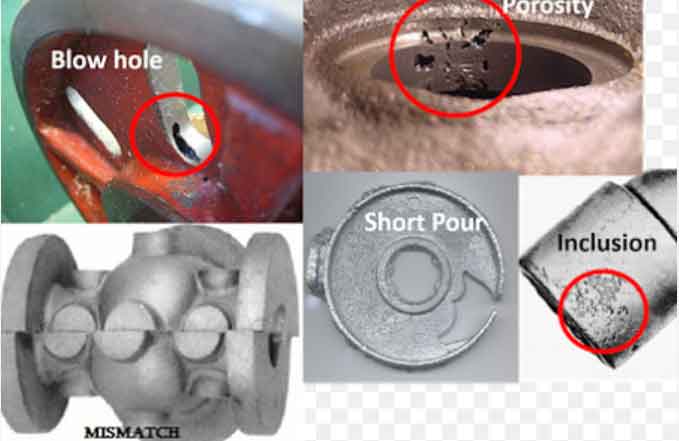
Casting defects can pose significant challenges in the manufacturing process, affecting the quality and performance of castings. However, these defects also provide valuable lessons and opportunities for continuous improvement. By analyzing the root causes of defects, implementing corrective measures, and fostering a culture of continuous improvement, manufacturers can enhance their manufacturing processes and minimize casting defects. This article explores the lessons learned from casting defects and the importance of continuous improvement in manufacturing.
- Defect Analysis and Root Cause Identification:
- Conduct a thorough analysis of casting defects to identify their root causes. This involves examining process parameters, material properties, mold and core design, and other factors contributing to the defect. By understanding the root causes, manufacturers can implement targeted solutions to prevent their recurrence.
- Data Collection and Documentation:
- Collect comprehensive data on casting defects, including defect type, frequency, and associated process parameters. Maintain detailed documentation of defect analysis, corrective actions taken, and their outcomes. This data serves as a valuable resource for future reference and continuous improvement efforts.
- Process Optimization:
- Utilize the insights gained from defect analysis to optimize the casting process. Make informed adjustments to process parameters, such as pouring temperature, cooling rates, mold design, and gating system, to minimize the risk of defects. Continuously monitor and evaluate the impact of process changes to ensure continuous improvement.
- Quality Control and Inspection:
- Implement robust quality control measures at each stage of the manufacturing process. Conduct regular inspections, dimensional measurements, and non-destructive testing to detect and eliminate defects. Emphasize the importance of inspection and provide training to personnel involved in quality control.
- Training and Skill Development:
- Provide ongoing training and skill development programs for operators, technicians, and engineers involved in the casting process. Enhance their knowledge of defect recognition, process optimization techniques, and problem-solving skills. Empower employees to actively contribute to defect prevention and continuous improvement.
- Collaborative Problem-Solving:
- Foster a collaborative environment where cross-functional teams can work together to address casting defects. Encourage open communication, knowledge sharing, and collaboration between design engineers, manufacturing personnel, and quality control experts. Leverage collective expertise to identify innovative solutions and drive continuous improvement.
- Supplier Collaboration:
- Collaborate closely with material suppliers, tooling manufacturers, and equipment suppliers to address casting defects. Establish clear communication channels and engage in regular discussions to address any potential issues related to material quality, tooling performance, or equipment reliability. Work together to implement improvements and prevent defects.
- Continuous Learning and Benchmarking:
- Stay updated with the latest advancements in casting technologies, materials, and quality control methods. Engage in continuous learning through industry conferences, workshops, and research publications. Benchmark against industry best practices to identify areas for improvement and incorporate new techniques into the manufacturing process.
- Process Monitoring and Feedback:
- Implement real-time process monitoring systems to track critical parameters and detect deviations. Use data analytics and visualization tools to analyze process performance and identify trends or patterns related to defects. Establish a feedback loop to provide timely feedback to operators and enable them to take corrective actions promptly.
- Embrace a Culture of Continuous Improvement:
- Instill a culture of continuous improvement throughout the organization. Encourage employees to actively participate in defect prevention initiatives, share their insights, and propose process improvements. Recognize and reward contributions to continuous improvement, fostering a sense of ownership and accountability.
Casting defects in manufacturing serve as valuable lessons for improving processes and enhancing product quality. By analyzing defects, implementing corrective actions, fostering a culture of continuous improvement, and collaborating with suppliers and employees, manufacturers can minimize casting defects and optimize their manufacturing processes. Continuous improvement ensures that lessons learned from past defects are applied to prevent future occurrences, leading to increased efficiency, reduced costs, and improved customer satisfaction.