The defect analysis of nodular iron crankshaft in the actual production process can be divided into many defects, such as insufficient pouring, shrinkage cavity, porosity, inclusion, etc. for the reduction and control of these defects, the specific links in the casting process can be adjusted, so as to reduce or even overcome the casting defects.
1. Sand inclusion and its control
Due to the influence of many factors such as spheroidizing agent and sand, there are impurities on the surface or inside of the casting during the wet sand mold casting of nodular iron crankshaft, as shown in Figure 2 [3]. The surface of the casting shows obvious sand hole defects due to sand inclusion. Once such defects occur, the subsequent cleaning and repair work of the crankshaft is increased, making the production process more complicated. In order to better reduce the impurities in the nodular iron crankshaft, Control can be achieved from two aspects:
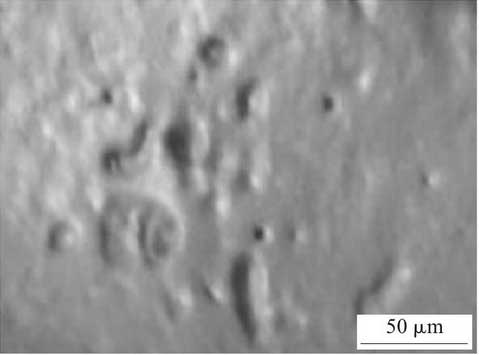
(1) Add filter screen at the end of pouring, as shown in the figure, to reduce impurities brought by one pouring.
(2) The second pouring can control the quality of the sand mold, strictly control the water content of the sand, keep the temperature of the sand the same, ensure that the sand mold of each part of the cavity has a certain degree of compactness, and reduce the occurrence of sand inclusion defects in the second pouring.
2. Porosity and other defects and their control
The blowhole defects of nodular iron crankshaft castings are mainly due to the holes formed by nitrogen bubbles trapped in the metal during the solidification process of the molten metal. As shown in Figure 3, the blowhole defects reduce the effective impact area of the crankshaft and the relative concentration of stress to reduce the mechanical strength and fatigue resistance of the crankshaft. Therefore, for blowholes and other defects, on the one hand, the introduction of gas source should be reduced, On the other hand, the position of casting wall thickness is chosen to add vent hole, which can reduce the blowhole defect of nodular iron crankshaft.
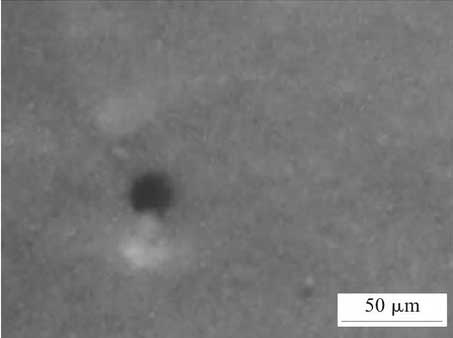
3. Shrinkage cavity, porosity and other defects and their control
After the molten metal enters into the wet sand mold, the heat transfer direction and strength in the sand mold will induce the crankshaft to produce shrinkage cavity defects, as shown in Figure 4. In the casting production, the shrinkage porosity of nodular iron crankshaft is mainly caused by hot spot. For the control of the defect, cold iron can be placed outside the hot spot for feeding control.
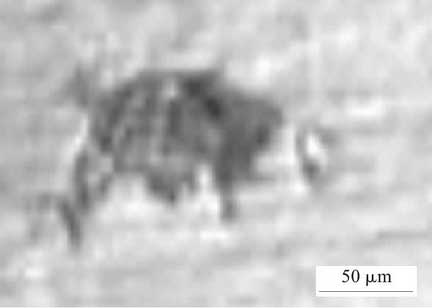
In general, the following control principles are adopted for the casting defects of multiple types of nodular iron crankshaft:
(1) In order to improve the rigidity of the mold properly, the rigid mold can be used for the larger nodular iron crankshaft. In addition, it is necessary to reduce the yield of the mold properly. Through the reaction of the graphite expansion force, the liquid metal can flow evenly, and then the casting can be effectively fed.
(2) The carbon equivalent is 4.2% ~ 4.6%, the carbon content is 3.6% ~ 3.9%, and the silicon content is 1.8% ~ 2.2%.
(3) The spheroidizing treatment of nodular iron adopts RE Mg alloy spheroidizing agent to reduce mg residue.
(4) Reasonable choice of riser, cold iron and pouring system. Cause sequential solidification and feed with riser.