With the improvement of the transportation requirements for water, liquefied petroleum gas, natural gas and other media, the performance requirements for ball valves are becoming higher and higher. In order to improve the performance of ball valves, a set of casting process plan with higher performance must be designed. The produced ball valves should be free of pores, porosity and inclusions. The ball valve shall meet the working environment of water, oil and gas, and the operating temperature range is – 29 ℃~260 ℃. The ball valve shall have good sealing, corrosion resistance, high hardness, strong compression and crack resistance, etc.
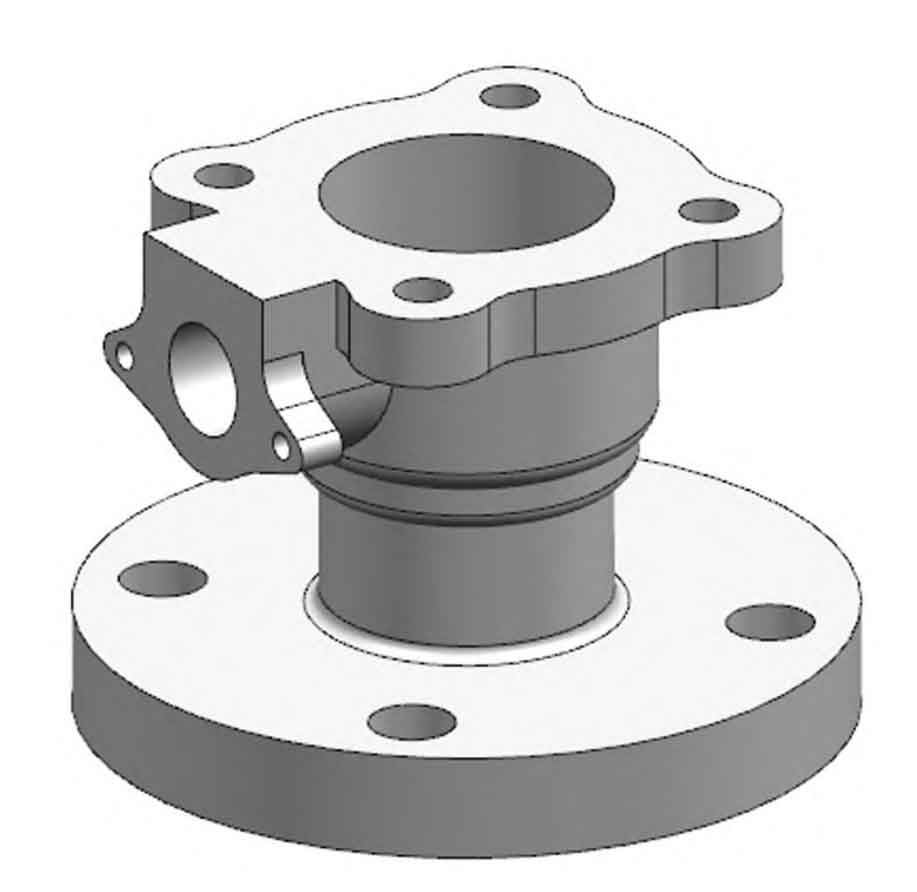
As shown in the figure, it is a three-dimensional solid model of a flanged ball valve. The ball valve is made of 304 stainless steel. It is a medium-sized ball valve with an overall dimension of 145 mm × 160 mm × 220 mm. The upper and lower ends of the ball valve are flat end faces with bolt holes, and the flatness of the upper and lower end faces shall be ensured. The middle part of the ball valve is connected by a stepped cylinder. Its cylindrical surface protrudes from the control structure. Inside the ball valve are holes of different sizes. According to the comprehensive analysis of the ball valve structure, pouring from the bottom or from the side can be selected.
Through the structural analysis of a flanged ball valve, a reasonable sand core combination scheme is designed, and the cold core box method is used for sand core modeling; By analyzing the structure of the ball valve, the pouring position is determined, and a reasonable pouring system is designed; Through the numerical simulation of the casting process by AnyCasting, the solidification sequence of the casting and the position of the defects are determined. The defects are eliminated by adding cold iron, and the adding position of the cold iron is determined through analysis; Again, the casting was analyzed by numerical simulation and the actual casting was tested. There was no defect in the casting, so the casting process plan was feasible.