1. Introduction
The cylinder head is a crucial component of diesel engines. In the case of the 16V190 cylinder head, it operates under extremely harsh conditions. The high – temperature environment in the combustion chamber, with temperatures reaching up to about 2000 K (around 1700 °C), subjects the cylinder head to intense thermal stress. Additionally, the high – pressure cyclic loads in the combustion chamber demand a high – quality casting with no internal or external defects, especially in areas like the high – pressure side and valve seat holes. The material of the 16V190 cylinder head is RuT300, which has excellent mechanical properties, good thermal fatigue resistance, and high airtightness.
2. Casting Process of 16V190 Cylinder Head
2.1 Sand Molding and Core – Making
The casting process of the 16V190 cylinder head starts with resin – sand machine molding for the overall casting mold. The mold is designed to produce 2 pieces per mold. Some sand cores are made by hand using resin sand, while the water – cavity cores and bolt – hole cores are fabricated through the hot – box 覆膜砂 core – making process. Given the complex internal curved surfaces of the cylinder head, a total of 22 sand cores are used in the process.
Core Type | Making Method |
---|---|
Water – cavity core | Hot – box 覆膜砂 core – making |
Bolt – hole core | Hot – box 覆膜砂 core – making |
Some other cores | Resin – sand hand – making |
2.2 Coating and Drying
Both the mold and the sand cores require coating to improve their surface quality and performance. The mold is coated with a water – based coating by pouring, and then it is dried in a drying furnace at a temperature of 170 °C ± 10 °C for 3.5 – 4 hours. The sand cores are coated using a composite process of an alcohol – based quartz coating and a water – based graphite coating. After the cores are assembled into the mold, the entire assembly is dried again.
2.3 Pouring System
Due to the requirement of rapid and stable filling of the molten iron during casting, a stepped pouring system is adopted. The pouring temperature is strictly controlled within the range of 1380 – 1390 °C, and the pouring time is set between 15 – 20 s. This ensures that the molten iron can evenly fill the mold cavity and form a high – quality casting.
3. Common Casting Defects and Their Causes
3.1 Sand Holes
Sand holes in 16V190 cylinder head castings are unwanted holes found inside or on the surface of the casting after cleaning. The main causes of sand holes are related to improper operations during the mold – assembly and core – setting processes. For example, when the bolt – hole core is not installed properly, is not perpendicular to the bottom surface of the core – setting area, or when the upper mold is not hoisted steadily during the mold – closing process, the bolt – hole core may be broken and fall into the mold cavity. This is difficult to detect, and after pouring, it leads to sand holes in the casting. Another situation is that when the upper water – cavity core and the injector – hole core, which are made of separate sand cores and glued together, have cumulative errors in bonding. If there is floating sand or coating accumulation in the injector – hole core seat, and the core – setting is not in place, combined with poor hoisting stability during mold – closing, the sand core may be broken or crushed, resulting in sand – hole defects.
Potential Reasons for Sand Holes | Impact on Casting |
---|---|
Bolt – hole core installation issues | Sand core fragments in the mold cavity, forming sand holes after pouring |
Cumulative errors in core bonding and floating sand | Core breakage during mold – closing, leading to sand holes |
3.2 Inner – cavity Burrs
Inner – cavity burrs in the 16V190 cylinder head are irregular and non – uniform “thin – iron – sheet – like” substances in the gas and water passages or other parts. There are two main reasons for their formation. Firstly, due to the complex structure of the water – cavity in the cylinder head, the sand cores in the water – cavity are made by the hot – box core – shooting process. However, the coated sand is prone to shrinkage and sinking when heated, resulting in a thin shell layer of the sand core. During natural cooling, the sand core shrinks and generates capillary cracks. When the molten iron is poured, the sand core is affected by the high – temperature thermal radiation of the molten iron and may crack, allowing the molten iron to penetrate into the sand core and form burrs of different degrees. Secondly, because of the complex structure of the water – cavity and the need for the intake and exhaust cores to intersect with the water – cavity core, the water – cavity core is divided into two pieces in the process design. When these two pieces of sand cores are glued together, if the bonding surface does not fit tightly enough, it increases the possibility of molten – iron penetration, thus increasing the probability of inner – cavity burrs.
