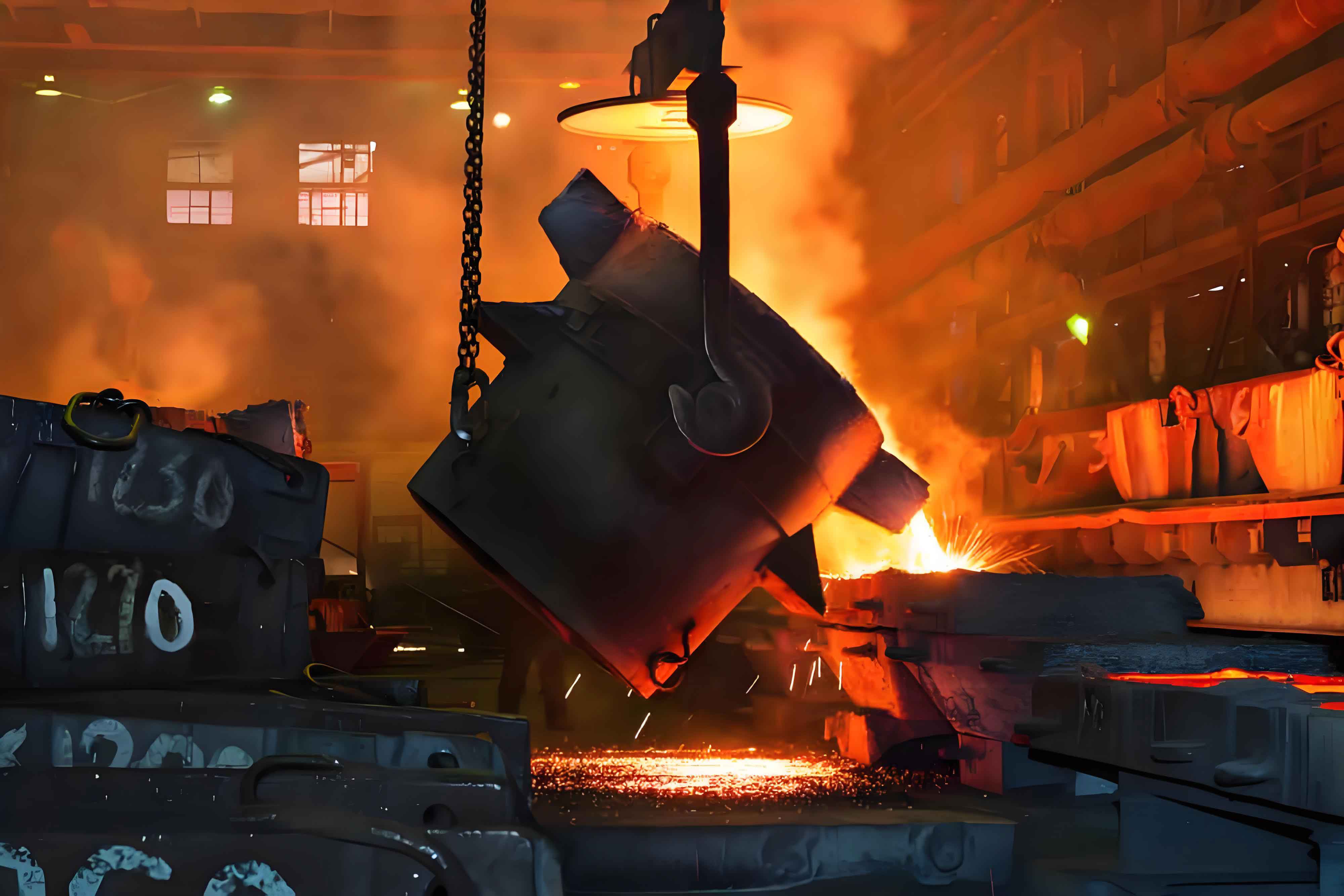
1. Water Jacket Core Breakage in EA113 Cylinder Blocks
1.1 Defect Characteristics
Core fractures predominantly occurred at the bottom center of water jacket ends (wall thickness: 3.5 mm) in grey cast iron EA113 cylinder blocks. This defect severely compromised cooling efficiency, causing scrap rates exceeding 10%.
