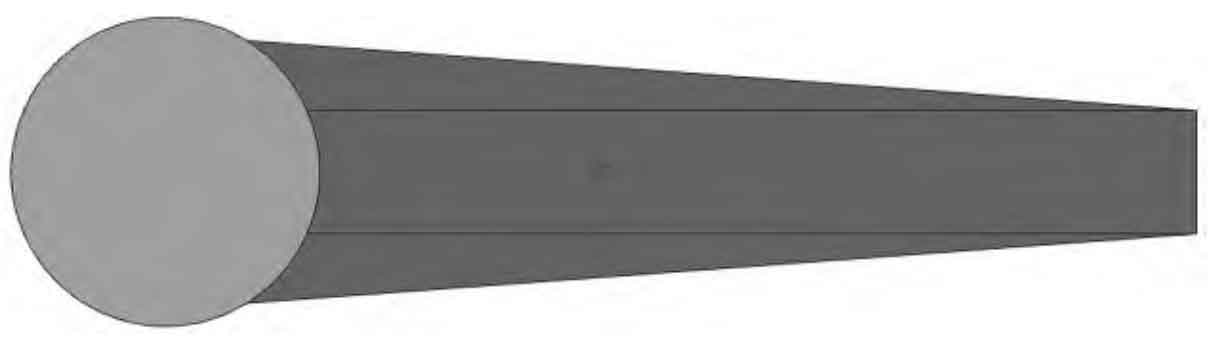
Metal subsidy is one of the most common subsidies. Metal subsidy refers to the structure subsidized on the basis of the casting, which is integrated with the casting to establish a feeding channel for the casting, so as to effectively realize sequential solidification. Because the metal subsidies change the original structure, it is usually necessary to propose design changes or process cleaning to the customer. Take the simple model as an example. Through analysis, the metal subsidies are added on both sides to reduce the size of the castings from the riser end to the distal end, as shown in Fig. 1.
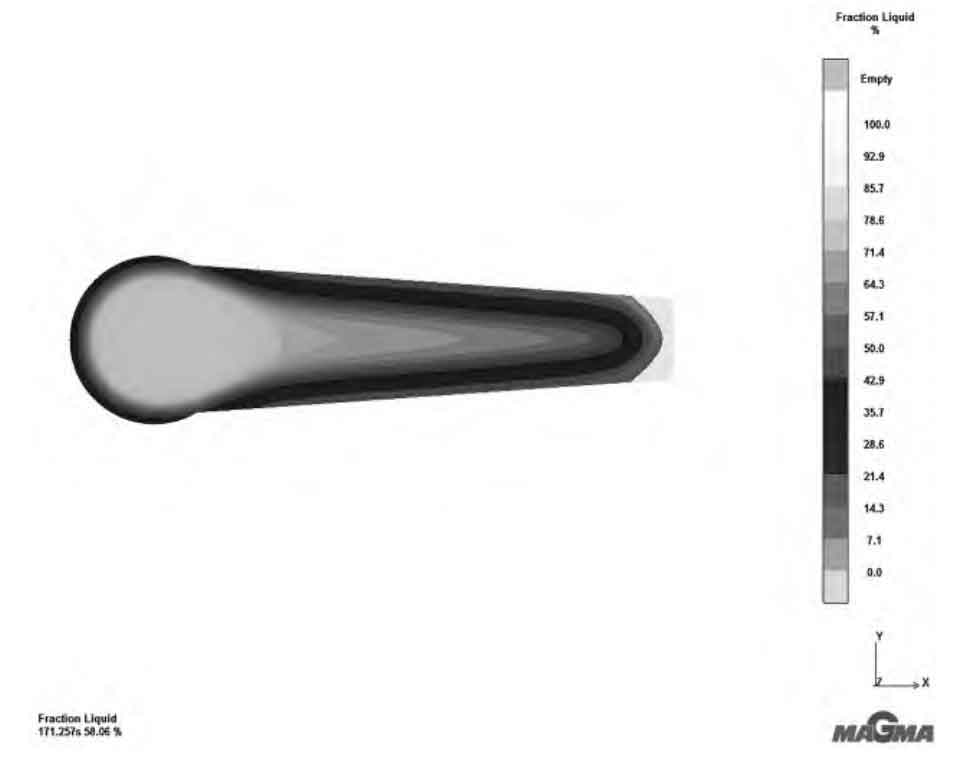
Through the analysis of the solidification process simulated by magma, it is found that after the increase of metal subsidies, the feeding of castings will form sequential solidification, no independent liquid phase zone will be formed, and the castings will not have shrinkage porosity risk, as shown in Fig. 2.
