The load of self-aligning ball bearing is shared equally by two rows of rolling elements. Then for each row of rolling elements, the contact normal load of the rolling element with the largest force is:
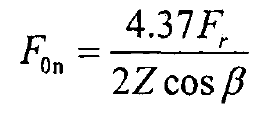
Where Z is the number of rolling elements in each column. At the rolling element, the sum of the elastic approach values of the inner and outer rings in the contact normal direction is as follows:

Where, subscripts I and 0 indicate that the rolling sphere contacts the inner ring and outer ring respectively. The relationship between normal elastic approach and radial elastic approach is as follows
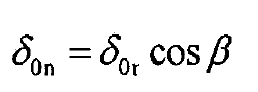
Therefore, the Hertz contact stiffness of the self-aligning ball bearing is:

Under elastohydrodynamic lubrication, the minimum oil film thickness between ball and raceway is calculated by using the minimum oil film thickness of Dowson

Where u, G and W are dimensionless velocity parameters, dimensionless material parameters and dimensionless load parameters, respectively, η 0 is the viscosity of lubricating oil under atmospheric pressure, ν is the average velocity at the contact between inner and outer rings and rolling element, e ‘is the equivalent elastic modulus (2.25x10000mpa for steel to steel contact), α 1 is the pressure index of lubricating oil viscosity, and Q is the pressure index along the normal direction of contact For self-aligning ball bearings, if the outer ring of the bearing is assumed to be stationary and the rotation speed of the inner ring is η I, then the expression of W is as follows:

Then the sum of the oil film thickness of each steel ball in contact with the inner and outer raceways is:
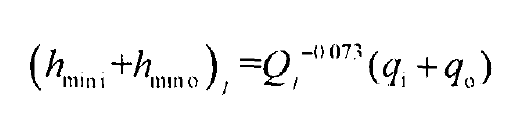
Then the oil film stiffness of single roller in contact normal direction is:
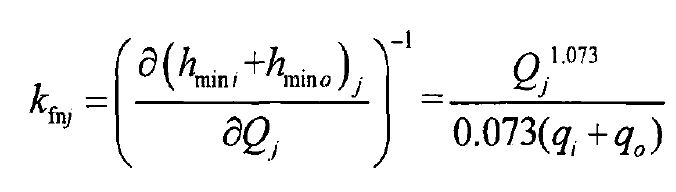
The oil film stiffness is the vector sum of the oil film stiffness of all loaded rolling elements
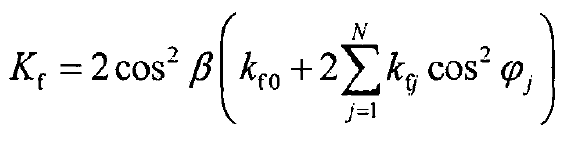
The stiffness of self-aligning ball bearing is obtained by series connection of Hertz contact stiffness and oil film stiffness
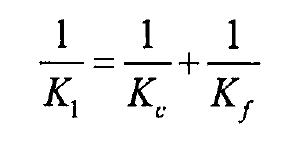
The stiffness K2 of the roller shaft can be easily obtained according to the mechanics of materials
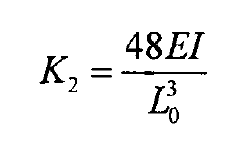
Where l0 is the distance between each pair of bearings and EI is the bending stiffness of the roller shaft.
The linear contact between the mold and the roller can be calculated by the contact deformation formula proposed by palmgren
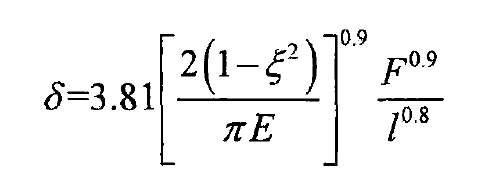
Then the contact stiffness between the mold and the roller can be obtained as follows
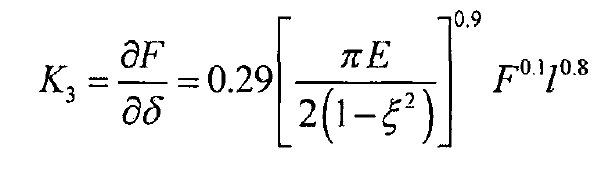
Where, 5 is the elastic modulus, ξ is the Poisson’s ratio, and ι is the effective contact width between the roller and the mold.