In order to ensure that the connecting rod has sufficient stiffness and strength under the condition of light structure, in the past, high-quality medium carbon structural steel with selected carbon content, such as No. 40 steel or No. 45 steel, was generally used for die forging. The hardness of 45 steel is 217-293hb and that of 40Cr is 223-280hb. Medium carbon alloy structural steels, such as 40Cr, 40CrMo, 35CrMo, etc., are used in high-speed strengthened engines. Alloy steel has high comprehensive mechanical properties, but when there are factors that produce stress concentration, its fatigue resistance drops sharply, even as low as carbon steel. Therefore, more attention must be paid to the shape design, transition smoothness and surface quality of alloy steel connecting rod in order to give full play to the potential of high-quality materials. Penggang materials, such as 40MnB and 40mnvb, have shown good performance as mass-produced connecting rod materials with high load. The main medium carbon quenched and tempered steel materials for manufacturing connecting rods include 42CrMo, 35CrMo, 45mnvb, 45crmnb, s48cl2, 35mnv, 40mns, SAE1141, etc. For example, FAW CA488 connecting rod is made of 40mn2s material, the chemical composition (%) is: C 0.37 ~ 0.45, mn1.35 ~ 1.65, P ≤ 0.04, s 0.08 ~ 0.13, and the hardness after quenching and tempering is hb229 ~ 269.
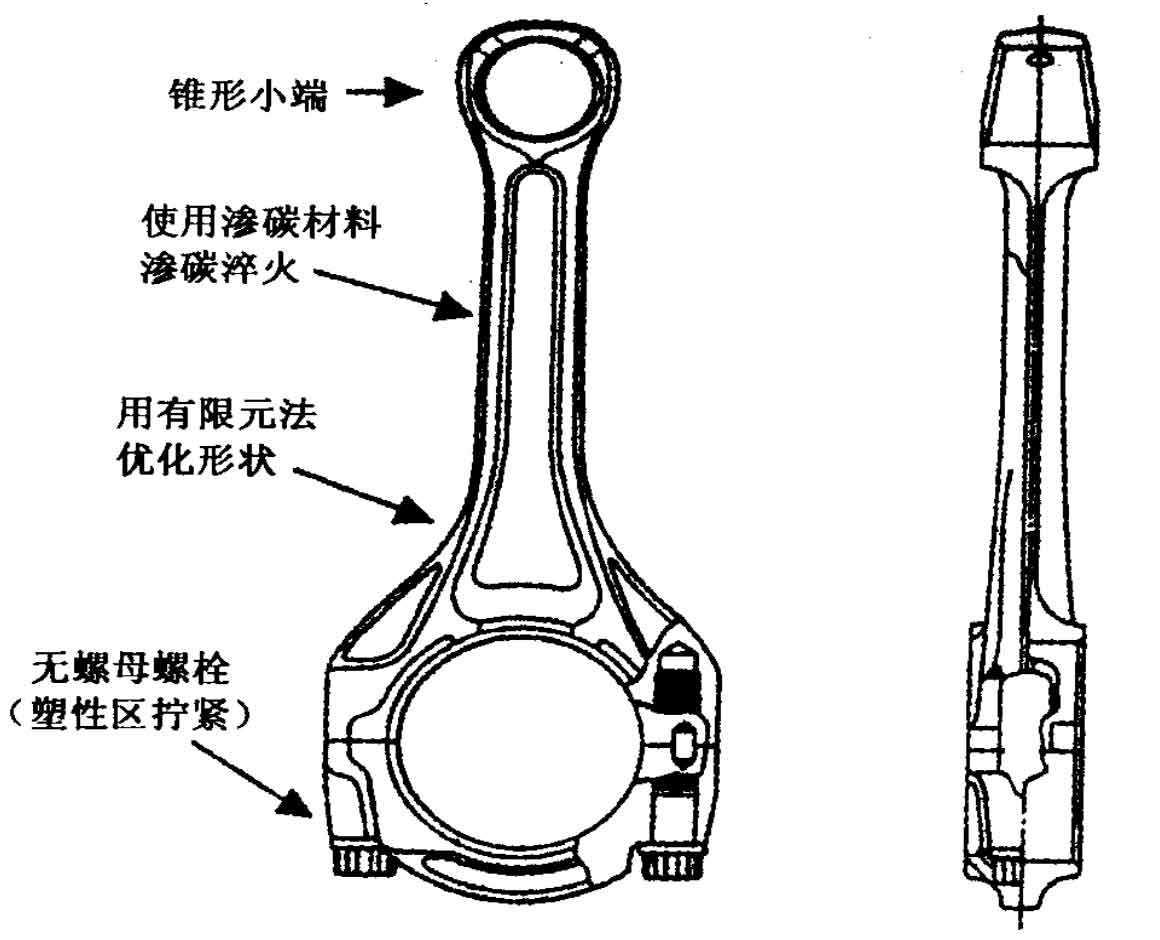
In recent years, medium carbon microalloyed non quenched and tempered steel has also been used to make connecting rods, which has been widely used in Europe, America and Japan. The engine connecting rod is made of high carbon steel on mass-produced cars and light vehicles. For example, FAW Jetta engine connecting rod is made of 70 high carbon steel with a sulfur content of 0.08%.