Casting refers to the process of melting solid metal into liquid, pouring it into a specific shape of mold, and then solidifying it into shape.
Metal shrinkage occurs in the following three stages: liquid cooling; Coagulation; Solid cooling. The volume change and pouring temperature cooling change under the shrinkage state are shown in Figure 1 below.
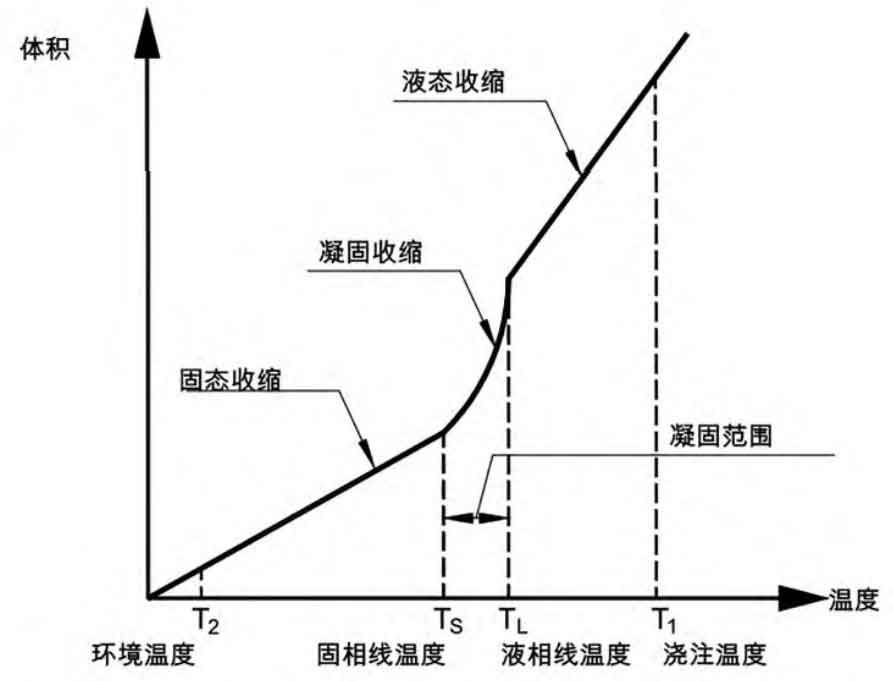
The formation of shrinkage porosity in the casting is shown in Figure 2 below. Start pouring when the pouring temperature is T1, and the height of the molten metal in the mold cavity can reach the plane A1; At this time, the molten metal starts to shrink in liquid state. When the temperature of the casting in the mold cavity drops to the liquidus temperature TL, the height of the molten metal drops to the plane Al, and then solidification shrinkage begins.
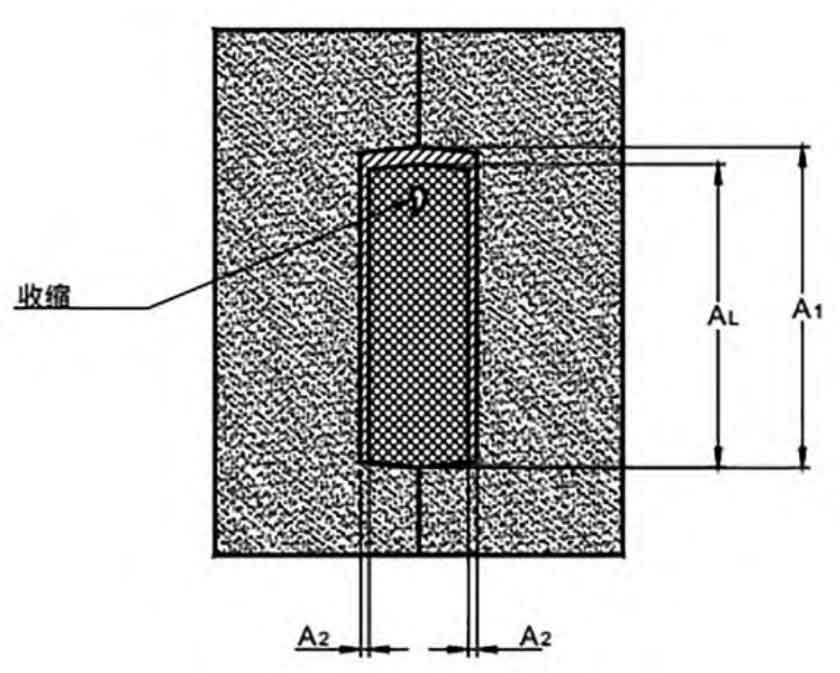
Since the temperature of the sand mold is far lower than the temperature of the molten metal, the heat of the molten metal is exchanged through the contact surface of the sand mold. From high to low, the heat flows from the inside of the molten metal to the outside, and the metal contracts and solidifies inwards from the contact surface of the mold wall. However, since the density of the solid metal is greater than that of the liquid metal in Fig. 2, and the volume in the solid state is smaller when the mass is the same, the casting will continue to shrink during solidification until the solidus temperature TS is reached. The solid metal shrinks until the casting temperature cools to the ambient temperature T2, and the casting will be slightly separated from the mold wall A2.