1.2 Root Cause Analysis
The failure mechanism involves two critical factors:
$$ \sigma_{thermal} = E \cdot \alpha \cdot \Delta T $$
Where:
E = Elastic modulus of quartz sand (72 GPa)
α = Thermal expansion coefficient (12×10⁻⁶/°C)
ΔT = Temperature gradient (1,200°C)
The phase transformation stress from β-quartz to α-quartz at 573°C causes volumetric expansion:
$$ \epsilon_{phase} = \frac{\Delta V}{V_0} = 2.4\% $$
Acid Demand Value (mL) | Production Quantity | Defective Units | Scrap Rate |
---|---|---|---|
8.2 | 422 | 42 | 9.9% |
4.3 | 200 | 4 | 2.0% |
1.3 Corrective Measures
Key improvements for grey cast iron components:
- Implemented high-temperature calcined sand with acid demand value <3 mL
- Established core storage protocol: ≤3 days at RH≥65%
- Optimized equipment maintenance cycle:
$$ t_{maintenance} = \frac{\sum (MTTR + MTBF)}{N_{cycles}} $$
2. Surface Burning-on Defects in EA118 Cylinder Blocks
2.1 Process Parameters
Horizontal pouring process for thin-wall grey cast iron castings (3.5±0.8 mm) with pouring temperature 1,450±10°C.
Parameter | Original | Optimized |
---|---|---|
Sand GFN | 50-100 | 50-140 |
Gas Evolution (mL/g) | 14-17 | 18-22 |
Clay Content | 10% | 12% |
2.2 Thermal Analysis
The critical gas pressure model for metal penetration:
$$ P_c = \frac{4\gamma \cos\theta}{d_p} $$
Where:
γ = Surface tension (1.2 N/m for grey cast iron)
θ = Contact angle (135°)
dₚ = Sand particle diameter (0.212 mm)
2.3 Process Optimization
- Installed sand cooling system:
$$ \Delta T = \frac{0.01m_{water} \cdot L}{c_p \cdot m_{sand}} $$ - Adjusted compactibility-water ratio:
$$ C/W = \begin{cases}
14-16 & T_{ambient} > T_{sand} + 10^{\circ}\text{C} \\
11-13 & \text{Otherwise}
\end{cases} $$
3. Leakage Defects in Cylinder Bore Areas
3.1 Microstructural Analysis
Typical microstructure requirements for grey cast iron cylinder blocks:
$$ \text{Graphite Flake Size} = \frac{\sum (l_i \cdot w_i)}{N} \leq 0.15 \text{mm}^2 $$
Where lᵢ and wᵢ represent length and width of individual graphite flakes.
3.2 Process Improvements
- Modified inoculation practice:
$$ \Delta CE = 0.03\% \cdot t_{inoculation}^{-0.5} $$ - Implemented directional solidification:
$$ G = \frac{T_{pour} – T_{solidus}}{t_{solidification}} \geq 3.5^{\circ}\text{C/cm} $$
Parameter | Before | After |
---|---|---|
Leakage Rate | 7.2% | 1.8% |
Hardness Variation | 35 HB | 18 HB |
4. Integrated Quality Control Model
Developed a comprehensive quality prediction system for grey cast iron production:
$$ QPI = \sum_{i=1}^n w_i \cdot \frac{x_i}{X_{std}} $$
Where:
wᵢ = Weighting factors (process parameters)
xᵢ = Actual measured values
X_std = Standard requirements
Key parameters include sand properties, melt quality, and process stability. This model reduced overall defect rate by 42% in grey cast iron cylinder block production.