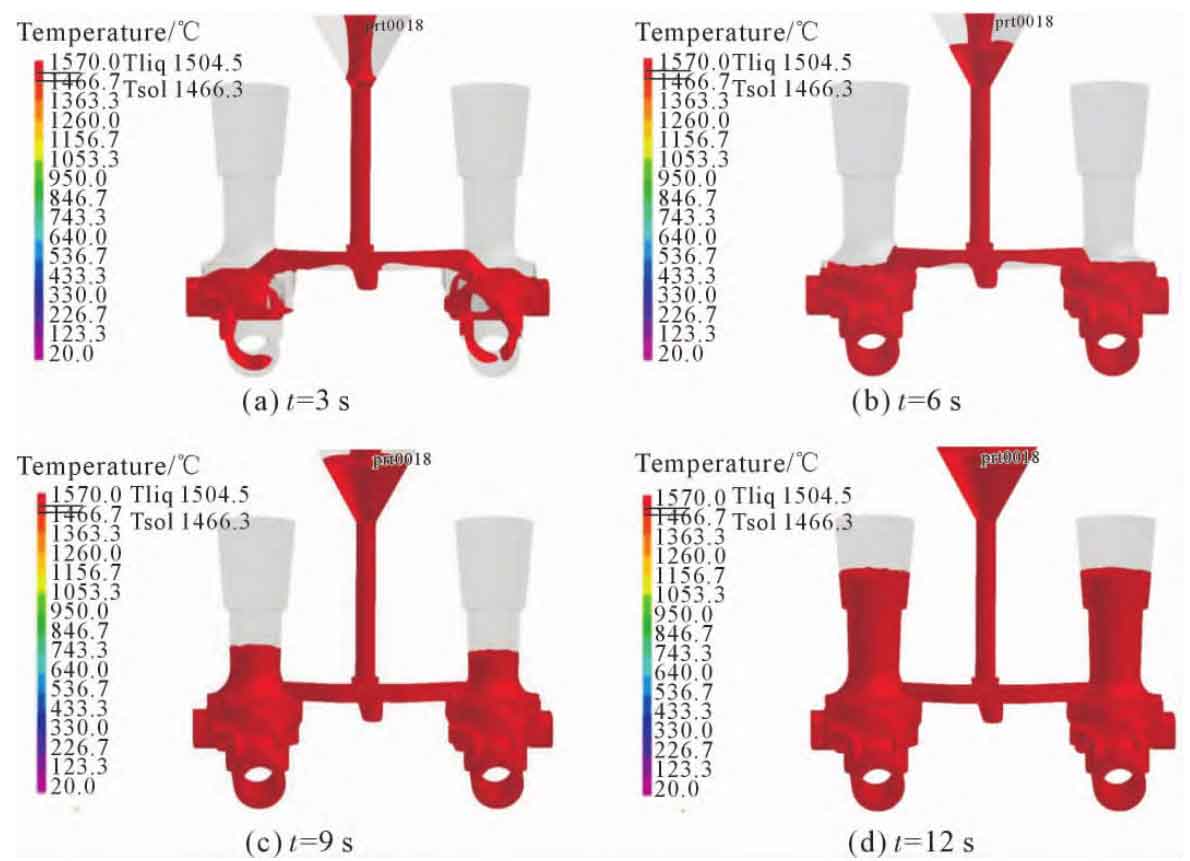
(2) During the solidification process, when the solid content of the steering knuckle steel casting reaches 61.6%, the liquid steel disappears in the animation. The overall solidification process of the steering knuckle steel casting presents a sequence of solidification from bottom to top, with the edge area around the riser first solidified, and the riser part finally solidified. From the temperature field, it can be seen that during solidification and cooling of the steering knuckle steel casting, there is an isolated liquid phase zone at the thick part of the axial center, which is prone to produce shrinkage defects at the later stage of solidification, as shown in Figure 2.
