In China’s casting industry in recent years, the output of steel castings has increased year by year, reaching 5.9 million tons in 2019, accounting for 12.1% of the total output of castings; In 2020, it will reach 6.35 million tons, accounting for 12.2%. Steel castings are widely used in petrochemical, pump and valve, mining machinery, nuclear power, marine equipment and other fields. The quality of steel castings has a decisive impact on the equipment manufacturing industry.
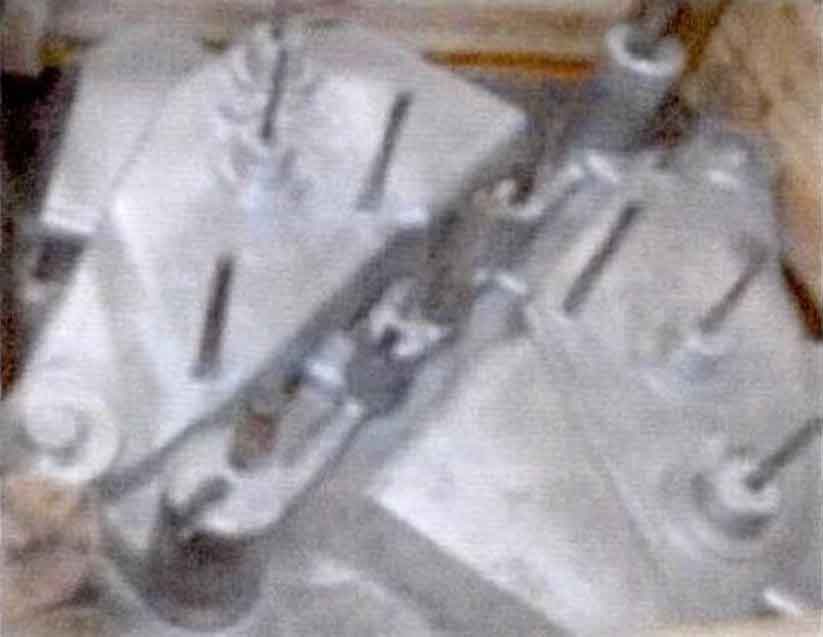
Steel castings, especially thick and large steel castings, due to the high temperature of molten steel during pouring, the liquid steel stays in the liquid state for a long time, and the surface of molten steel is easy to oxidize, which is very easy to produce permeable bonded sand and iron clad sand, which brings great difficulties to the cleaning of castings. For a long time, to solve the surface quality problems of steel castings, most of them use chromite sand as surface sand, and then brush the surface with zircon powder as aggregate paint for different times. This solution not only solves the problems, but also brings about problems such as increased production costs, high labor intensity, complex operation and so on.
According to the characteristics of steel castings and the application scheme of on-site coating, a zirconium free composite coating combined with the optimized coating application scheme can improve the production efficiency, reduce the labor intensity and reduce the production cost while ensuring the coating performance.
Coating plays an important role in the surface quality of steel castings. No matter what casting process is adopted, the coating must meet its requirements. Practice has proved that in the production practice of steel castings, the performance indexes of zirconium free composite coating tl405b meet the production and use requirements. Because its refractory aggregate is non zirconium material, the source and price of raw materials are free from foreign resource constraints, and the production cost is greatly reduced. Through the selection of appropriate application methods, reduce labor intensity, improve site turnover in limited space, improve production efficiency, and reduce comprehensive costs. Of course, as the application and promotion of zirconium free composite coating, it can not completely replace the use of zircon powder coating, but it can be promoted and applied in the process of most steel casting products.