Nd is generally used to refine the grain and improve the mechanical properties of the cast magnesium alloy, and to improve the heat resistance of the magnesium alloy so that the magnesium alloy can be used at high temperature.
1. Application of Neodymium in ZM5 cast magnesium alloy
X-ray diffraction and metallography show that the as cast structure of ZM5 Alloy is composed of α – Mg solid solution and β – Mg17Al12 network distributed along the grain boundary. After solution treatment, Mg17Al12 is dispersed in the matrix, while ZM5 Alloy with rare earth element nd is composed of α (matrix), Mg17Al12, granular mg12nd and other phases. After solid solution treatment, the mesh Mg17Al12 phase was completely dissolved, leaving the precipitated phase Mg12Nd with high thermal stability. SEM shows that the fracture of ZM5 Alloy is cleavage fracture, while the fracture of ZM5 Alloy with rare earth Nd is intergranular fracture and quasi cleavage fracture. The reason is that when rare earth Nd is added, mg12nd, a strengthening phase, which is coherent with magnesium matrix, is formed in the melt, and the fracture morphology is changed.
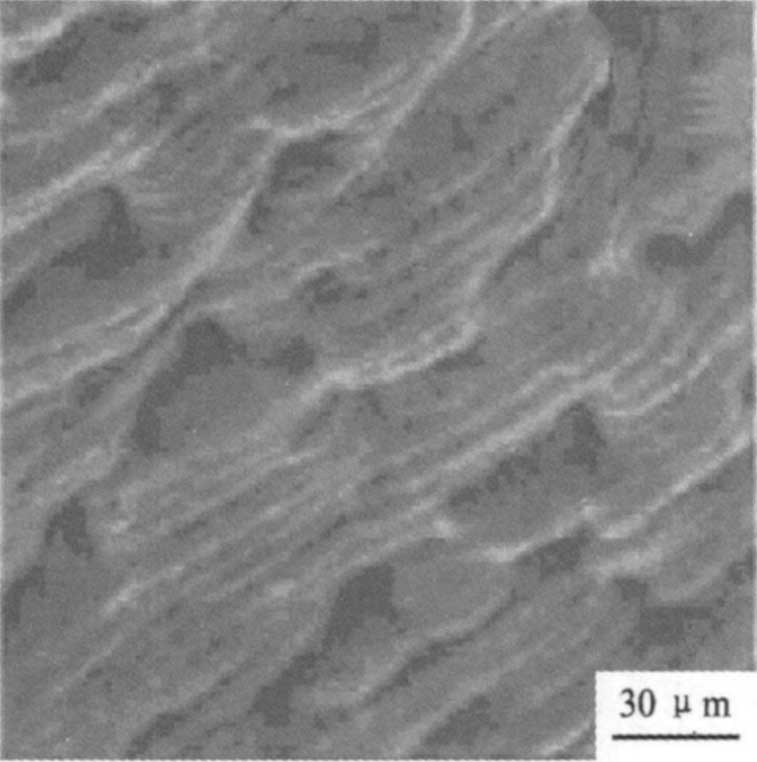
The microstructure of ZM5 cast magnesium alloy is usually composed of matrix solid solution α – Mg phase and network eutectic structure β – Mg17Al12 phase distributed around the grain boundary. However, after adding a certain amount of rare earth element Nd (the maximum mass fraction is 2%), the mixed phase mg12nd is formed in the alloy. Adding rare earth nd to ZM5 Alloy can effectively refine the structure of the alloy. When the mass fraction of Nd is 2%, the refining effect of the structure is significant. Adding nd into ZM5 Alloy forms mg12nd strengthening phase, which is superior to Mg17Al12 in strength and thermal stability. It has been verified that the structure of mg12nd and HCP matrix has a good way: local ductile fracture + quasi cleavage fracture. The fracture mode of ZM5 Alloy is cleavage fracture. The reason is that the dispersion distribution of mg12nd is formed by adding mixed rare earth, which changes the fracture morphology of the alloy. Nd phase itself has the characteristics of high melting point, high hardness and high corrosion resistance. In the as cast structure, it is mainly distributed on the grain boundary, but the amount of dissolution in the crystal is very small, because the radius of Nd atom is larger than that of Mg.
2. Application of Neodymium in AZ91 cast magnesium alloy
The influence of Nd on the microstructure and mechanical properties of AZ91 cast magnesium alloy can be seen from the following aspects: (1) because nd can reduce the interfacial tension between solid and liquid: from the formula R * = – 2 σ L-S Δ GM, it can be seen that the critical nucleation radius of Nd containing magnesium alloy is reduced, it is easy to nucleate, and the grain of the alloy is refined; In the formula, R * is the critical nucleation radius, σ L-S is the interfacial tension between solid and liquid, and Δ GM is the free energy difference of the unit volume of solid and liquid; (2) nd promotes the formation of completely divorced eutectic. Because the distribution coefficient of Nd in MG is less than 1, and the solid solubility decreases with the decrease of temperature [7], a nd rich layer is formed at the front of α dendrite solidification, which enhances the component supercooling at the front of α dendrite solidification, makes the primary α dendrite grains smaller and produce more branches, reduces the dendrite spacing, and promotes the occurrence of completely divorced eutectic. (3) Near the eutectic temperature, Al, Nd in the liquid phase formed al11nd 3 intermetallic compound [8], which mainly distributed in the form of granular and acicular near the grain boundary. (4) At the end of the solidification process, some of the nd elements were dissolved in α – Mg, which reduced the diffusion coefficient of the solid solution and made the diffusion of Al in α – Mg relatively difficult, thus inhibiting the formation of secondary β phase.
Add nd element in AZ91 casting magnesium alloy, nd exists in two forms of solid solution and intermetallic compound al11nd3 in AZ91 magnesium alloy, which reduces the geometric size of α and β phases and promotes β phase granulation. At the same time, nd promoted the transformation from the incompletely divorced eutectic to the completely divorced eutectic, and inhibited the secondary β phase precipitation. Nd element can also improve the tensile strength and macro hardness of the alloy through the joint action of solution strengthening, precipitation strengthening and fine grain strengthening, and improve the elongation of the alloy by refining the grains. However, when the content of Nd in the alloy is too high (w (nd) = 1.5%), the strength and elongation of the alloy decrease slightly. The addition of Nd in AZ91 can also change the fracture mechanism from cleavage fracture to quasi cleavage fracture. Adding 0.2% ~ 0.8% nd to AZ91 alloy can refine α grain obviously. The average grain size decreased from 108 μ m before refining to about 31 μ m, and the grain area decreased from 3575 μ M 2 to 920 μ M 2. When the nd content is 0.5%, the grain size is the smallest. Through the measurement and analysis of the grain size and grain area, it can be seen that the rare earth element nd has an obvious refining effect on the α – grain in AZ91 alloy.
3. Refinement and modification mechanism of Neodymium on cast magnesium alloy
The rare earth element nd also has remarkable effect on grain refinement and modification of cast magnesium alloy. At 0.2% nd, the effect of modification is better; at 0.4% nd, the effect of grain refinement is the best for eutectic magnesium alloy, and the effect of grain refinement is worse with the increase of Nd addition. In the solidification process, when the nd content in the front of liquid-solid interface exceeds a certain amount, in addition to eutectic phase, it may also form coarse compound with other elements.