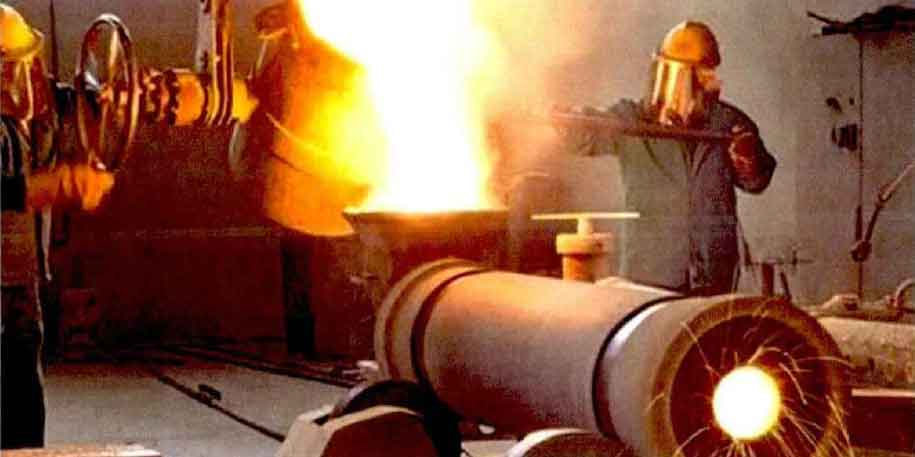
The microstructure and characteristics of the bonding interface play a key role in the macro mechanical properties of the composite roll. Therefore, it is necessary to clarify the relationship between the phase composition and microstructure of the bonding interface of the composite roll, the diffusion of interface elements and the outer metal. By studying the bonding interface morphology of centrifugal casting outer high chromium cast iron and inner 45 steel bimetallic roll (outer wear resistance and inner toughness are good), it is found that the interface structure consists of high chromium solidification structure, transition zone (decarburization zone), carburization zone and 45 steel structure. The carbides in the high chromium solidification structure are mainly strip M7C3 with high hardness, and the amount of M7C3 carbides in the transition zone is significantly reduced, The carburized zone is caused by the pearlite structure formed by the diffusion of carbon element to the core 45 steel under the action of thermal diffusion; The preheating temperature of the pipe mold and the holding time of the inner and outer metals at the high temperature stage have a significant impact on the interface bonding performance. For example, the longer the holding time, the longer the liquid-solid interaction time and the enhanced diffusion ability of C and Cr across the interface can significantly increase the thickness of the diffusion layer, effectively avoiding the failure problems caused by the pores, cracks and spalling at the roll interface. In addition, by controlling the liquid metal temperature, the microstructure and thickness of the bonding layer of the outer high chromium white cast iron and the inner low alloy steel composite roll were studied. It was concluded that the uniform distribution of interface composition and microstructure was closely related to the inner and outer metal temperatures. The higher the temperature of low alloy steel after solidification, the better the interface bonding effect. The higher the pouring temperature of the outer high chromium cast iron, the thicker the bonding layer. Based on ProCAST platform, Lu et al. Established the finite element model of composite roller centrifugal casting with Cr4 steel as the outer layer and nodular cast iron as the inner layer, and concluded that the composite process of composite roller centrifugal casting can be divided into three stages, namely, outer layer centrifugal casting, middle layer centrifugal casting and core layer gravity filling casting, and conducted experimental research; The interface structure and grain size obtained at different cooling rates are different, mainly pearlite and martensite. The amount of pearlite increases due to the massive diffusion of interface carbon elements; When the temperature of the middle layer is higher, the temperature of the outer surface and the inner surface is lower; When the temperature of the middle layer is low, the non-uniformity of the inner and outer surface temperature will lead to the loose combination of the inner layer and the middle layer, which is easy to cause the roll to peel off. Therefore, in order to realize the close combination of the composite roll interface, it must rely on the pouring interval between the inner and outer layers Δ The good match between T and inner pouring temperature T makes the inner surface of the outer alloy melt to a certain thickness under the action of the pouring heat of the inner metal liquid, so as to ensure the metallurgical bonding quality. However, a metallurgical bonding area composed of a mixed thin layer of two alloys and a melted but unmixed thin layer of the outer alloy is often formed near the contact surface of the inner and outer alloys, so as to determine the inner The criterion for good bonding effect of outer layer is:

Where: Δ T is the pouring interval between inner and outer layers, min; TS1 and TS2 are the solidification time of outer layer and inner layer respectively, min; T internal pouring is the pouring temperature of inner layer, ℃; TL1 and TL2 are the liquid phase temperature of outer layer and inner layer respectively, ℃.