Therefore, in the process of liquid cooling and solidification contraction, the outer side of the molten metal starts to solidify into a shell, and gradually solidifies toward the inner side. However, when the inner molten metal (that is, the last solidified part) turns into a solid state, its volume decreases, but it cannot be supplemented by the molten metal, which will lead to shrinkage cavities due to contraction.
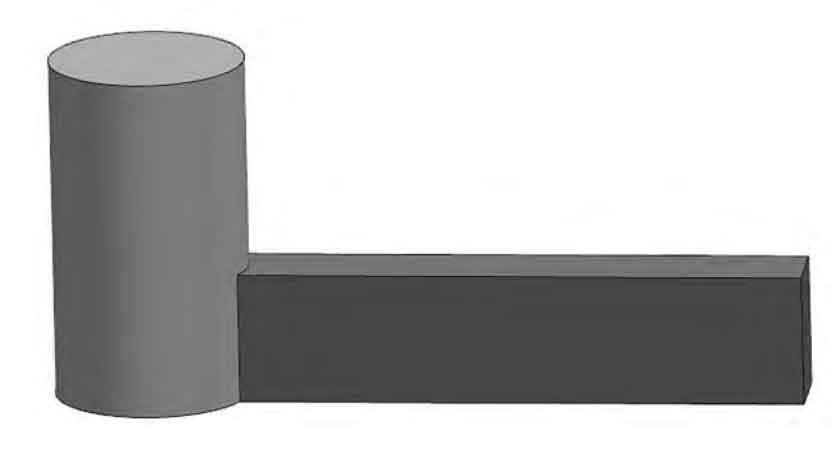
In the design of casting process, it is usually necessary to change the solidification sequence of castings by placing risers and chill, so as to achieve the goal of no shrinkage porosity and shrinkage cavity in the castings. However, in the actual process design, there will be some products with limited feeding channels due to structural reasons, which solidify earlier than the hot spot, and isolated hot spot is easy to form inside the casting, resulting in shrinkage porosity and shrinkage cavity defects.
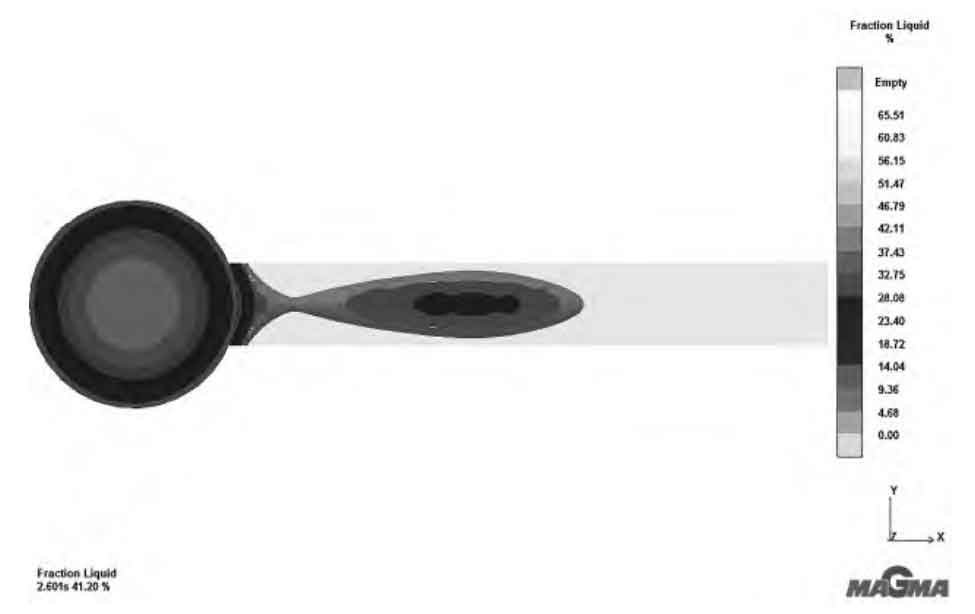
A simple three-dimensional model is designed as the model analyzed in this paper, as shown in Fig. 3, which is divided into riser and casting. According to the analysis of the simulated solidification process, as shown in Fig. 4, during the solidification process of the casting, the feeding channel is interrupted, and shrinkage porosity defects are easy to form in the casting.