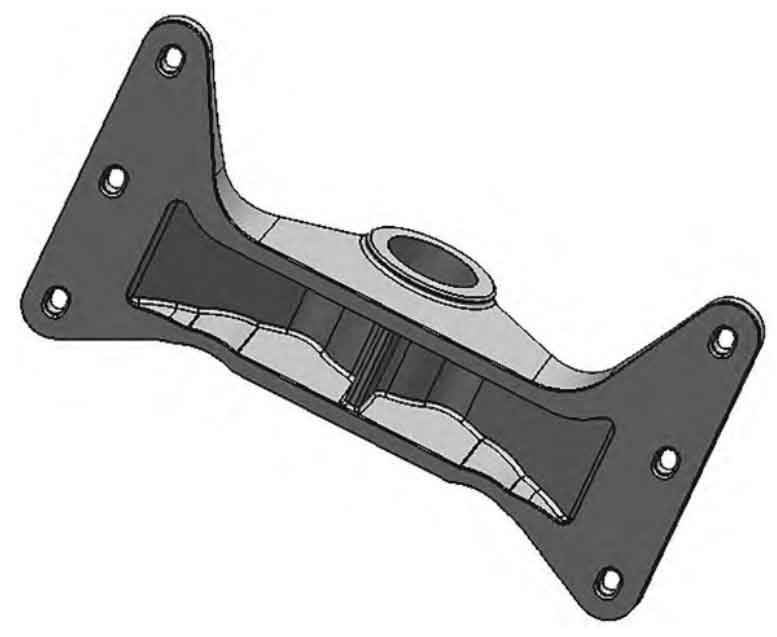
Take the support seat product shown in Fig. 3 as an example. The casting material is qt400-18. As the casting needs to randomly take mechanical performance test bars at the identification positions ① and ②, as shown in Fig. 4, if there is shrinkage in the middle area of the test bar, the mechanical performance will be unqualified. Therefore, it is necessary to ensure that the identification area is completely free of shrinkage.
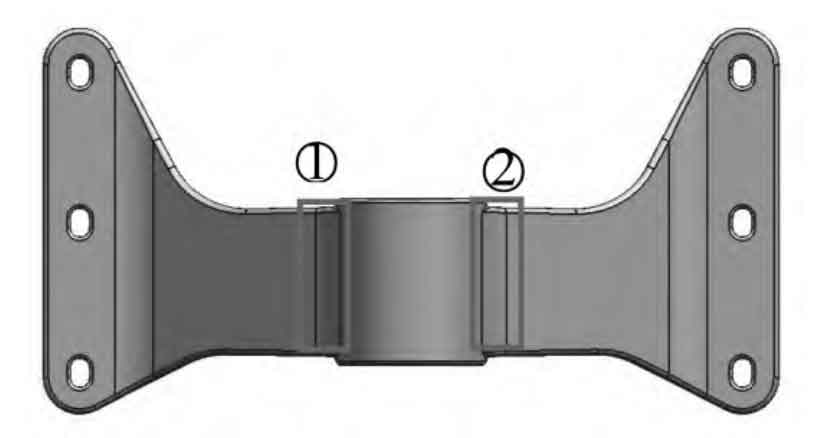
According to the analysis, the product is produced and developed on disa line. The riser is placed as shown in Fig. 5. The riser is placed on the top of the test bar. Through the simulation analysis of magma, the feeding channel of the casting solidifies early, and shrinkage porosity defects will appear inside the casting. Through the trial pouring of the original process, the internal defects of the casting correspond to the simulation results and need to be improved. See Fig. 6.
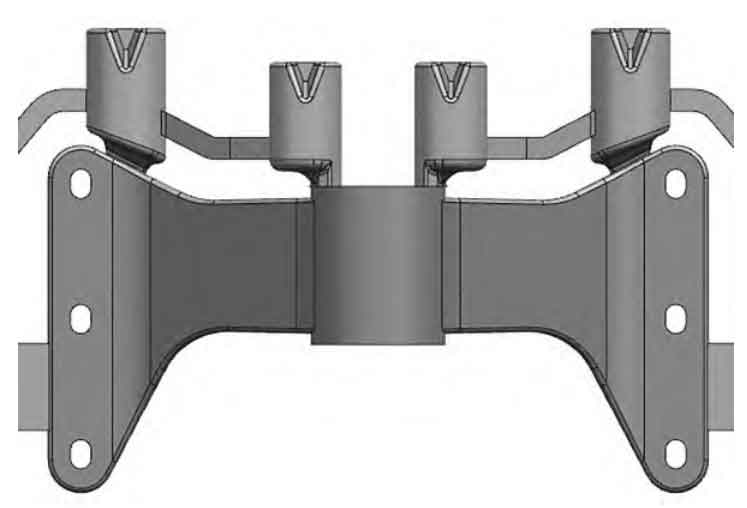
If the metal subsidy scheme is used for optimization, as shown in Fig. 7, the metal subsidy is increased, and through simulation analysis, the test bar area of the casting is fully fed, without shrinkage porosity risk.