Reasons for Inner – cavity Burrs | Mechanism of Burr Formation |
---|---|
Shrinkage and cracking of sand core due to heating | Molten iron penetration through cracks in the sand core |
Loose bonding of split water – cavity cores | Molten iron seeping through the bonding gap |
3.3 Misrun
The misrun defect in 16V190 cylinder head castings is mainly caused by the overflow of molten iron at the parting surface during pouring, that is, leakage of the mold. In addition, factors such as the purity of the molten iron, the pouring temperature, the correct placement of the filter, and the leakage of molten iron through air holes also have an impact. If the molten iron leaks from the parting surface, it cannot fully fill the mold cavity, resulting in an incomplete casting. Poor – quality molten iron with impurities, low pouring temperature, incorrect placement of the filter that blocks the flow of molten iron, or leakage of molten iron through air holes can all lead to this defect.
Factors Affecting Misrun | How They Cause Misrun |
---|---|
Molten – iron leakage at the parting surface | Incomplete filling of the mold cavity |
Impurities in molten iron | Hindered flow of molten iron |
Low pouring temperature | Solidification before full filling |
Incorrect filter placement | Blockage of molten – iron flow |
Leakage through air holes | Reduced molten – iron volume for filling |
3.4 Gas Holes
Gas holes in 16V190 cylinder head castings are mainly caused by the use of resin – self – hardening sand for molding and core – making. The resin and curing agent in the molding sand generate a large amount of gas under the action of high – temperature molten iron during pouring. If these gases cannot be smoothly discharged from the mold during the pouring process and are trapped inside the casting, they will form gas holes after the casting cools and solidifies. These gas holes are mostly invasive gas holes.
Gas – hole – forming Substances | How Gas Holes Are Formed |
---|---|
Resin and curing agent in molding sand | Gas generation under high – temperature, trapped in the casting during solidification |
4. Improvement Measures for Casting Defects
4.1 Measures for Sand – hole Defects
- Use of Core – setting Fixtures: Special core – setting fixtures, such as core – setting gauges, are made according to the actual situation. For the 16V190 cylinder head, considering its core – assembly process, height – checking gauges are made for the mating surfaces in the height direction of the sand cores. This helps to reduce the cumulative errors during core – setting, preventing the upper mold from crushing the bolt – hole core and other sand cores during mold – closing.
- Inspection of Inner – cavity Wall Thickness: Inner – cavity wall – thickness calipers and 6 – mm soft – leather wires are used for inspection. Regular – shaped wall – thickness dimensions are measured with calipers, while for irregular – shaped curves like those in the air passages, soft – leather wires are used as inspection feeler gauges. By ensuring the minimum wall – thickness dimensions of the curved parts, the core – setting of the inner – cavity – related sand cores can be guaranteed to be in place, preventing the sand cores from being damaged during mold – closing.
- Quality – awareness Training: Regular quality – awareness training is carried out for workers. During core – setting, the floating sand and accumulated coating in the core seat are carefully cleaned one by one. After core – setting, the perpendicularity of the bolt – hole core is checked one by one. During mold – closing, a dedicated person is assigned to check whether the bolt – hole core collides with the upper – mold core seat, ensuring a smooth mold – closing process and preventing the sand cores from being crushed.
4.2 Measures for Inner – cavity Burr Defect
- Improving Sand – core Quality: To prevent the formation of inner – cavity burrs, the quality of the water – cavity sand core is enhanced. Process parameters such as the core – shooting temperature and pressure – holding time are strictly controlled to ensure that the shell – layer thickness of the sand core is greater than 5 mm. Before mold – assembly, the sand core is immersed and coated twice with an alcohol – based zircon – powder coating to improve the surface density, refractoriness, and strength of the sand core.
- Controlling Core – setting Details: The quality control of water – cavity core – setting is strengthened. Before core – setting, the upper and lower pieces of the water – cavity sand core are trial – fitted to check the mating surface. The mating surfaces of the two pieces of sand cores are appropriately trimmed according to their shapes to make the fit flat and minimize the gap. When installing the upper and lower pieces of the water – cavity core, a layer of foundry adhesive is evenly applied on the mating surface of the lower – piece water – cavity core, avoiding the exhaust groove. Then the upper – piece water – cavity core is put on and slightly pressed to make the adhesive extrude to both sides. The upper – piece core is removed to check the bonding situation, and the excess adhesive is scraped off. For areas where the bonding is not tight enough, the foundry adhesive is used for proper repair, and then the upper – piece sand core is put on again and pressed to ensure a tight fit between the two sand cores and reduce the possibility of molten – iron penetration.
