(1) Cause analysis of formation of porosity in invasive casting. The total amount and rate of gas produced by molding sand at high temperature is called gas generation. Theoretically, as long as the following conditions are controlled: P gas < p liquid + P resistance + P cavity, the castings will not produce invasive casting pores. However, various pressures in the above conditions change from the time when the liquid metal is poured into the mold. Liquid P increases with the increase of pouring amount of liquid metal, and reaches the maximum when it is full. P gas also increases with the increase of pouring time and gas production, but p gas value is not only related to the total gas production of sand mold gas production materials, but also related to gas production temperature and gas production speed. Therefore, the occurrence time and value of the maximum value of P gas are different, and the consequences are different accordingly.
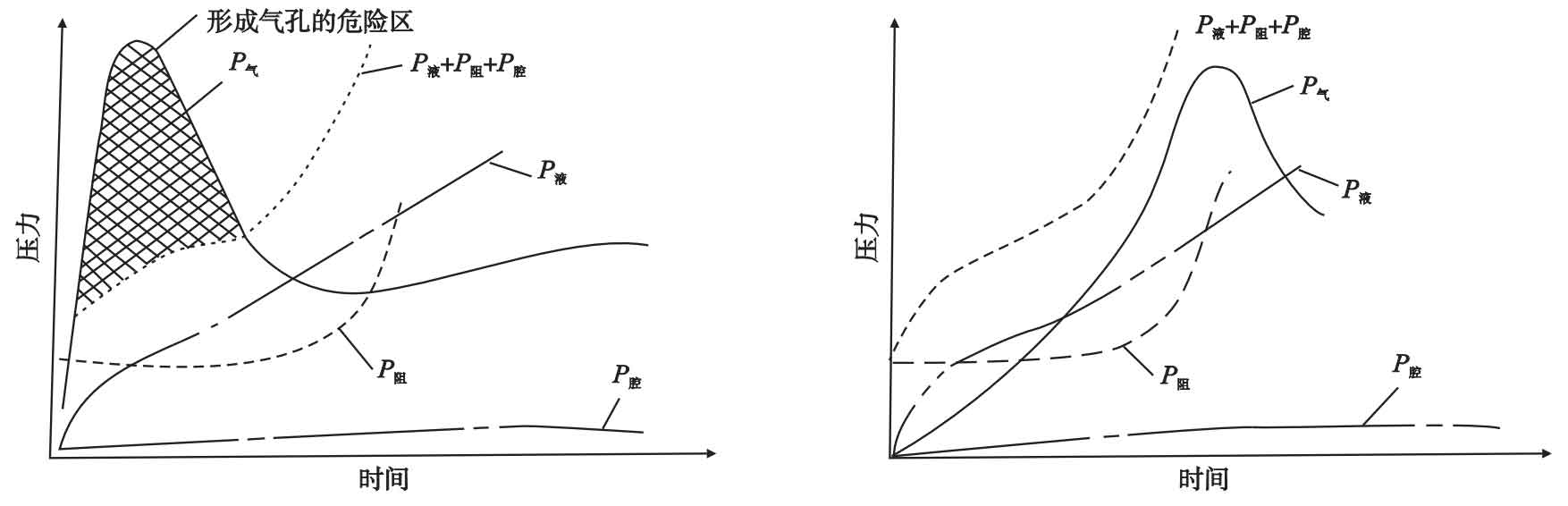
Fig. shows the effect of molding sand gas evolution and gas evolution rate on the formation of invasive casting pores. Fig. a shows the situation when the molding sand has a high gas generation rate. Fig. b shows the situation when the gas generation speed is slow. It can be seen from Fig. a that there is a dangerous area of invasive casting pores, in which p gas > P liquid + P resistance + P cavity. In Fig. b, P gas < p liquid + P resistance + P cavity during the whole process from pouring to solidification and crusting on the casting surface, so invasive casting pores will not be formed.
The molding sand used for valve body modeling is alkaline phenolic resin sand. The main gas generation temperature of phenolic resin is 650 ~ 750 ℃, and the total gas generation is 460 ml / g. Compared with urea acid resin (the main gas evolution temperature is 280 ~ 320 ℃, and the gas evolution is 410 ml / g), the gas evolution temperature range is large. When other conditions are the same, phenolic resin is more dangerous to cause casting pores.
The selection of phenolic resin sand is harmful to the formation of casting pores, especially when the moisture content in the air increases. When water turns into steam at 100 ℃, the volume expands suddenly, and the expansion becomes more serious when it is further heated, which promotes the rapid increase of P gas, which is very harmful. The water content in the air in July, August and September is more than 20 g / m3. Therefore, the humidity in the air is very high, and a large amount of water will be brought into the sand mixing molding process, smelting process and pouring process. When the temperature rises sharply, P gas will increase rapidly, and the risk of forming casting pores will also increase greatly.
(2) Cause analysis of porosity formation in reactive casting. There are two reasons for the formation of porosity in reactive casting of valve body castings.
1) The content of soluble gas in furnace gas is too high, and liquid metal absorbs a large amount of gas. Under the condition of electric arc furnace melting, the water in the air is dissociated into hydrogen and oxygen due to the high temperature of the arc. In Meiyu season, the moisture content in the air is too high. During refining, the calcium carbide in carbide slag will produce the following chemical reaction with the moisture in the air to produce a large amount of hydrogen:
2) In the smelting process, after adding slag remover at last, the slag is not removed in time. During the slag removal process of molten steel, the heating power supply has been cut off, but the slag has not been removed in time. With the decrease of temperature, the slag sinks into the liquid metal and floats to the top layer during pouring. In addition, under the influence of reactive gas, a casting pore containing a large amount of slag is formed.