The product structure includes single-gate blowout preventer and double-gate blowout preventer, and the material is ASTM A487 Grade 4. Taking the single-gate BOP as an example, the outline dimensions of the BOP shell casting are shown in Table 1, the net weight is 3580kg, and the structure of the BOP shell casting is shown in Figure 1.
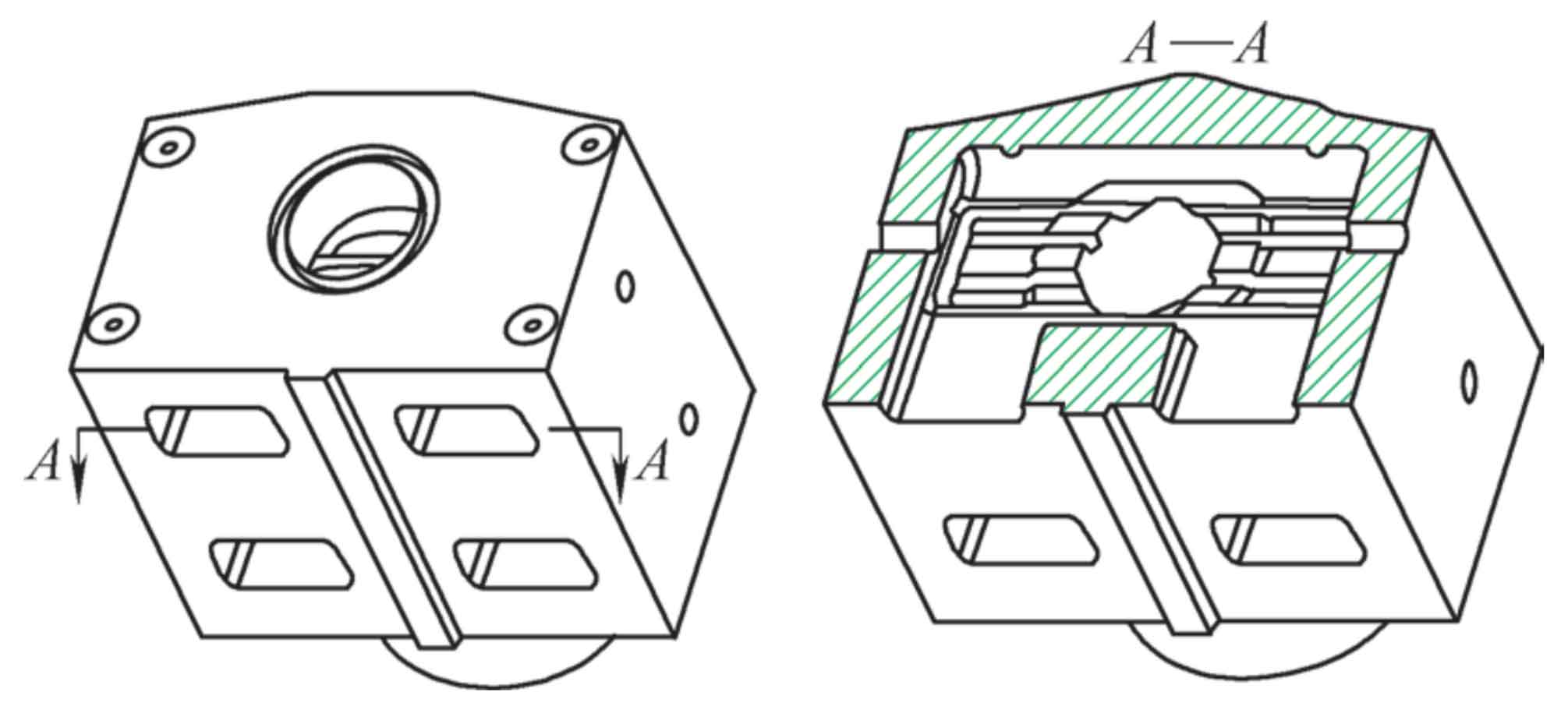
1) The BOP shell casting has small contour, large wall thickness difference and many holes, resulting in the formation of multiple hot spots.
