Abstract: This article presents an in-depth study on the application of coated sand in steel casting production. It introduces the shell making process, production process flow, raw materials, core sand formulations, and process properties of coated sand. The article analyzes the factors influencing the quality of coated sand used in steel casting production and summarizes the economic benefits brought to enterprises by the introduction of coated sand technology. Through detailed descriptions and analysis, this article aims to provide guidance and reference for steel castings manufacturers in optimizing production processes and improving product quality.
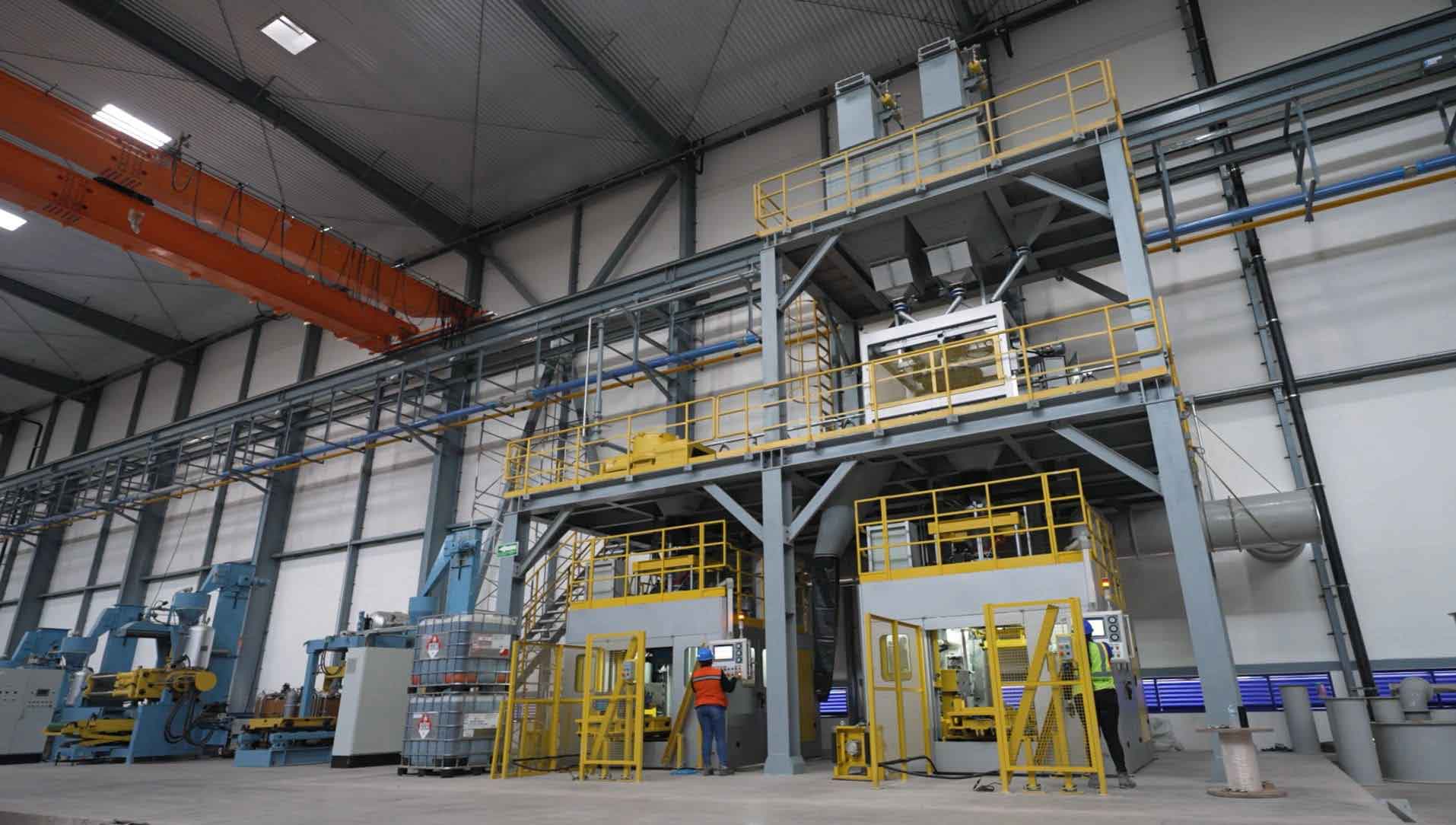
1. Introduction
Steel casting is an important part of the modern manufacturing industry, widely used in various fields such as machinery, automotive, aerospace, and shipbuilding due to its excellent mechanical properties and processing performance. In the production process of steel castings, the selection of molding materials plays a crucial role in determining the quality and efficiency of the castings. Coated sand, as a new type of molding material, has been widely used in steel casting production due to its excellent performance. This article will conduct an in-depth study on the application of coated sand in steel casting production.