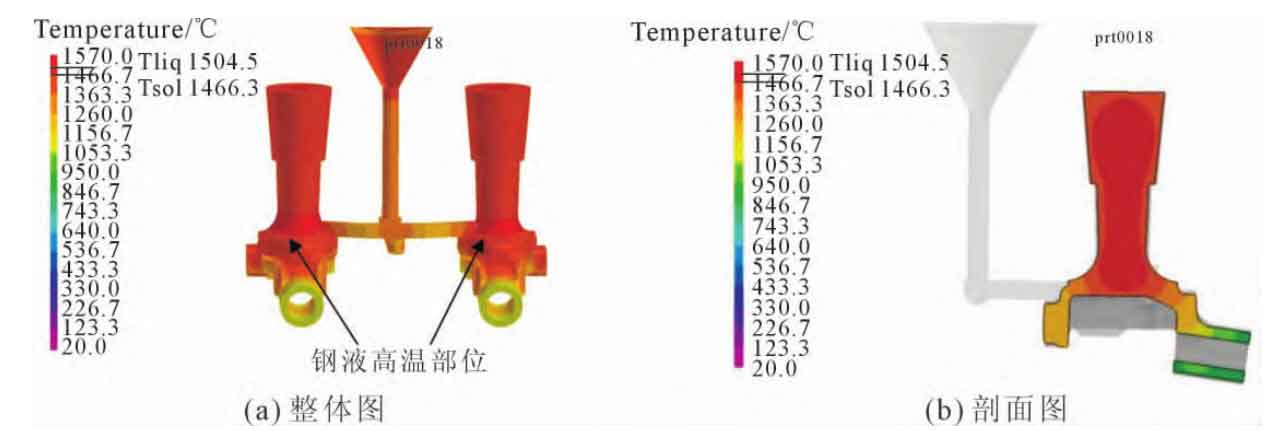
From the overall distribution diagram of shrinkage holes in the steel casting of the steering knuckle during the later solidification period, it can be seen that there is a high probability of shrinkage defects in the thick parts of the axial center. If sufficient liquid steel is not supplemented above the shrinkage defects in the axial center during the final solidification, the physical object will form shrinkage defects, as shown in Figure 3.
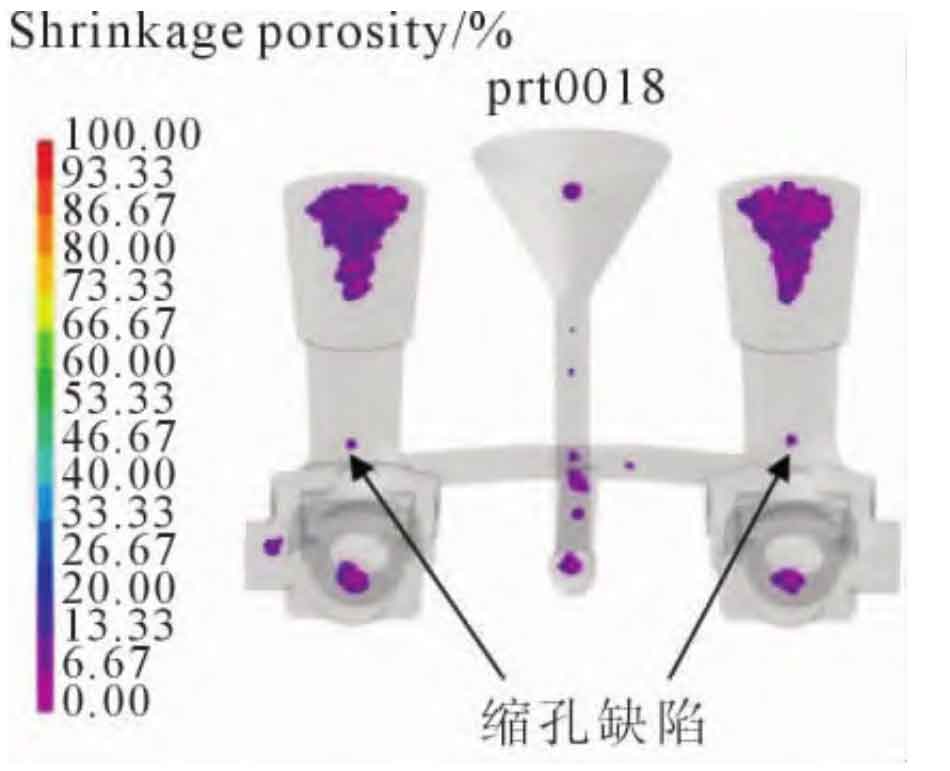