4.3 Measures for Misrun Defects
- Preventing Mold Leakage: During the molding process, the condition of the sand box and other tooling is carefully inspected. Defective or loose sand boxes are not used to prevent the overall sinking of the mold. Before mold – closing, a φ4 – mm sealing clay strip is placed along the perimeter of the lower – mold parting surface, avoiding the pouring channel. When clamping the mold with box clamps, they are tightened diagonally at the same time to ensure uniform stress on the mold.
- Controlling Molten – iron and Pouring Quality: The quality of the molten iron and the pouring process is strictly controlled. During pouring, the quality of the original molten iron is ensured by skimming and removing slag. The slag – blocking operation during pouring is strengthened. The pouring ladle spout should be close to the pouring cup, and the pouring cup should be quickly filled and kept full to avoid turbulent flow, eddy current, and splashing during filling. Intermittent pouring, which may cause slag to block the filter holes, is also avoided.
- Correct Placement of Ceramic Filters: In the process design, a ceramic filter is placed at the connection between the straight pouring channel and the horizontal pouring channel to block slag. When placing the ceramic filter, it is necessary to ensure that the inflow hole faces the pouring cup, allowing the molten iron to flow smoothly through the filter holes and into the mold.
- Controlling Ventilation Holes: The ventilation holes and air holes are kept unobstructed, and proper post – treatment is carried out. The air passages in the mold and sand cores are ensured to be unobstructed, and the ventilation holes of the sand cores are made properly during mold – assembly. The ventilation holes are preferably reserved in the upper mold, and proper sealing is done around the ventilation holes to prevent molten iron from entering and causing leakage.
- Controlling Pouring Temperature: During the pouring of the cylinder head, the initial pouring temperature is controlled at the upper limit of the process (1390 °C). The molten iron in the pouring ladle is properly insulated with insulation materials. The pouring process should be carried out smoothly, orderly, and quickly to ensure that the pouring temperature at the later stage of pouring is within the required process range.
4.4 Measures for Gas – hole Defects
- Optimizing the Pouring System: The pouring system is optimized in the process design. The design of the inner pouring channel should ensure the smooth filling of the molten iron and the smooth floating of the gas. The positions and numbers of the risers and air holes are designed reasonably to facilitate the smooth discharge of the gas in the mold from the cavity.
- Enhancing Sand – core Ventilation: The ventilation of the sand core is enhanced. Before the sand core is coated, the air – passage holes are blocked to prevent the coating from blocking the air passages. After coating, all the air – passage holes in the sand – core heads and the blocked air – passage holes are opened, and they are extended to the thick part of the sand core. Some broken sand in the sand core is poured out to ensure the smoothness of the sand – core air passages.
- Ensuring Mold Ventilation: Before core – setting, according to the position of the sand – core head in the mold cavity, ventilation holes are drilled from the outside of the mold to the core seat. A foundry adhesive is applied in the core seat to block the gaps between the core heads. The foundry adhesive is applied around the ventilation holes, avoiding the holes, to prevent the molten iron from entering the ventilation channels and blocking the air passages during pouring, ensuring that the gas generated in the sand core can be smoothly discharged from the mold.
5. Effect of Improvement Measures
After implementing the above – mentioned improvement measures, the production of 16V190 cylinder head castings has achieved remarkable results. The defect rate of cylinder head castings has dropped significantly, from the original 3.8% to 0.8%. This shows that these improvement measures are effective in preventing sand holes, inner – cavity burrs, misrun, and gas – hole defects in 16V190 cylinder head castings.
Defect Type | Before Improvement | After Improvement |
---|---|---|
Sand holes | Relatively high occurrence rate | Significantly reduced |
Inner – cavity burrs | Common in castings | Rarely seen |
Misrun | A certain proportion of defective products | Almost eliminated |
Gas holes | Noticeable in castings | Greatly decreased |
6. Conclusion
The casting process of 16V190 cylinder heads is complex, and various casting defects are likely to occur. By analyzing the causes of typical casting defects such as sand holes, inner – cavity burrs, misrun, and gas holes, and taking corresponding improvement measures, the quality of cylinder head castings can be effectively improved. In the casting production of cylinder heads, strict control of the details of the casting process, reasonable design and improvement of the casting process, standardization of on – site operations, and the implementation of relevant measures are crucial for reducing the scrap rate of castings, improving production efficiency, and reducing production costs.
