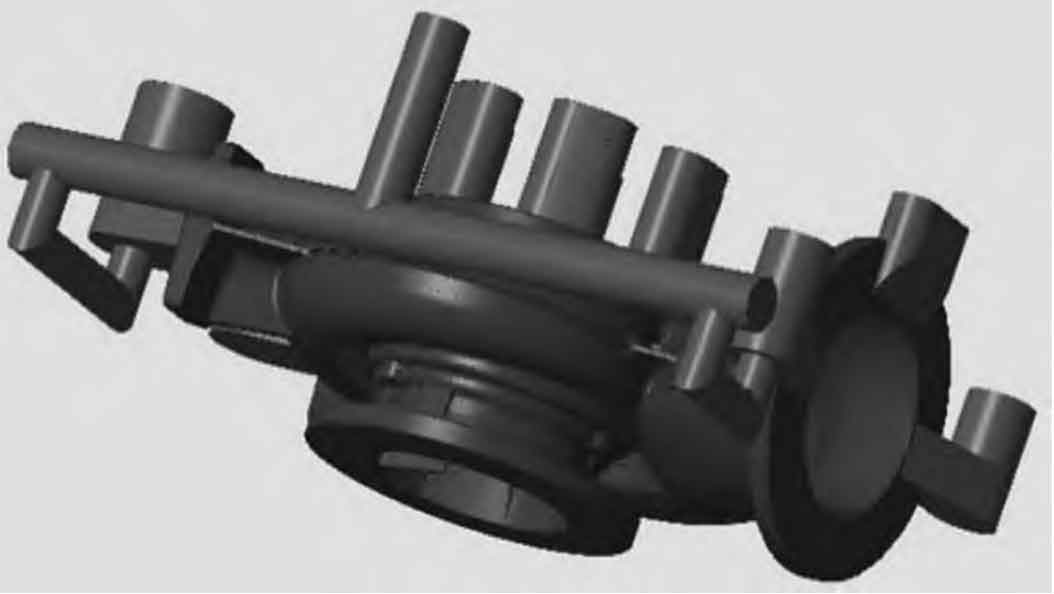
Fig. 1 shows the current mainstream pump casing casting process. The water system is injected at the parting surface height through risers respectively located at the foundation support and the outlet flange. The casting process gating system has the following defects:
(1) The drop of internal water outlet is too large. The molten steel falls and splashes from the parting surface, which scours the cavity seriously, and is easy to produce sand holes, fire, inclusions and other problems.
(2) Water inflow is too concentrated. There are only two dot shaped internal nozzles, which are easy to overheat and increase the risk of cracks.
(3) The molten steel converges at the middle end of the casting. After the molten steel flows for a long time, it will merge at the bottom layer, which is very easy to cause fire and entrainment. In particular, there is also a cold iron at this position.
The casting process and gating system are redesigned as follows:
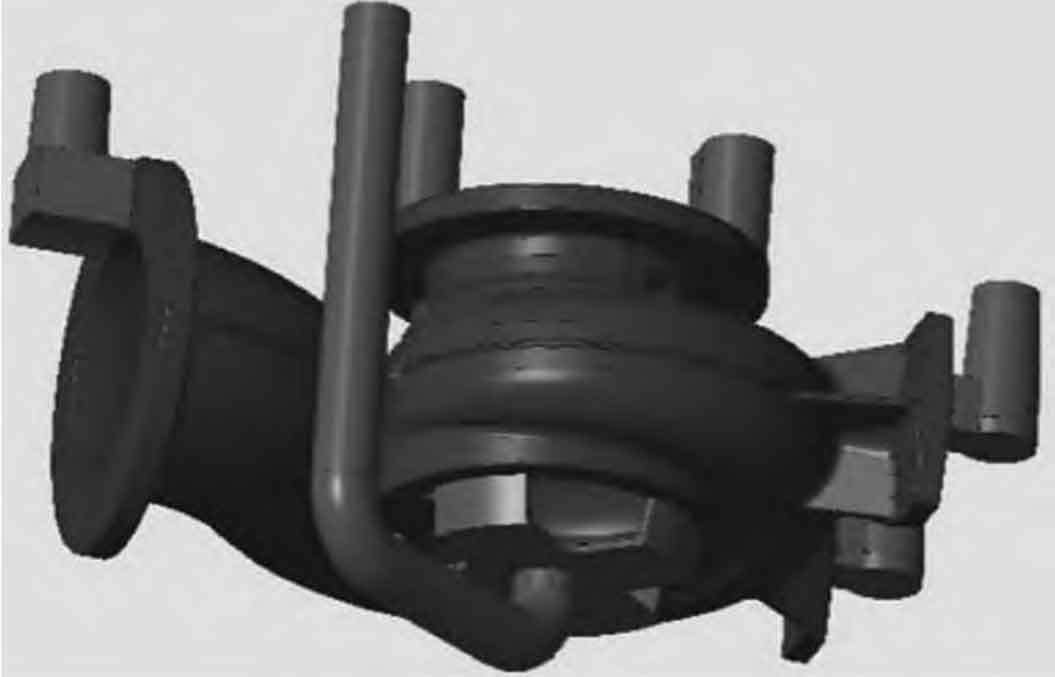
(1) In the open casting process gating system, the straight nozzle adopts ceramic tube bottom return, the horizontal nozzle is used to reduce the speed of molten steel, and the internal nozzle is set inside the connecting flange, which adopts wide flat form to equalize the temperature, as shown in Fig. 2.