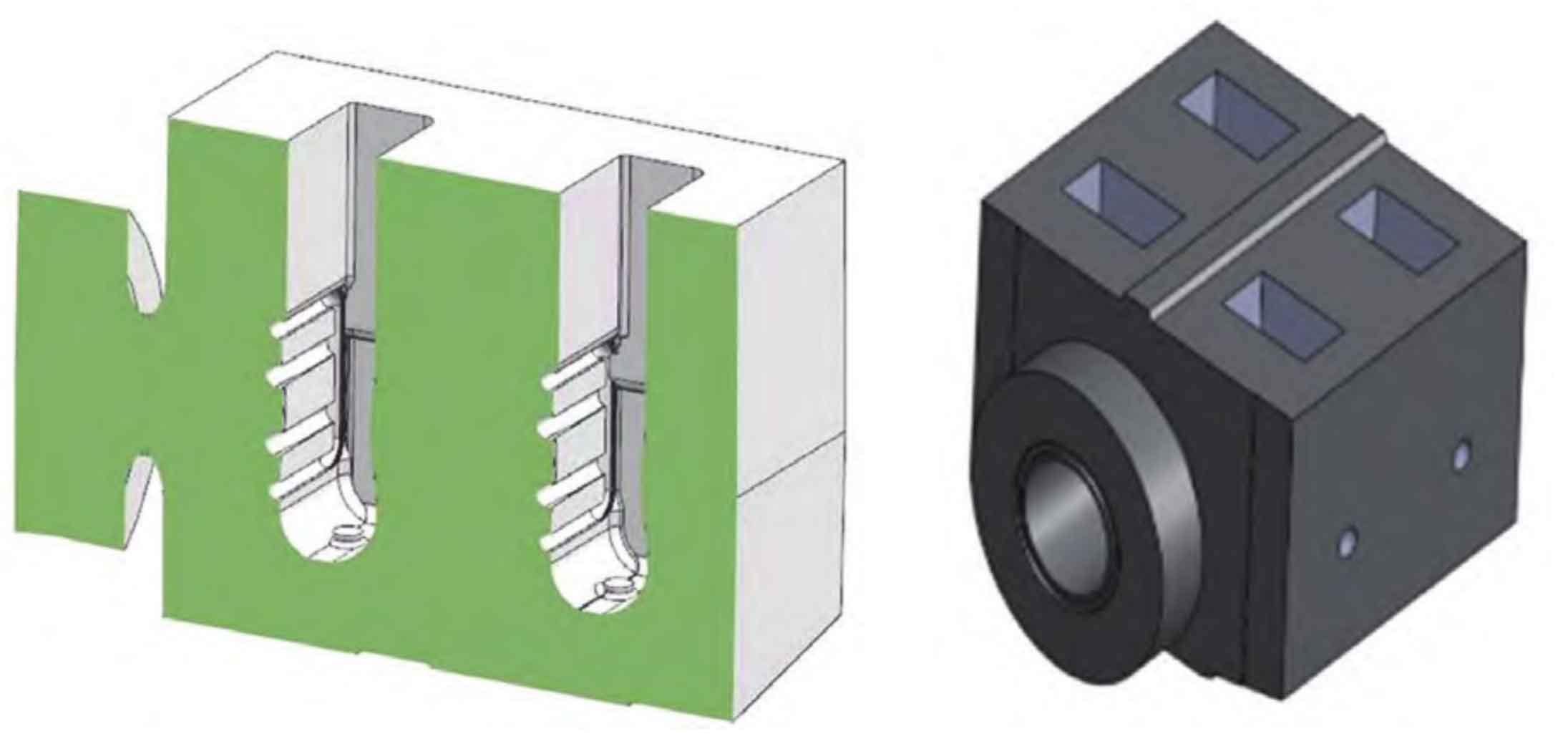
The overall dimension of the product is only 1238mm × 822mm × 876mm, but the maximum wall thickness is 330mm. There are up to 6 intersecting holes in the casting body of the blowout preventer shell. Cross casting hot spots are formed between the holes, and the spacing is less than 200mm. During the casting process, it is easy to produce casting defects such as shrinkage porosity at the large part of the hot spot thickness, segregation of the structure at the root of the riser, which leads to the scrapping of the BOP shell casting. The three-dimensional structure of the product is shown in Figure 2, and the simulation results are shown in Figure 3.
