In order to test the carbon content in austenite during austenitizing, gsl-1500x 1500 ℃ high temperature vacuum tube furnace was used to austenitize the flake samples taken from ductile iron test bars with casting modulus of 0.25cm, 0.50cm and 1.25cm under the protection of argon. The heating rate was 10 ℃ / min, and the furnace temperature control accuracy was ± 5 ℃. A small hole with a diameter of 1 mm is drilled at 1 / 2 of the sample radius (for sampling through fine wire during heat treatment). The austenitizing temperature is 880 ℃, 920 ℃ and 960 ℃, and the holding time is 1.4h, 1.7h, 2.0h, 2.3h, 2.6h and 2.9h. There are three groups of 54 samples, which are quenched into 24 ℃ water immediately after heat preservation.
Sg2-7.5-12a intelligent box type resistance furnace is selected to heat up the sample, and the furnace temperature control accuracy is ± 10 ℃. In the process of heating and austenitizing, graphite powder is used to bury the sample to prevent oxidation and decarburization at high temperature. The salt bath furnace modified by well furnace is selected to austemper the austenitized sample. The well furnace, salt bath and the salt bath furnace are shown in the figure. The temperature control accuracy of the salt bath furnace can reach ± 2 ℃ after several debugging before the test. The composition of bath salt in this experiment is: 50% KNO3 + 50% Na NO2. Meanwhile, during the test, the mass ratio of bath salt to parts should be controlled above 10:1.
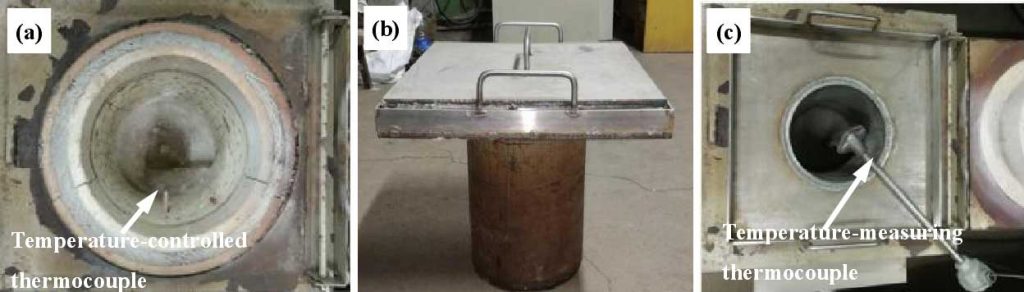