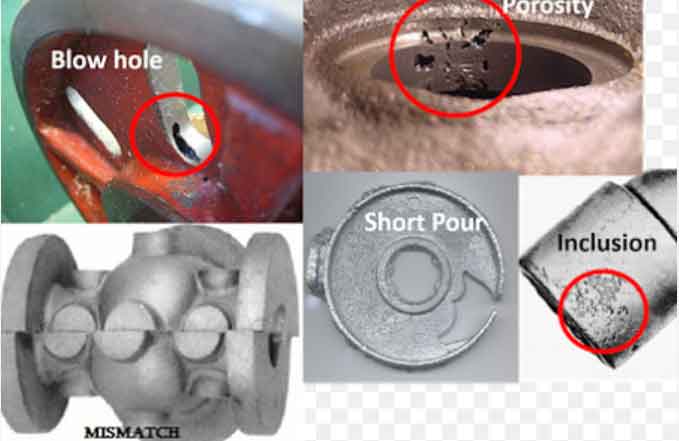
The metal casting industry continually strives to improve casting quality and minimize defects through a process of learning and continuous improvement. Lessons learned from past experiences and a commitment to ongoing refinement play a vital role in enhancing casting processes. This article highlights the importance of continuous improvement in metal casting, focusing on the lessons learned from casting defects and strategies for achieving higher quality and efficiency.
1.Defect Analysis and Root Cause Identification:
a) Comprehensive Defect Documentation:
Thoroughly document and categorize casting defects, including their types, locations, and potential causes. Create a defect database for future reference.
b) Root Cause Investigation:
Conduct detailed analyses to identify the underlying factors contributing to casting defects. Utilize tools such as process mapping, failure mode and effects analysis (FMEA), and statistical analysis to pinpoint root causes.
c) Collaboration and Expertise:
Foster collaboration among design engineers, foundry personnel, metallurgists, and quality control teams to leverage their expertise and gain a comprehensive understanding of defect causation.
2.Continuous Improvement Initiatives:
a) Corrective and Preventive Actions (CAPA):
Implement systematic CAPA processes to address identified root causes and prevent recurrence of casting defects. Monitor the effectiveness of implemented actions and make adjustments as necessary.
b) Process Optimization:
Continuously refine casting processes by analyzing historical defect data and conducting experiments. Optimize process parameters, such as mold design, gating and riser systems, pouring temperature, and solidification time, to improve casting quality.
c) Technology Integration:
Embrace advanced technologies, such as computer-aided design (CAD), casting simulation software, real-time monitoring systems, and non-destructive testing (NDT) techniques, to enhance process control and defect detection capabilities.
3.Employee Training and Skill Development:
a) Continuous Learning:
Provide regular training programs and workshops to enhance the knowledge and skills of casting personnel. Educate them on defect recognition, process optimization techniques, and the latest advancements in casting technology.
b) Cross-Functional Training:
Encourage cross-functional training to develop a deeper understanding of the entire casting process, enabling employees to identify potential defects and contribute to process improvement initiatives.
c) Knowledge Sharing:
Establish platforms for knowledge sharing and open communication between teams. Encourage employees to share their experiences and lessons learned, fostering a culture of continuous improvement.
4.Supplier Management and Quality Control:
a) Supplier Collaboration:
Foster strong partnerships with material suppliers, ensuring a consistent supply of high-quality raw materials. Collaborate on material testing, quality control, and process improvement initiatives.
b) Supplier Qualification and Auditing:
Implement rigorous supplier qualification processes, including audits and inspections, to ensure adherence to quality standards and minimize material-related defects.
c) Quality Control Measures:
Continuously monitor and inspect casting processes at various stages to identify potential defects early on. Implement quality control checkpoints and establish clear acceptance criteria to ensure consistency and reduce variations.
5.Data-Driven Decision Making:
a) Data Collection and Analysis:
Collect and analyze process data, defect data, and quality metrics to identify trends, patterns, and areas for improvement. Utilize statistical analysis tools to make data-driven decisions.
b) Key Performance Indicators (KPIs):
Define and track relevant KPIs, such as defect rate, first-pass yield, and customer satisfaction, to measure the effectiveness of continuous improvement efforts and drive accountability.
c) Benchmarking and Best Practices:
Stay updated with industry trends and best practices. Benchmark against industry leaders and incorporate successful techniques and methodologies into the casting process.
Lessons learned from casting defects and a commitment to continuous improvement are essential for achieving higher quality and efficiency in metal casting. By conducting thorough defect analysis, implementing corrective actions, optimizing processes, investing in employee training, fostering collaboration, managing suppliers effectively, and making data-driven decisions, manufacturers can drive continuous improvement initiatives and reduce casting defects. Embracing a culture of learning, innovation, and openness to change is crucial for the long-term success of metal casting operations.