The solidification process of liquid metal is divided into three phases: liquid phase, solid / liquid phase coexistence and solid phase. The thermal and mechanical properties of the material change greatly, and there may be three regions coexisting at the same time. Therefore, the stress-strain constitutive relationship of solidification simulation design is very complex. If the maximum stress of liquid metal in the process of phase transformation is greater than the tensile strength of the material, cracks will occur. Hot cracking is a common defect in the casting process, which is an important factor affecting the quality and performance of castings. Therefore, reasonable casting process design plays an important role in reducing casting stress and preventing hot cracking.
1.The effect of pouring speed on effective stress
The initial temperature of sand mold is 25 ℃ (room temperature) and pouring temperature is 1610 ℃. The effective stress distribution of castings with pouring speed of 14kg / s and 12kg / S is calculated respectively, as shown in Figure 1.
It can be seen that when the pouring speed is 14kg / s and 12kg / s, the maximum effective stress of the casting is 40.11 MPa and 40.15mpa respectively. It can be seen that the effect of pouring speed on the maximum effective stress of the casting is not obvious.
2. Effect of pouring temperature on effective stress
The initial temperature of sand mold is 25 ℃ (room temperature) and the pouring speed is 14kg / s. The effective stress distribution of casting at 1610 ℃ and 1650 ℃ is calculated respectively, as shown in Figure 2.
During the cooling process, the different cooling rate of each part results in the different shrinkage of each part at the same time. At the same time, due to the different heat dissipation and cooling conditions, the time for each part to reach the solid phase transformation temperature is also different, and the degree of phase transformation is also different. In the case of free expansion, the elongation in the direction of length and width is Δ l= α( TP TS) l and Δ d= α( The strain in the direction of length and width is: TP TS) d
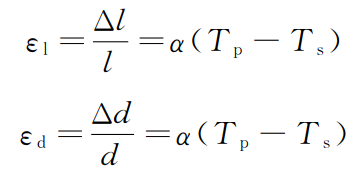
When the casting temperature decreases from pouring temperature (TP) to solidus temperature (TS), the strain in each direction is as follows:
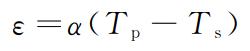
Where, α Is the coefficient of linear expansion of the material, which varies with temperature.
When the pouring temperature increases from 1610 ℃ to 1650 ℃, the strain in all directions increases by 7.5% ~ 7.75%, and the cooling time of the casting is prolonged. In the process of shrinkage, the blocking time of sand mold, gating system and riser increases correspondingly, and the casting stress increases accordingly. It can be seen that when the pouring temperature is 1610 ℃ and 1650 ℃, the maximum effective stress of the casting is 40.11 MPa and 43.21 MPa respectively. Therefore, the maximum effective stress of the casting is greatly affected by the pouring temperature.