Although there are differences in local structure of valve castings of hydrocracking unit, the common structural feature is that the shape is tee tubular, the centerline of each pipeline is on the same plane, the pipe wall is thick and basically uniform, and the material of valve castings is generally corrosion-resistant stainless steel cf8c. Our company has accumulated some experience in the process of developing valve castings, which will be analyzed and described by taking the casting of typical parts dn400-2500lb valve as an example.
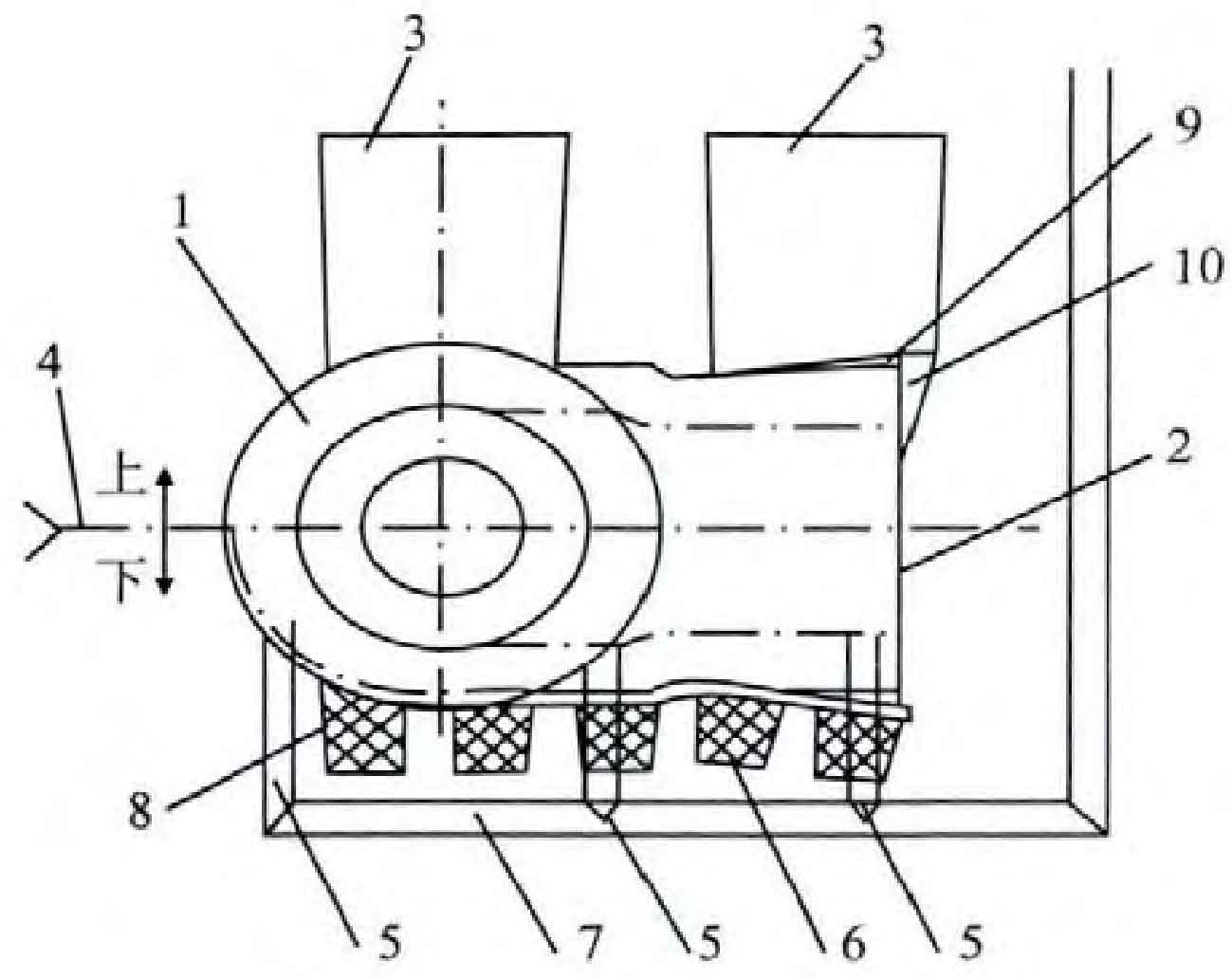
(1) Determination of shrinkage of valve castings. The cf8c material selected for the valve casting is austenitic stainless steel. Under the condition of hindered shrinkage, combined with the structural shape of the casting, the scale of the outer cavity of the valve casting is 2.0% and the scale of the inner cavity is 1.5%.
(2) Parting surface selection. The center line of each pipe is required to be on the same plane for the valve casting, and it is difficult to feed each annular pipe. Therefore, take the plane where the center of the three nozzles is located as the parting surface, and divide the valve casting into upper and lower halves (as shown in the figure).
The parting surface is selected to pass through the center of each nozzle of the valve casting, so that the plane where the parting surface is located is the maximum section of the valve casting, so as to ensure that the axial center line of each nozzle of the valve casting is on the same plane, reduce the use of valve casting sand core, reduce the assembly deviation of the lower core box, avoid the formation of drape joint after pouring, and improve the relative dimensional accuracy and surface quality of each part of the valve casting, The modeling is convenient and simple.
(3) Gating system design. The gating system of valve casting adopts bottom casting gating system. The inner sprue of the bottom injection gating system basically works in the submerged state, and the mold filling is stable, which can avoid splashing and oxidation of liquid metal and the resulting casting defects; No matter how large the gate ratio is, the runner basically works in the full state, which is conducive to slag resistance, and the gas in the mold cavity is easy to be discharged in sequence.