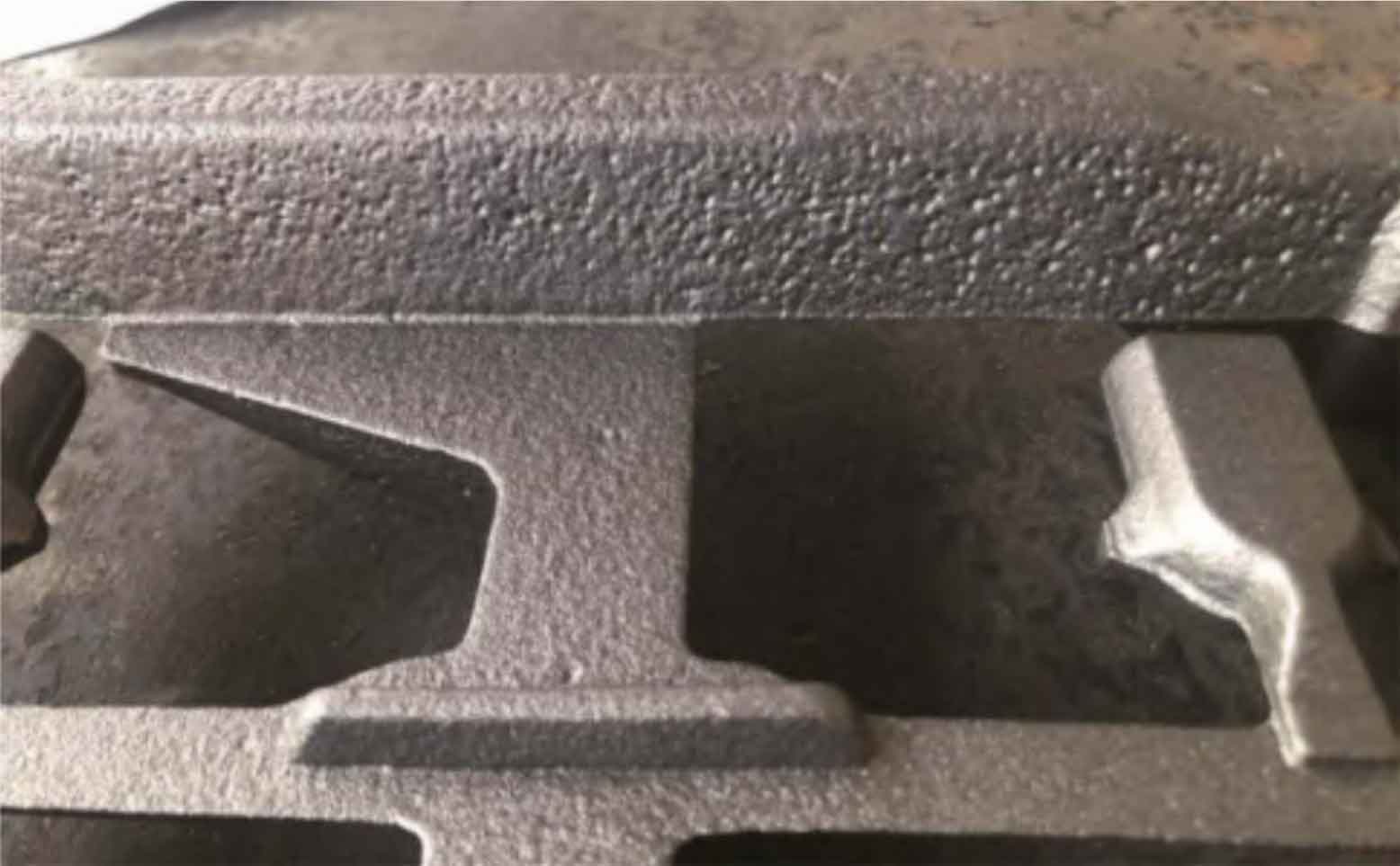
After successfully carrying out the above tests, the company canceled the pulverized coal in the molding process of the existing production line for precision casting of the cylinder base containing pulverized coal and conducted the pouring test. It was found that the air holes appeared in the pouring system and the inner cavity of the precision casting successively. Figure 1 shows the air hole on the lower surface of the transverse runner of the gating system, Figure 2 shows the air hole found after the processing of the KJ248 cylinder base precision casting, and Figure 3 shows the air hole found at the stator foot after the processing of the cylinder base precision casting.