2. Production Equipment and Process Flow
2.1 Core Making Equipment
The core making process in this company is carried out using two Z8957CE vertical parting hot-box core shooters. Before production, operators check the tightness of the mold and ensure there are no exposed wires on the heating element. During core making, parameters such as shooting temperature and holding time are set, with a shooting temperature of 260-270°C and a holding time of 3-3.5 minutes. After the sand core is removed, the sand nozzle is cleaned, and the flash is ground flat. One coat of alcohol-based zirconium silicate powder paint is applied, followed by core assembly, mold closing, and pouring operations.
2.2 Raw Material Requirements
The silica sand used is locally sourced and selected for its high quality. The binder and curing agent used in the coated sand also have specific performance requirements.
Table 1: Performance Indicators of Regional Selected Silica Sand
Category | SiO2 (%) | Angularity Coefficient | Mud Content (%) | Fine Particle Content (>200 Mesh) (%) | Moisture Content (%) | Particle Size (70/100) |
---|---|---|---|---|---|---|
Indicator | 98-99 | 1.1 | <0.3 | 0.73-0.80 | 0.018 | 0.44% |
Table 2: Performance Indicators of Binder
Category | Softening Point (°C) | Polymerization Speed (s) | Fluidity (mm) | Free Phenol (%) |
---|---|---|---|---|
Indicator | 95 | 60 | 61-65 | 0.003 |
Table 3: Coated Sand Process Parameters
Category | Raw Sand | Resin Addition | Surfactant Addition | Stearic Acid Calcium Addition | Curing Agent Addition | Coating Cycle (min) |
---|---|---|---|---|---|---|
Indicator (% of raw sand mass) | 100 | 2.7-2.9 | 0.1-0.5 | 0.1-0.6 | 1-5 | |
Indicator (% of resin mass) |
Table 4: Performance Indicators of Coated Sand Core Sand
Performance Indicator | Cold Bending Strength (MPa) | Hot Bending Strength (MPa) | Ignition Loss (%) | Melting Point (°C) | Particle Size (Mesh) |
---|---|---|---|---|---|
Value | 7.5-7.7 | 4.0-4.2 | 3.2-3.6 | 103-106 | 70/100 |
3. Factors Affecting the Quality of Steel Castings
The quality of coated sand is directly related to the final quality of the castings and is a crucial factor in ensuring casting quality. The quality of coated sand is closely related to the reasonable proportioning of high-quality raw sand, binder, and other process parameters. Any changes in these factors may affect the performance of the core sand.
3.1 Impact of Silica Sand
The composition of silica sand has a significant impact on the strength of the core sand. In silica sand, impurities other than silicon dioxide (SiO2) are generally considered harmful in the industrial context. Aluminum oxide (Al2O3) and iron compounds are the most common impurities, with iron compounds being considered one of the most harmful. These impurities can melt at high temperatures and react with various inorganic binders and oxides on the surface of the metal liquid, forming complex compounds with relatively low melting points. This not only leads to severe erosion and melting of quartz particles but also increases the channels for oxide slag and metal liquid infiltration, ultimately causing sand sticking on the surface of the castings. Therefore, it is desirable for silica sand to have a high SiO2 content and low content of other components to ensure high refractoriness. In practice, the SiO2 content is often used as the main acceptance criterion for casting silica sand.
3.2 Impact of Binder
Thermoplastic phenolic resin is used in the shell method for coated sand, and its performance can be classified into various types, including high-strength, fast-hardening, low-expansion, easy-collapse, low-odor, heat-resistant, and laser-selective sintering types. After trial production of automotive parts boxes, high-strength types were selected. The strength of coated sand mainly depends on the bonding strength between phenolic resin and sand and the cohesive strength of the resin itself. The bonding strength is related to the relative molecular mass of the resin; phenolic resin with a small relative molecular mass has good fluidity, which is conducive to full wetting and bonding between the resin and sand, thereby improving strength. To enhance the toughness of phenolic resin, appropriate modifying substances can be introduced during resin synthesis.