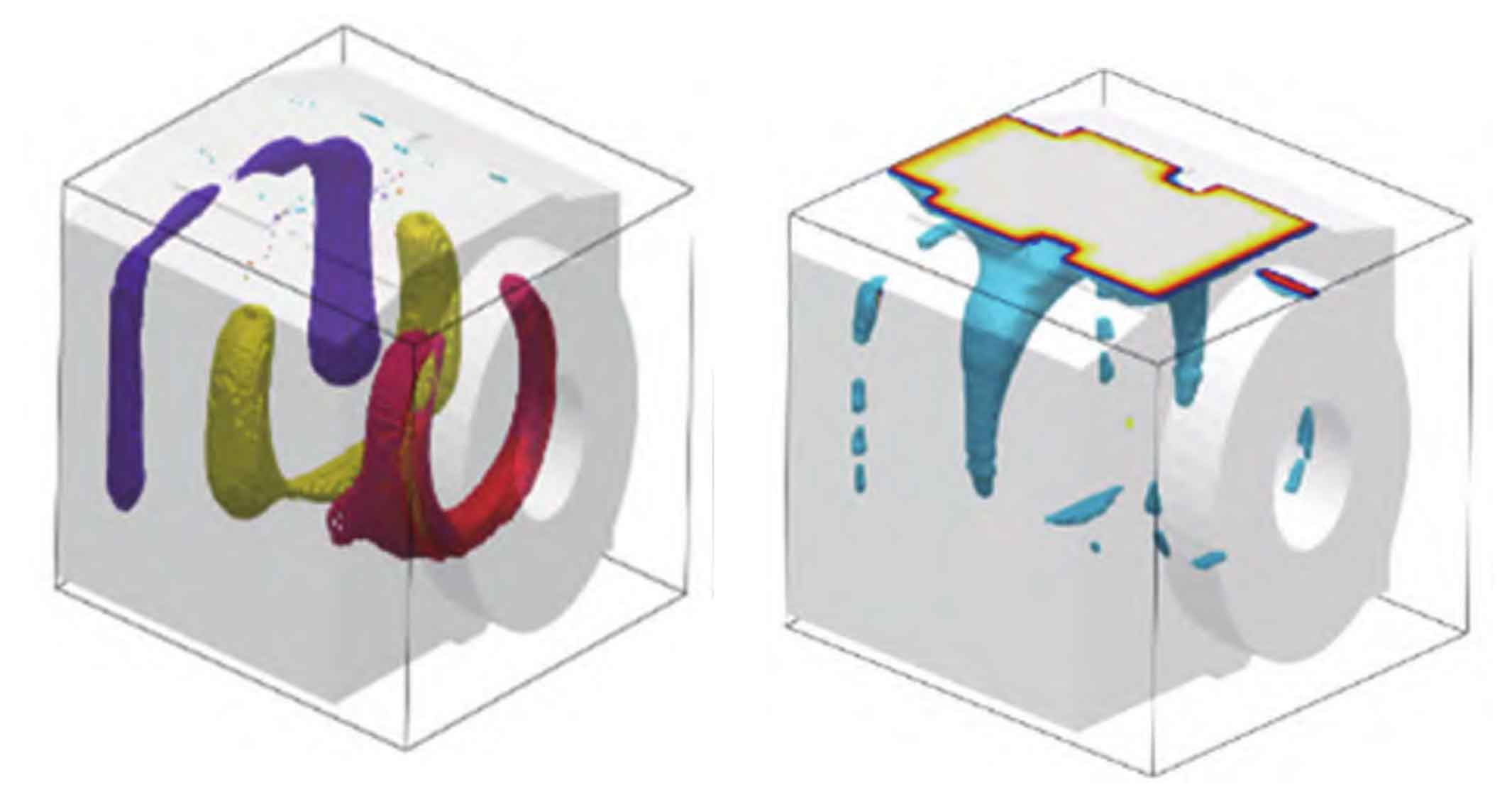
2) The casting of blowout preventer shell has small space, many oil grooves, and is easy to sand and difficult to repair.
The double-gate blowout preventer has two chambers, the inner chamber space is narrow, the maximum space is 167mm, each chamber has four oil grooves, the diameter of the oil groove is 32mm, the narrow space and the complex structure of the oil groove are easy to cause sand sticking inside the cavity when surrounded by 1560 ℃ liquid steel. It can be seen from the simulation that there is a high risk of sand sticking at the inner cavity corner and oil groove under high temperature. If the inner cavity is sand sticking, it cannot be repaired, and the BOP shell casting can only be scrapped.