Steel casting coating can be applied in various ways according to different site conditions and different steel castings. Through the combination of coating and application methods, the production efficiency and comprehensive performance can be improved and the production cost can be reduced. This paper introduces the application cases of different coating processes in actual production.
(1) A factory uses Baozhu sand resin sand process to produce valve steel castings. The single piece weight of steel castings is 50~2000 kg, the maximum thickness is 200 mm, and the materials are WCB, CF8, CF3, etc. The steel casting coating used by the factory adopts the brushing process of brushing once for small parts and twice for large parts. The Baume degree is 70 ° B é for the first time and 65 ° B é for the second time. After ignition and combustion, the coating has good strength without powder dropping. After unpacking, the surface of steel castings is in good condition without sand sticking. The field application shows that all properties of the cast steel coating meet the actual application requirements and achieve satisfactory results. The steel castings after painting and shot blasting are shown in Figure 1 and Figure 2.
(2) A factory uses 40~70 mesh silicon sand furan resin sand process to produce steel castings with a single piece weight of 50~10000 kg. The steel castings produced are valves, pumps, impellers, etc. and the materials are high alloy steel, low alloy steel, carbon steel, etc.
Originally, alcohol based zircon powder coating was used, and the coating method was mainly brush coating, with a small amount of flow coating. Now it is replaced with cast steel coating brush for 3 times, the first time Baume degree is 70 ° B é, and the other two times are 60 ° B é. After ignition and combustion, the coating has good strength without powder dropping. After unpacking, the surface of steel castings is in good condition without sand sticking. The field application shows that all properties of cast steel coating meet the actual application requirements. The steel castings after painting and unpacking are shown in Figure 3 and Figure 4.
(3) For large steel castings similar to steam turbines, the sand mold and clay core are usually large, and the coating application has the problems of low efficiency and low coating quality. Therefore, the airless spraying method is adopted to improve the efficiency and application effect.
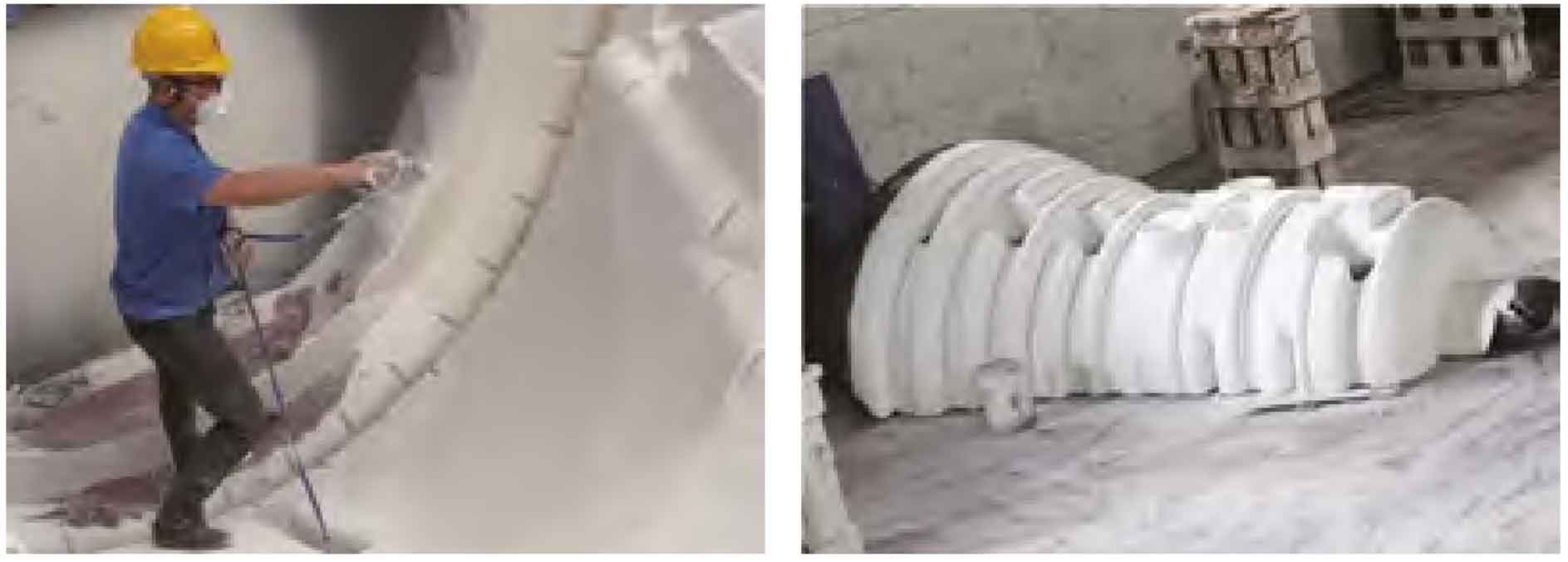
Steel castings for steam turbines were produced by alkaline phenolic resin sand process in a factory. The steel casting coating is applied by airless spraying. The coating is sprayed for 3~4 times with a Baume degree of 65~70 ° B é. After each spraying, it is ignited and dried, and the subsequent coating is continued after the sand mold temperature is reduced. Using this coating process can not only meet the requirements of steel castings, but also improve the production efficiency. The steel castings after coating and unpacking are shown in Figure 5 and Figure 6.