(2) Maximum outline dimension of casting: 600mm × 400mm × 300mm, 390kg of cast steel volume and 60mm of wall thickness.
(3) The effective height of the sprue is h = 100mm + 300mm = 380mm.
(4) Casting process pouring time t = (4001 / 2 + 4001 / 3) s ≈ 27.4s, casting process pouring time is 28s.
(5) The casting process and gating system section ratio A1 ∶ A2 ∶ A3 = 1 ∶ 1.1 ∶ 1.2 were selected.
(6) K1 and K2 are calculated as V1 = 0.65, V2 = 0.65 and V3 = 0.60.
V1 is the flow velocity of the sprue; V2 is the flow velocity of the runner; V3 is the flow velocity of the ingate.
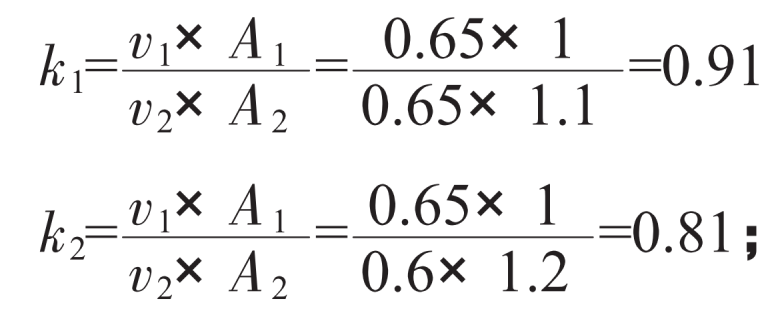
K1 is the pressure ratio of the sprue to the runner; K2 is the pressure ratio between the runner and the ingate.
(7) Calculated tie head (HP)
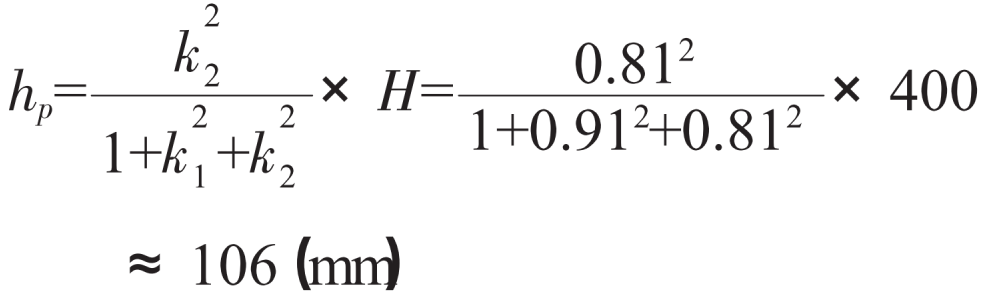
(8) Calculation of cross-sectional area of ingate
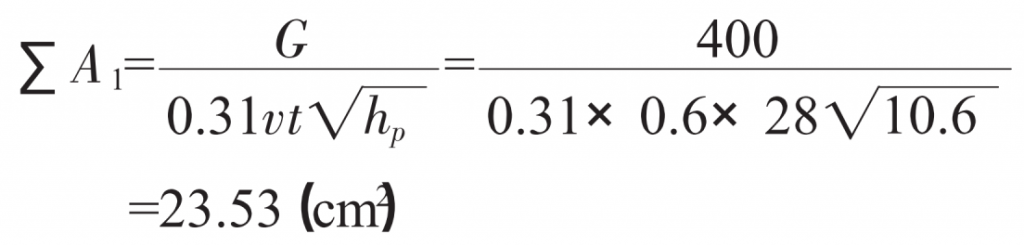
(9) Calculation of cross-sectional area of sprue and runner
As the area of sprue: area of runner: area of ingate is 1 ∶ 1.1 ∶ 1.2, the area of runner is 21.39cm2, the area of runner is 19.6cm2, and the area of ingate is 10mm × 60mm (4 lanes); The transverse runner is taken as ø 200mm × 10mm, and the straight runner adopts ø 50mm ceramic pipe.