The four major processes of traditional automobile production are stamping, welding, spraying and assembly. The rear frame is made of steel: the first step is to press the steel plate into small parts, then weld the sub-parts into assembly parts, and finally assemble. The integrated casting process is to change stamping into casting, and the raw material is changed from steel to aluminum alloy; A large part can be directly cast and bolted without welding. This greatly reduces the time of stamping, welding and assembly. By applying the integrated casting technology, the four major processes of the original automobile industry manufacturing system will be simplified into three major processes.
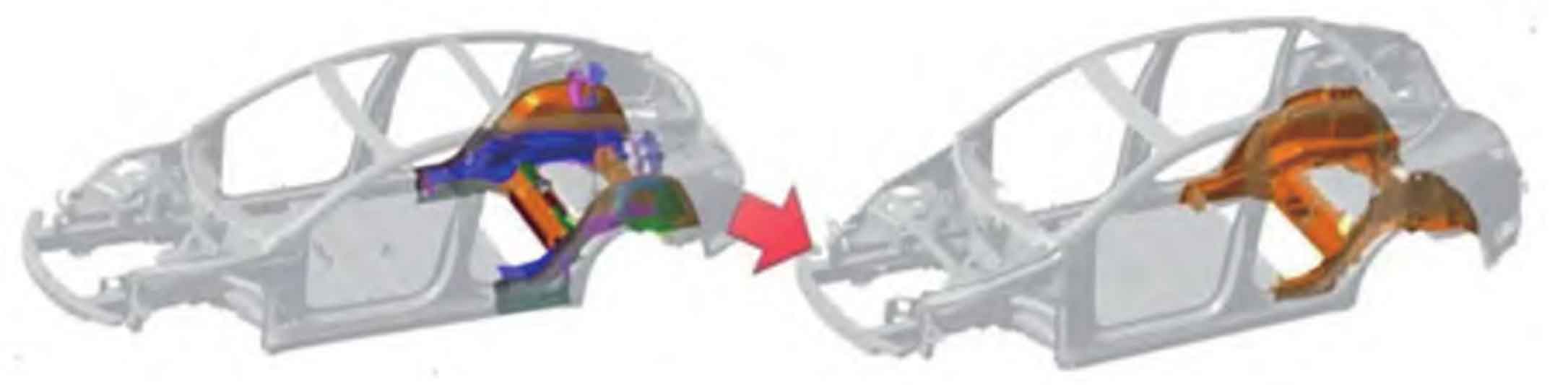
The traditional rear frame is formed by stamping, welding and assembling 70 to 80 parts, while the integrated casting is a large part. The total manufacturing time is reduced from 2 to 3 hours to 1.5 to 2 minutes, and the assembly process of screws and nuts is reduced by 50 robots, which also shortens the production line and saves 30% of the floor area. In terms of labor, the welding workshop needs 20-50 workers, but the integrated casting workshop only needs 8-15 workers. In addition, large aluminum alloy parts make recycling more simple and efficient: if aluminum alloy parts have serious defects or scrap in the production process, they can be directly recycled and melted into molten aluminum, and then cast. The material is not easy to waste, while scrap steel is difficult to do so. In other words, integrated casting has many advantages in the integration of parts and components, which can make the body lightweight, reduce the number of workers and assembly robots, improve efficiency, and shorten the manufacturing time of the supply chain and the whole vehicle. The integrated casting design for the rear frame of new energy vehicles is shown in the figure.