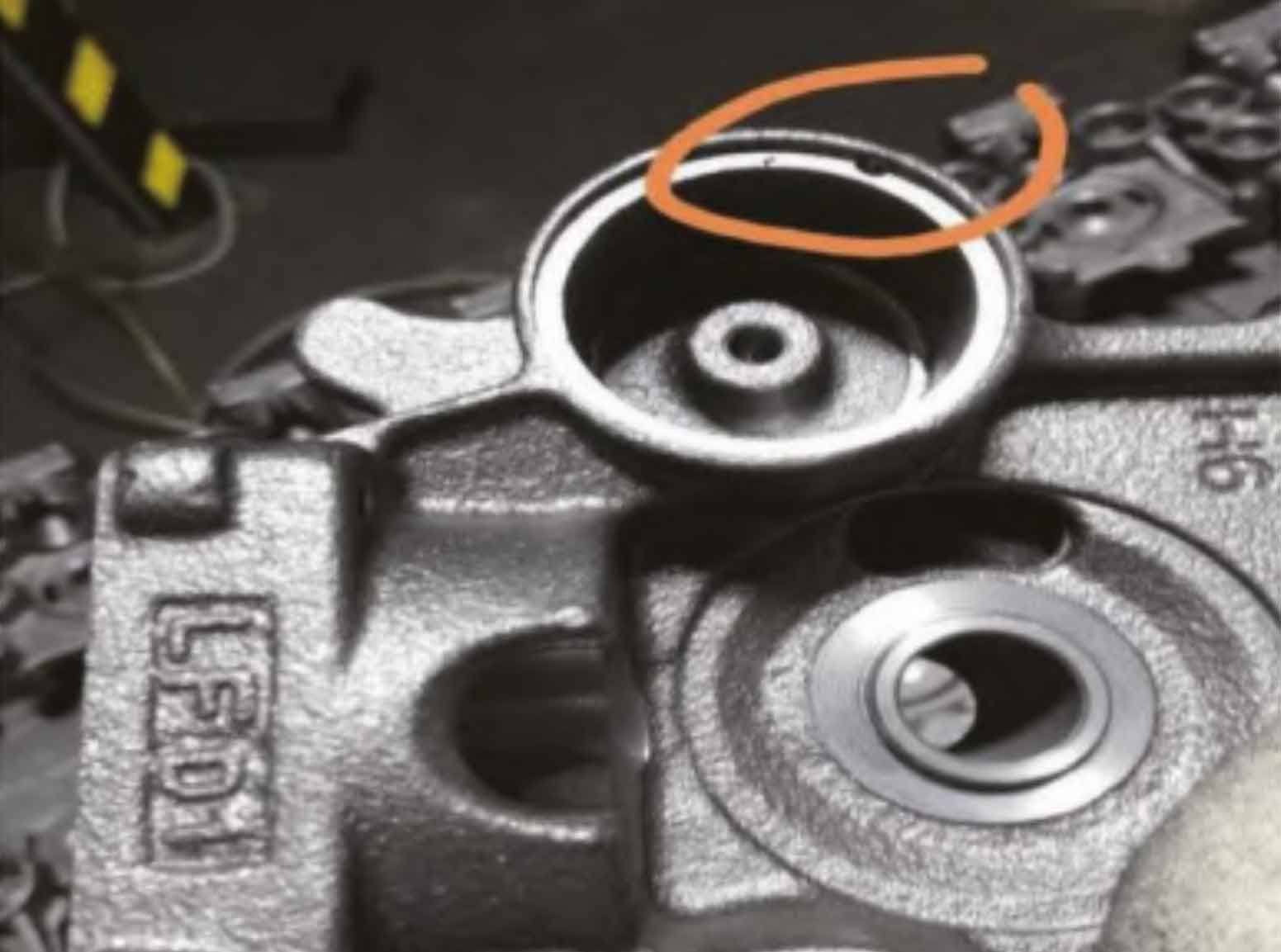
Compared with the test results of the new sand and the existing production line with pulverized coal, it is analyzed that the root cause of the blowholes in the precision casting after the cancellation of pulverized coal is that the degree of fish egg petrification (the surface of the molding sand is firmly coated with a layer of dead burned hard bentonite) of the two kinds of molding sand is completely different, that is, the oolization rate is different. Oolitization rate refers to the dead clay layer (particle diameter greater than 20) attached to the sand after the molding sand is roasted at 900 ℃ μ m) , as a percentage of the mass of sand particles after heating and cleaning. The determination method of oolization rate of the two types of molding sand is as follows: take 50 g of clay sand calcined at 900 ℃ for 4 hours, put it in a beaker, add 200 ml, 6 mol/L hydrochloric acid solution, boil it for 25 minutes, take out the sand and wash it with distilled water, test the pH value of the distilled water after washing, until it no longer shows acidity; Take another empty beaker, add washed sand, KOH (60 g) and distilled water (250 ml) respectively, and boil the beaker for 25 minutes. Also take out the boiled sand, wash it in a new empty beaker with distilled water, and test the pH value of the distilled water after washing until it no longer shows alkalinity. Finally, dry and weigh the residual sand and calculate the mass percentage between the residual sand and the test sand sample, which is the oolization rate of the clay sand during the heating process of the test sand sample.
