The distribution of the solid-liquid phase of the initial centrifugal casting process at t=150s is shown in Figure 1. The liquid metal transfers heat to the surroundings through thermal radiation. The liquid metal near the mold and baffle solidifies first because of the rapid cooling. As the internal surface of the centrifugal casting cylinder liner and the two-way heat dissipation of the mold, the internal surface and the external surface of the centrifugal casting cylinder liner solid-liquid solidify first because of the lower temperature. The middle layer of the centrifugal casting cylinder liner wall thickness has a higher temperature and a slower solidification rate, Finally solidify.
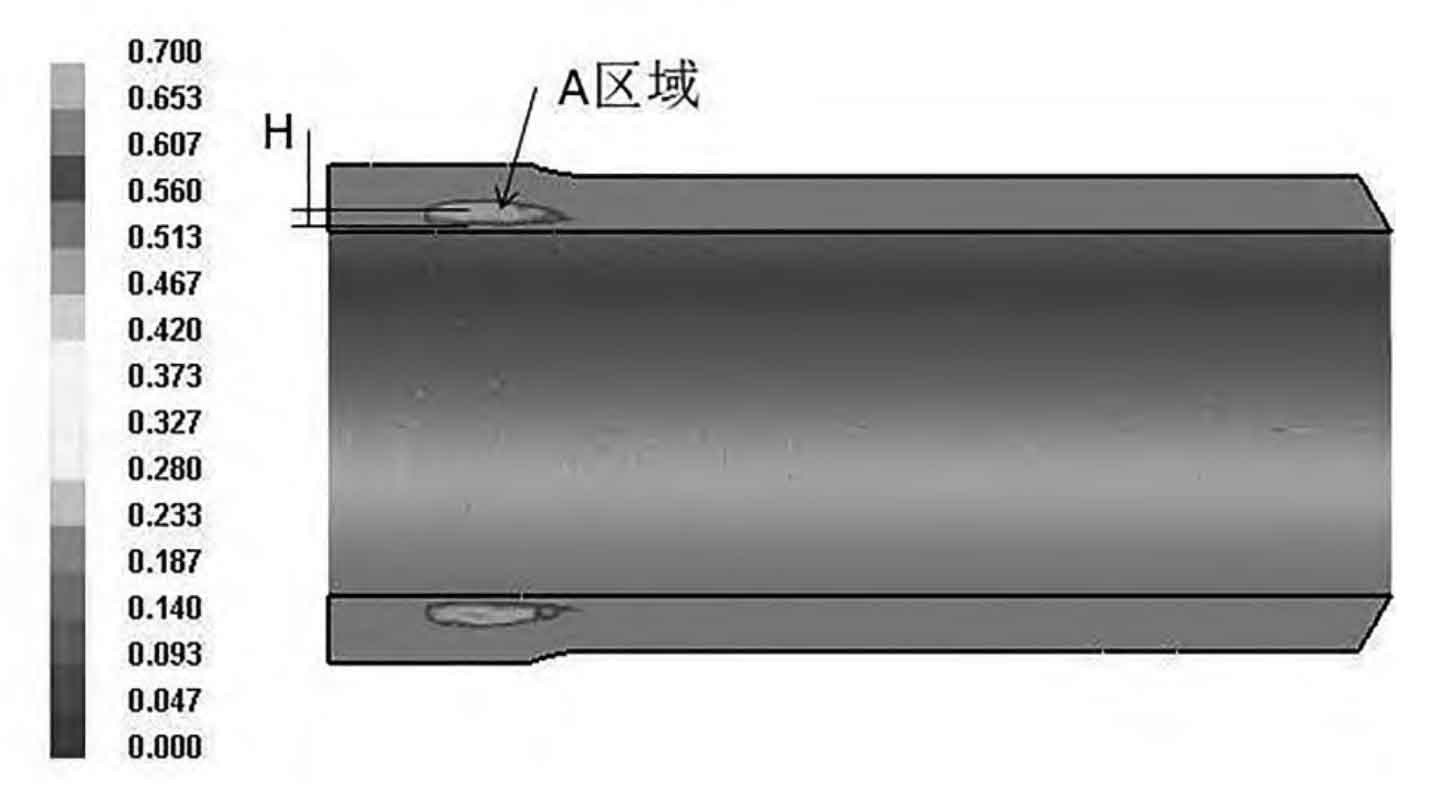
The “Area A” in Figure 1 is the final solidification area, which is also the location where anti white mouth defects are easily produced. The distance H=7.8mm from the center of the final solidification area to the inner wall of the center casting cylinder liner is measured.