In addition, there are actually “four zones and three interfaces” at the interface between the working layer and the core of the centrifugal casting composite roll: unmelted zone, semi molten zone, molten zone, core layer, interface between unmelted zone and semi molten zone, interface between semi molten zone and molten zone, and interface between molten zone and core layer. The ultrasonic flaw detection technology can be used to detect the bonding effect of the intermediate layer of the centrifugal casting composite roll and give the judgment basis, The typical echo waveform is shown in figure . As shown in Figure a, the A-shaped echo is located at the interface between the normal semi melting zone and the melting zone, which is caused by the segregation of distorted graphite, molten iron sulfide and iron slag, among which the non-metallic slag inclusion has the greatest impact. The segregation of distorted graphite and sulfide can be reduced by prolonging the condensation time of the outer metal liquid and reducing the temperature of the roll core metal liquid. As shown in Fig. b, B-shaped echo is another derived form of interface metallurgical bonding. There will be “interference” phenomenon at the front of the echo, which is caused by the “grass” echo formed by the segregation of interface components or the symbiosis of different tissues. It can be eliminated by controlling the appropriate core filling pouring temperature. As shown in Figure C, C-shaped echo is a common “double wave” phenomenon in ultrasonic flaw detection technology. Once “double wave” occurs, the first echo shall be used as the basis for judging the product quality. As shown in Figure D, the D-shaped echo is a double echo, which is a fatal defect of the roll and is easy to cause the roll to peel off.
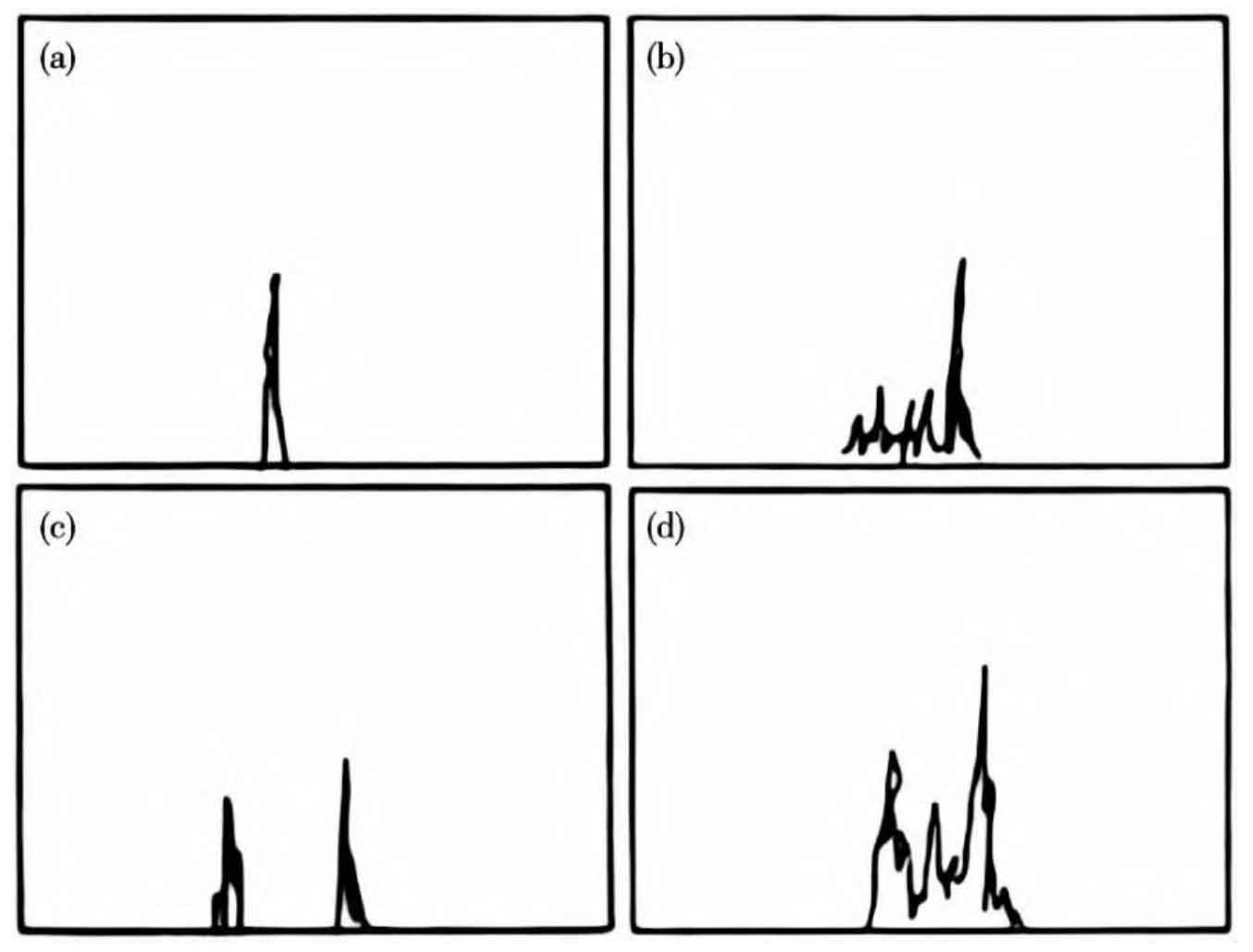
In the research of centrifugal casting bimetallic composite roll, domestic and foreign scholars, based on physical methods and mechanical metallurgy, studied the composite law of the bonding interface and the criteria for obtaining good bonding quality through experiments and numerical simulation, but only gave the approximate range of good bonding interface, and did not involve how to accurately control the bonding strength of the bonding interface. At the same time, most of the simulation results are based on the thermal mechanical coupling and the simulation of prestress, ignoring the liquid-solid interaction of metal, which reduces the accuracy of temperature distribution prediction.