The casting quality will be seriously affected by the length of pouring time. The shorter the pouring time, the faster the pouring speed will be, the shorter the heat action time on the upper surface of the sand mold during filling can be reduced, thus reducing sand inclusion and scarring defects. For gray cast iron and ductile iron parts, rapid pouring can make full use of eutectic expansion to reduce shrinkage hole defects; however, too fast pouring can reduce shrinkage hole defects on the mold wall.It is easy to cause sand scouring and other defects due to its large impact.
When pouring slowly, the impact of metal on the mold wall is small, which can reduce sand scouring; however, if pouring time is too long, the surface of the cavity will be baked at high temperature for a long time, cracking and falling will occur, which will finally lead to casting defects such as sand inclusion and scarring. At the same time, the fluidity and temperature of the molten metal will decrease greatly, causing casting defects such as cold separation and insufficient pouring.Therefore, the casting time severely affects the quality of castings.
At present, there is no perfect calculation formula to determine the proper pouring time. Empirical formula is often used to determine the pouring time in production.For cast iron castings of complex shape with a weight less than 450kg, the pouring time is calculated according to the formula:
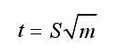
In
T – pouring time (s);
M – pouring weight (kg);
The S-coefficient is determined by the thickness of the casting.
The pouring time t of ductile iron castings can be calculated according to the formula, and then the pouring time of ductile iron can be calculated by reducing the calculated value by 1/3~1/2 as the pouring time of ductile iron.