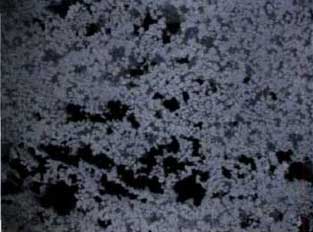
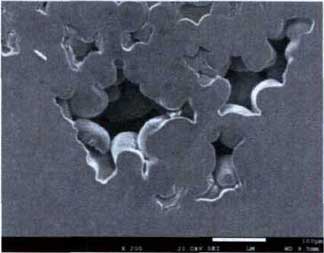
In the defect analysis of semi-solid thick wall products, shrinkage cavity and porosity are the typical defects studied. In the casting process, if the mold is not designed properly, there will be a local area where the metal solidifies more slowly than the surrounding metal, which is called “hot spot”. With the process of solidification, the hot spot area will solidify the slowest, resulting in the surrounding metal solidification. When the area is solidified again, it can not be filled. Finally, it is easy to form shrinkage defects in this position. Therefore, feeding is particularly important in casting. Some scholars also take the hot spot position as the main research object in mold design. In cast alloy, Si element will expand during solidification because This Al Si alloy has good filling and feeding properties, so the most commonly used aluminum silicon alloy in semi-solid casting is 319s. The observation of shrinkage cavity and porosity under metallographic microscope is shown in Fig. 1, and SEM scanning analysis is shown in Fig. 2
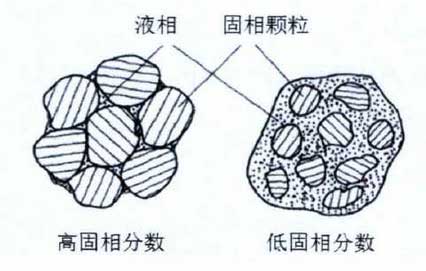
In the process of semi-solid casting, because the microstructure of semi-solid slurry is solid phase with high rigidity and liquid phase with high rheological property, semi-solid structure can be divided into two typical structures: high solid fraction and low solid fraction. As shown in Fig. 3, the solid content in semi-solid slurry with high solid fraction is mainly composed of A1 grains, which is closely arranged, and the liquid phase is isolated by connected solid phases In the solidification process of semi-solid slurry with low solid fraction, the slurry will continue to feed from the position close to the punch and the casting upward to the position of solidification shrinkage under the effect of pressurization pressure. If the feeding is smooth and smooth, the final solidification will not produce shrinkage cavity When the solid fraction of the material exceeds a certain value, the liquid phase becomes an isolated phase, which makes it difficult for the liquid phase to circulate in the solidification process, which leads to the position where the shrinkage value is difficult to be filled, resulting in the shrinkage cavity and porosity defect at this position.