3.3 Impact of Tooling
The coated sand process has high requirements for tooling. The mold must be a metal mold. During the mold design process, considerations must be given to the feeding and exhaust of castings, shell thickness, and sand reduction, as well as the matching between the mold backing plate and the casting, and the size of the heating pipe. The pouring method adopts in-line casting, which can be either stacked in-line casting or horizontal in-line casting. The company has experience in horizontal in-line casting and corresponding tooling, and stacked in-line casting may result in the collapse of the lower 1-2 shells due to gravity, leading to scrap castings. Currently, the production volume is not high, so horizontal in-line casting is adopted.
3.4 Impact of Equipment
The equipment used is a coated sand core shooter. The core shooter requires setting parameters according to different shell cores. The main parameters include shooting pressure, shooting time, shelling time, curing time, left and right core box temperatures, sanding pressure, and sanding time.
4. Process Control Requirements for Steel Casting Production
4.1 Shell Control
The shell needs a certain strength, but if the strength is too high, the resin addition will increase, leading to increased gas generation and a higher probability of porosity in the castings. Therefore, a high-strength coated sand formulation is adopted to reduce resin addition and subsequently reduce the gas generation of coated sand. After selecting the type and formulation of coated sand, the hardening time and temperature of the shell are particularly important. These parameters need to be continuously tested in actual production to determine the optimal values. In actual production, the suitability of hardening time and temperature can also be judged by the color of the hardened shell, with tan being the optimal color, yellow indicating inadequate hardening, and black indicating overhardening.
4.2 Paint
If the shell has sufficient density, no paint is required. However, high-density shells incur higher costs. Therefore, considering cost, a moderately strong coated sand supplemented with paint is chosen to improve surface quality. Applying one coat of alcohol-based zirconium silicate powder paint can significantly improve the sand sticking on the casting surface. When applying the paint, avoid accumulation and blocking of air passages, and ignite immediately after application.
4.3 Pouring Temperature
The conventional pouring temperature for steel castings is 1560-1580°C. Currently, coated sand steel castings are mostly small parts, and a higher temperature has an adverse effect on the surface quality of the castings. Based on practical experience, a pouring temperature of 1560°C is preferred. The company’s current ladle is relatively large, so pouring is carried out later.
5. Economic Benefits of Introducing Coated Sand Technology
The introduction of coated sand technology has brought significant economic benefits to the company. Firstly, coated sand has excellent strength, surface quality, and collapsibility, making it easy to clean castings and store, transport, and use sand cores. This helps reduce the cost of raw materials and improve production efficiency. Secondly, the use of coated sand technology has effectively improved the surface quality of castings, reducing the incidence of defects such as sand sticking and porosity, thereby improving product quality and reducing scrap rates. Finally, the introduction of coated sand technology has optimized the production process, shortened the production cycle, and greatly reduced labor intensity and energy consumption.
Table 5: Comparison of Production Indicators Before and After the Introduction of Coated Sand Technology
Indicator | Before Introduction | After Introduction |
---|---|---|
Raw Material Cost | High | Low |
Production Efficiency | Low | High |
Casting Quality | Poor | Good |
Scrap Rate | High | Low |
Labor Intensity | High | Low |
Energy Consumption | High | Low |
6. Conclusion and Outlook
This article presents an in-depth study on the application of coated sand in steel casting production, introducing the shell making process, production process flow, raw materials, core sand formulations, and process properties of coated sand. The factors affecting the quality of coated sand used in steel casting production were analyzed, and the economic benefits brought by the introduction of coated sand technology were summarized.
The application of coated sand technology in steel casting production has shown significant advantages in improving production efficiency, reducing production costs, and improving casting quality. However, there is still room for improvement in some aspects. For example, the current pouring package is relatively large, which may impact the surface quality of castings. Therefore, efforts should be made to adopt smaller pouring packages in the future to reduce the impact of steel water head on the shell and thereby reduce defects such as surface sand holes. In addition, as production volumes increase, it is necessary to establish an independent production system, including melting furnaces and steel ladles.
Overall, the coated sand process has simple equipment, a short production cycle, strong core sand collapsibility, and significantly reduced operation difficulty in various processes, saving considerable labor, equipment, and energy costs. It is expected that with the continuous development of technology and equipment, the application of coated sand in steel casting production will become more widespread, playing a more important role in promoting the development of the steel casting industry.