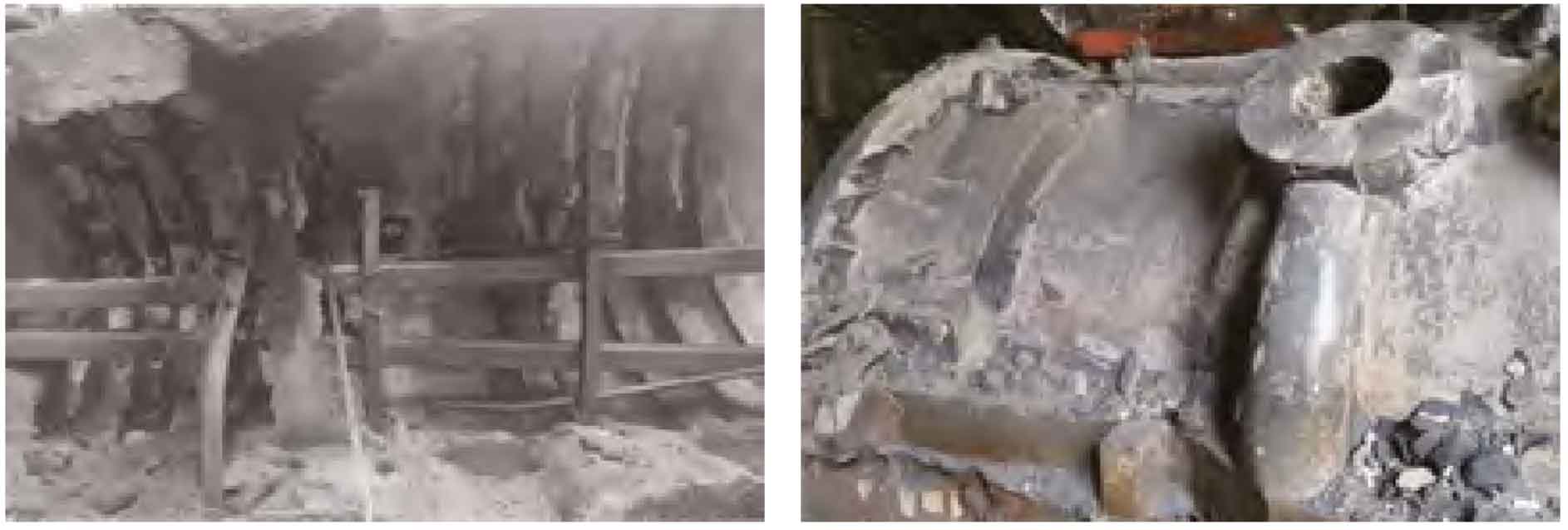
With cast steel coating, the original painting process takes 2 people and 2 hours to complete, and the improved airless spraying takes only 1 person and 1 hour to complete. Through different coating processes, the production efficiency of effective unit space is greatly improved, and the labor intensity and production cost are reduced at the same time.
(4) For steel castings with single size and mass production, the flow coating method can also be used to further improve the production efficiency. The flow coating process can eliminate the surface brush marks caused by the brush coating process and improve the surface quality of the coating.
A factory adopts alkaline phenolic resin sand process to produce medium and small steel castings made of carbon steel and low alloy steel. The flow coating process is adopted, and the Baume degree of the coating is controlled at 60~65 ° B é. After the flow coating is applied once, the hot spot is brushed again to ensure the coating thickness. After unpacking, the steel castings have excellent peeling performance and meet the requirements of customers. As shown in Figure 7 and figure 8.