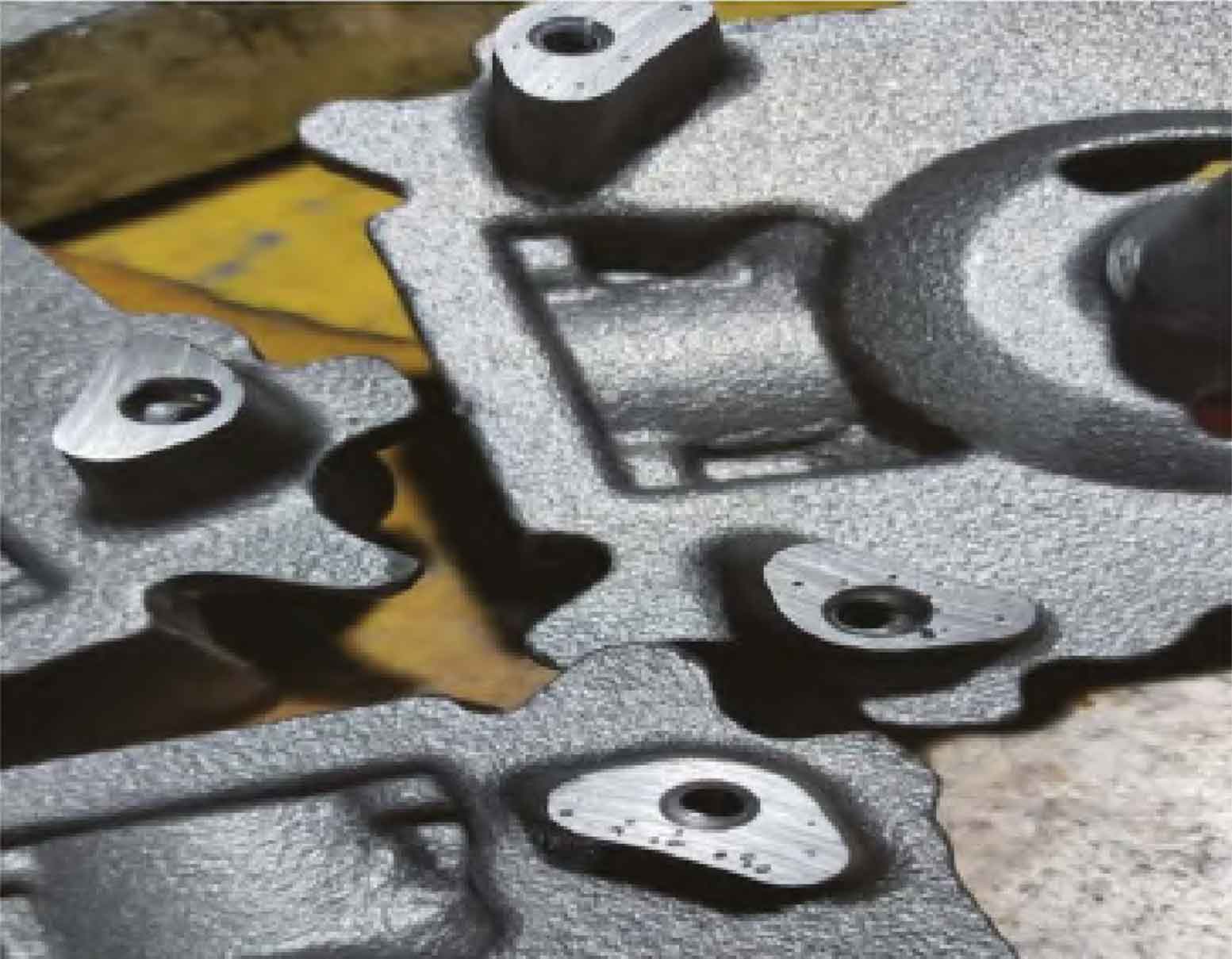
The molding sand with high oolization rate has high water content and low melting point, which is easy to produce porosity and sand sticking defects. When recycling the old sand, it is necessary to add new sand to reduce the use proportion of the old sand. In the subsequent molding sand performance test, it is found that the higher the oolization rate, the lower the shear strength of the molding sand. Table 1 shows the corresponding relationship between oolization rate and shear strength of molding sand, and Figure 4 shows the testing instrument for shear strength of molding sand.