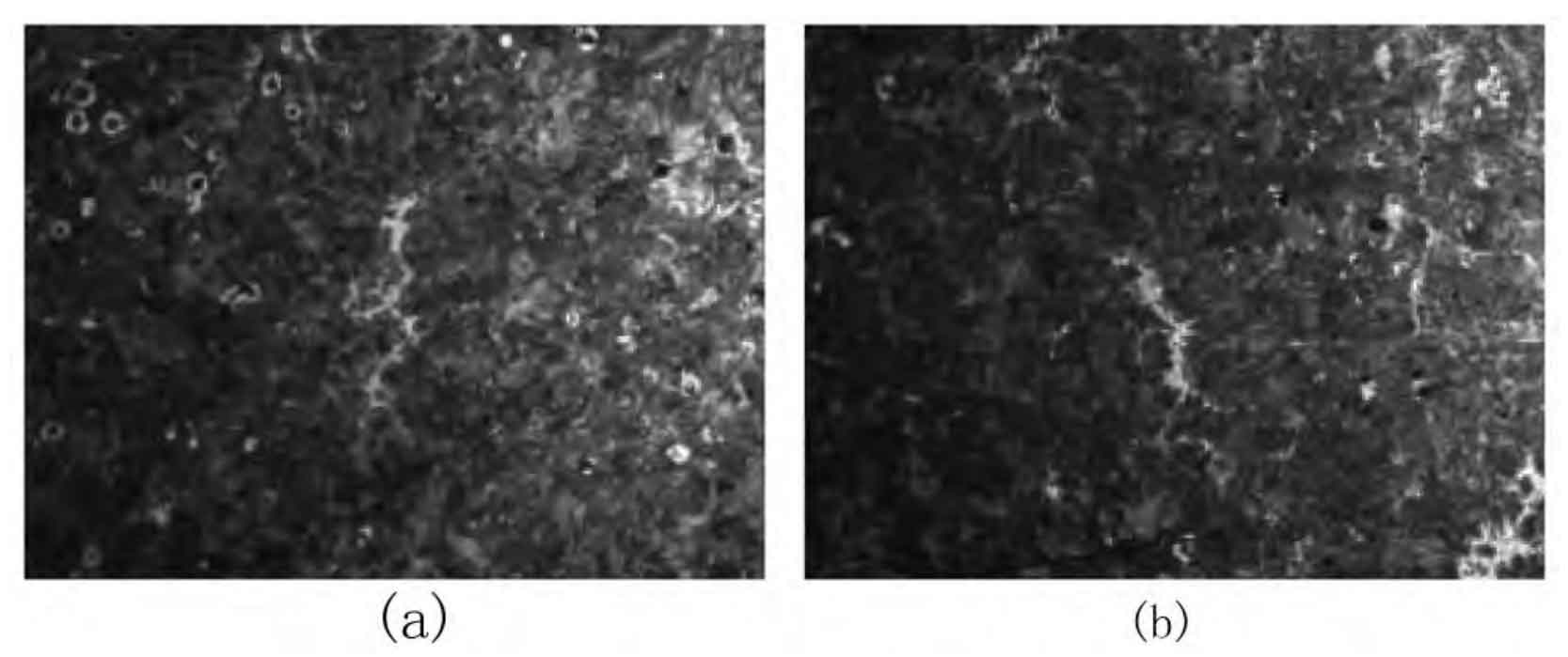
According to the 100 times metallographic photos of the anti white mouth defect in the actual production process of the initial process, as shown in Figure 2, the defect location is about 7mm away from the inner wall of the center casting cylinder liner, and the casting defect location and the final solidification area are almost at the same location. Therefore, it is proved that the location of the casting defect can be predicted using the simulation results of the solid-liquid distribution, providing a basis for process optimization.