7. Future Research Directions
Although the current improvement measures have achieved good results, there is still room for further improvement. Future research can focus on the following aspects: exploring new sand – molding materials and core – making technologies to further reduce the generation of casting defects; using advanced simulation software to optimize the casting process before production, predicting potential defect areas in advance, and making more targeted improvements; and studying the influence of different heat – treatment processes on the internal quality of cylinder head castings to improve the overall performance of the castings.
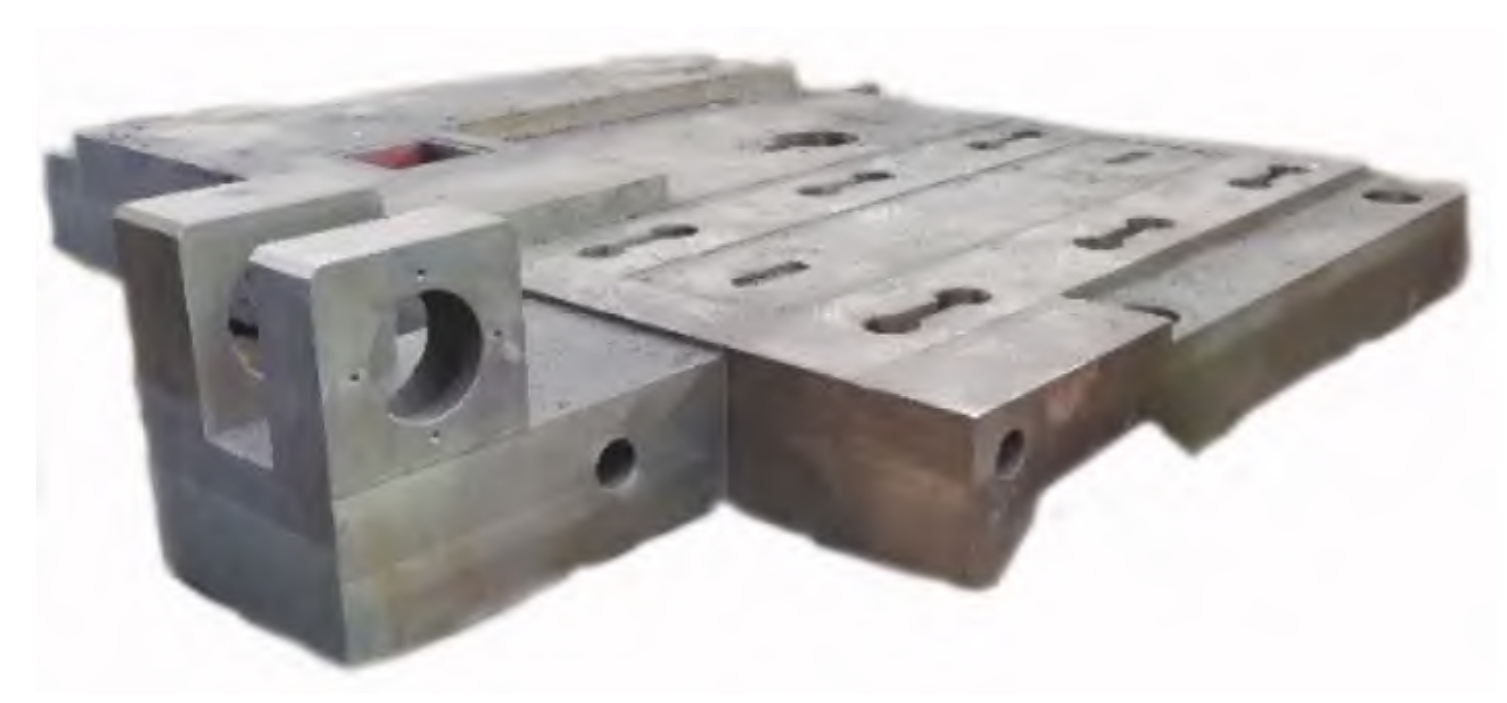