Production line | Shear strength of molding sand/kPa | Oolitization rate of molding sand (%) |
130 | 27 | 20.11 |
130 | 45 | 17.11 |
230 | 29 | 22.47 |
230 | 46 | 17.33 |
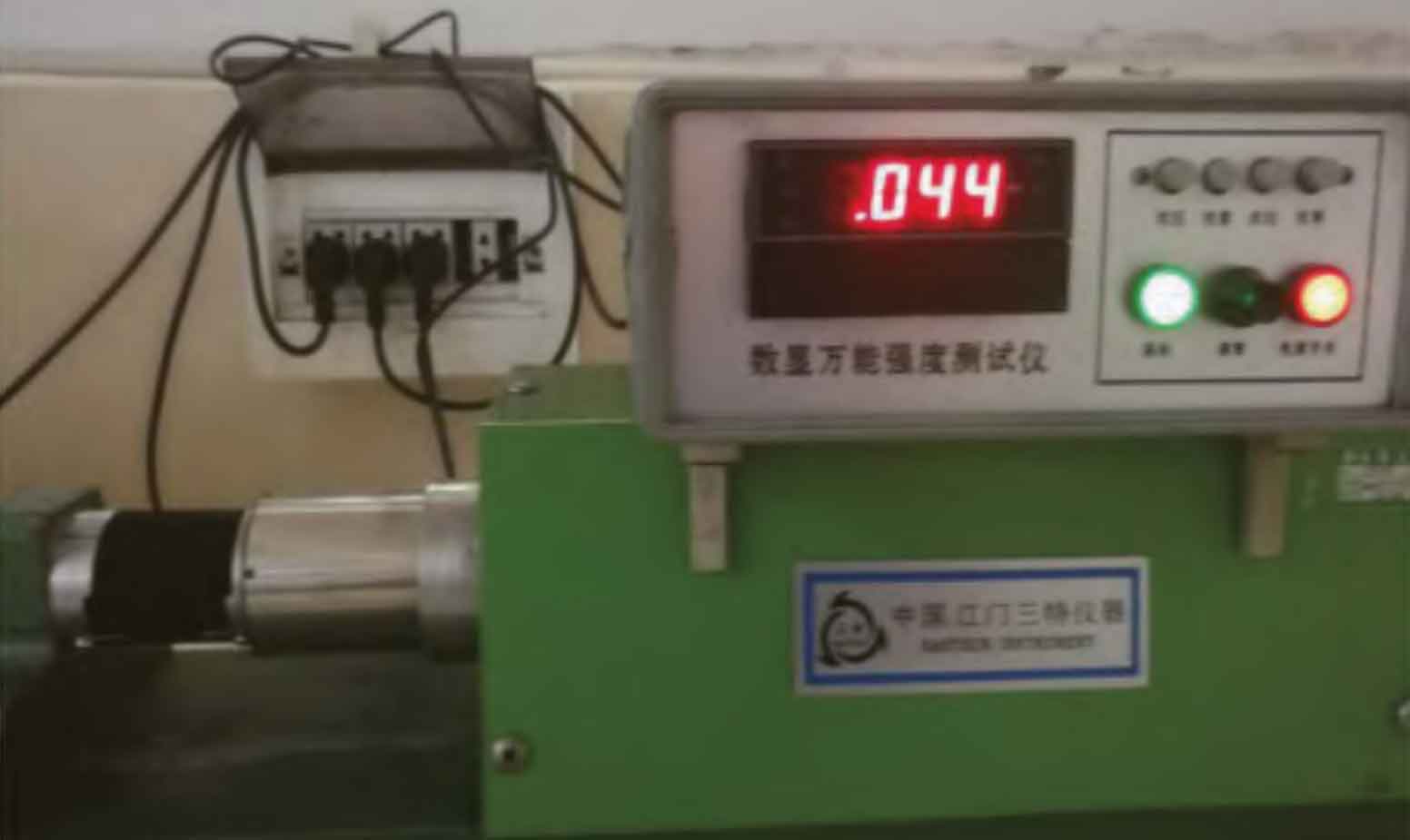
In the process test of recycling old sand, the goal of reducing the oolization rate of molding sand is to increase the amount of new sand, and the air hole defect of the cylinder block precision casting is gradually reduced until it is eliminated. When the old sand is recycled, the best oolization rate of molding sand should be controlled at less than 15%. Table 2 shows the corresponding relationship between the oolization rate of molding sand recycled from used sand and the porosity defects of precision castings.
Amount of new sand added (%) | Oolitization rate of molding sand (%) | Percentage of air holes in cylinder seat flaw detection (%) |
0.30 | 19.86 | 6 |
0.50 | 17.34 | 3 |
0.70 | 15.66 | 1 |
1.00 | 14.82 | 0 |