The structure of the steering knuckle steel casting is irregular, with a complex thin-walled structure below the parting surface, while the axial dimension above the parting surface is thick and bulky, which conforms to the overall sequential solidification principle. As shown in the figure, the wall thickness dimensions of the two support platforms below the parting surface are relatively large. When pouring molten steel, the thin wall above the support platform solidifies quickly, forming an independent space, and easily causing casting defects such as shrinkage holes at hot spots. The axial shape above the parting surface is irregular and the neck position is in a necked shape, causing the neck to solidify first after pouring, and the upper steel liquid cannot be filled in time. The steel liquid below the neck solidifies and contracts to form a closed body, causing hot spots and casting defects such as shrinkage holes.
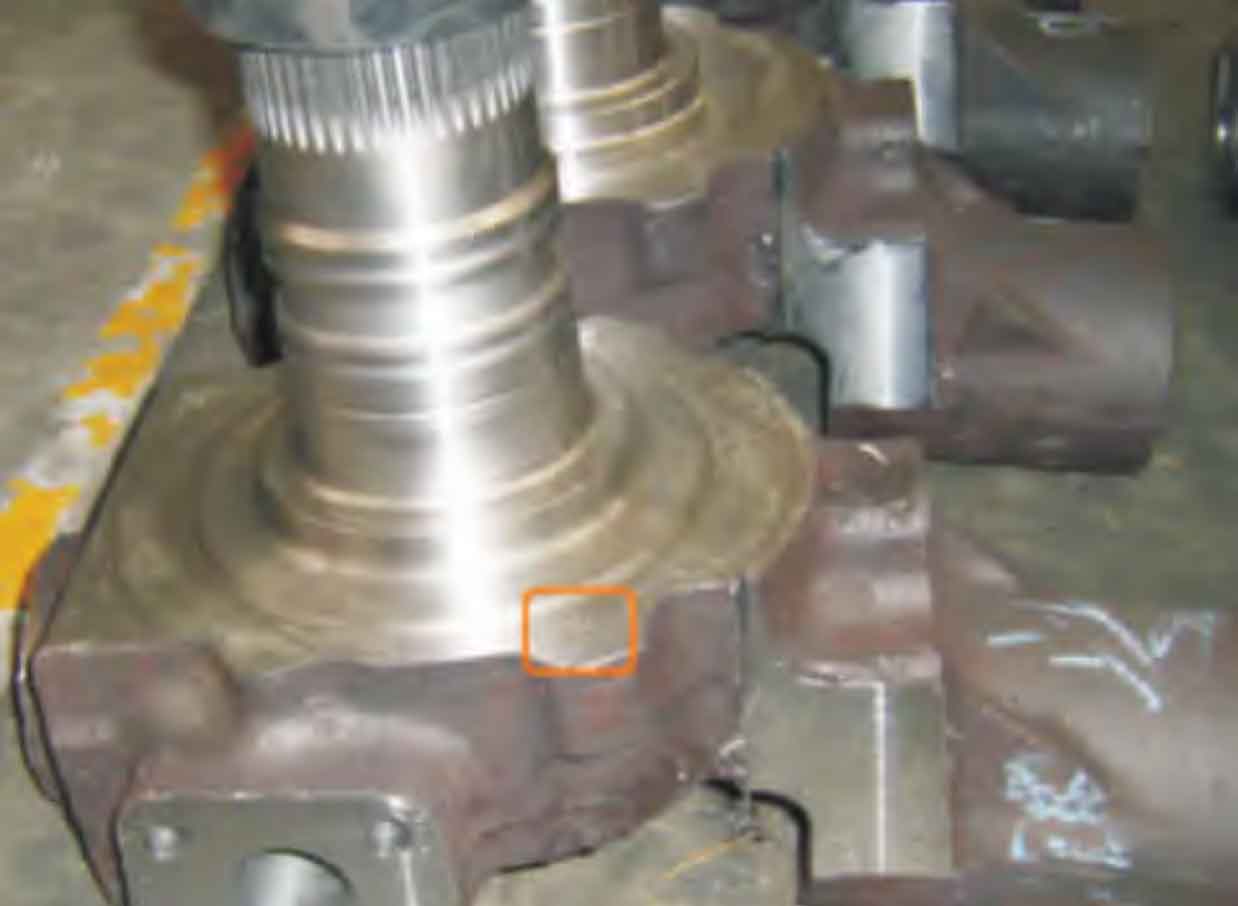
In addition, in the process design of steering knuckle steel castings, the inner runner enters the sand mold cavity at a certain angle from the middle, and the entrance direction of the inner runner corresponds to the position of the boss, which can easily flush the floating sand in the mold cavity to the dead corner of the boss. Due to the limitations of the axial neck structure, it is not conducive to further floating the floating sand into the riser, resulting in casting defects such as sand inclusion. Therefore, main defects of the steering knuckle steel castings are shrinkage cavities, sand inclusions, and other casting defects.