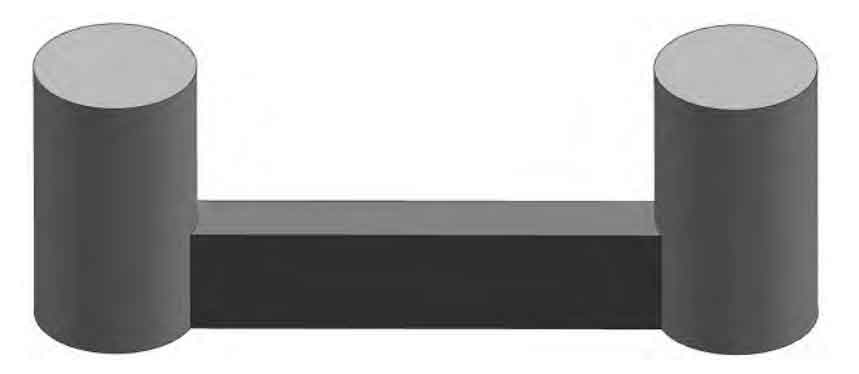
Normally, this problem can also be solved by adding a riser or a cold iron. As shown in Fig. 5, adding a riser at the distal end of the casting, or as shown in Fig. 6, adding a cold iron at the distal end, may solve the shrinkage problem. However, in practical application, due to the product structure or production line, the applicability of this solution is not comprehensive, We need to think about more solutions to help process personnel provide more solutions.
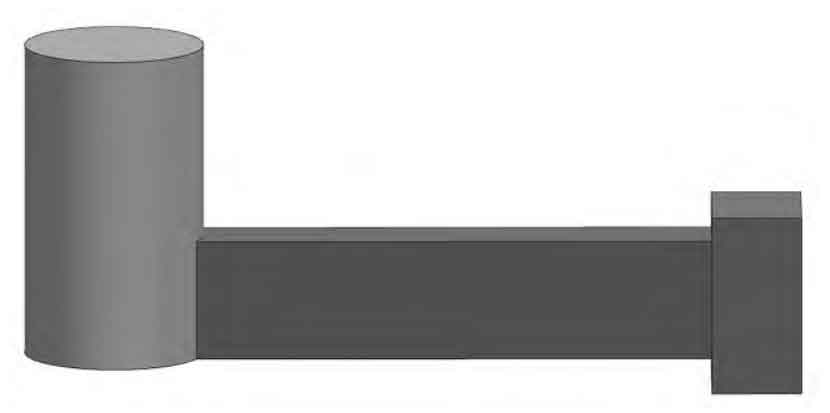
In the analysis and design of casting process, the process subsidy for castings is also a common solution, also known as metal subsidy. The feeding channel of castings is established through metal subsidy. In addition, the dark subsidy and heat subsidy schemes are also ideal solutions.
This simple model will be used as a carrier to discuss three solutions for establishing the feeding channel: metal subsidy, dark subsidy and heat subsidy, and compare the advantages and disadvantages of the three subsidy schemes as well as their application scenarios, so as to provide more options for process design.