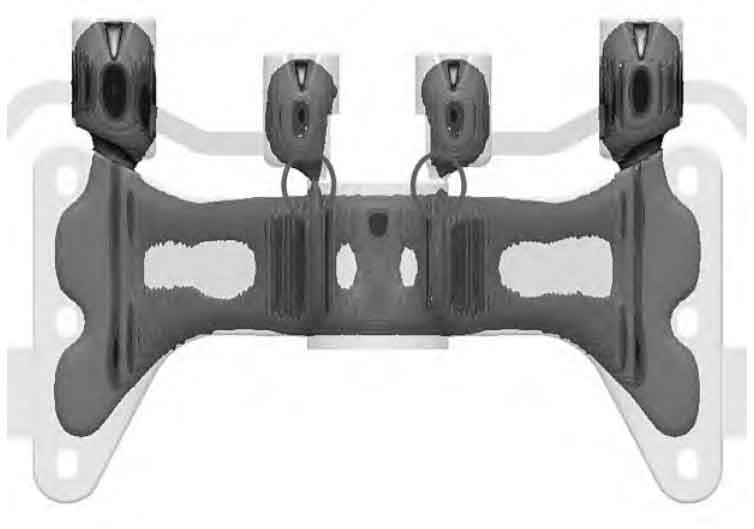
Through the above simple model and example analysis, it can be seen that metal subsidy is relatively simple to operate, can be directly formed by molds, and the process is easy to solidify, which is the most commonly used subsidy scheme. Of course, there are also disadvantages: design changes need to be proposed to customers, and the material cost will increase. If the product structure cannot be changed due to function or interference, then it is necessary to clean the casting Removal during processing: for some irregular areas, it is difficult and costly to clean.
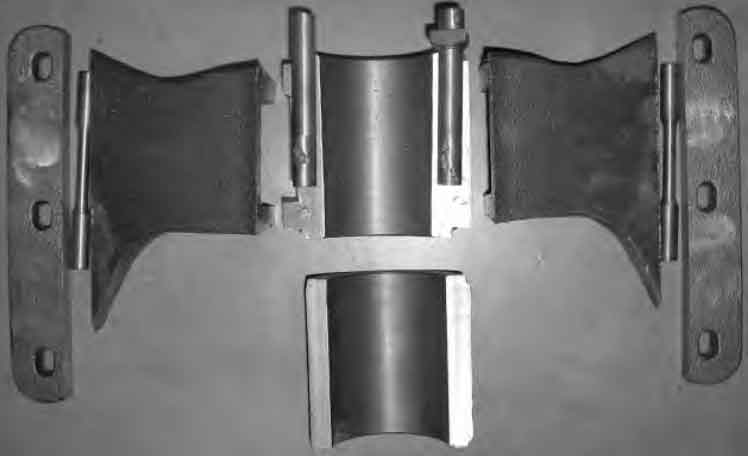
This case is a relatively simple model. The actual product structure may be very different, and the method of increasing metal subsidies may also need to be explored and summarized.
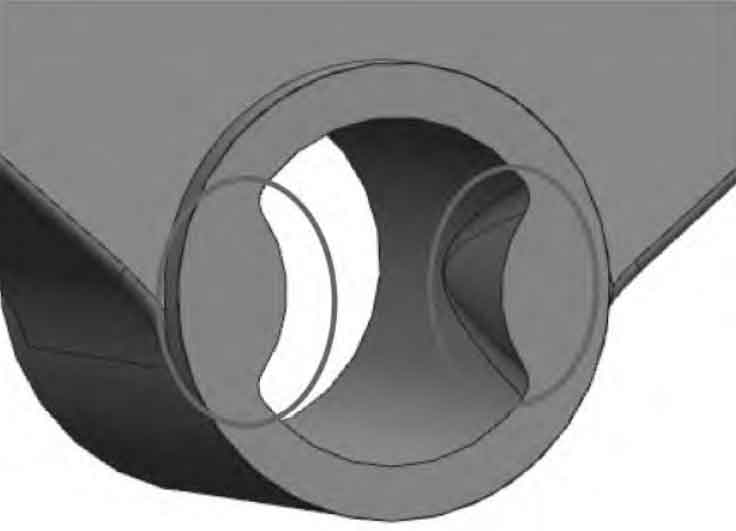