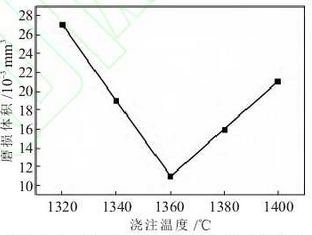
Fig. 1 is the curve of mass added value per unit area of Superalloy samples prepared at different pouring temperatures. It can be seen from the figure that with the pouring temperature increasing from 1320 ℃ to 1400 ℃, the mass increment value per unit area of the new superalloy used for turbocharger turbine of automobile decreases first and then increases, and the high temperature oxidation resistance first increases and then decreases. This is because the smaller the mass increment per unit area, the better the high temperature oxidation resistance of the samples. When the pouring temperature is 1320 ℃, the initial mass of the sample is 21.352 g, the mass per unit area is 606.8 mg / CMM2, and the mass increase value per unit area is 5.9mg/cmm2. At this time, the added value of mass per unit area is the largest, and the high-temperature oxidation resistance is the worst.
With the increase of pouring temperature, the increase value of mass per unit area decreases. When the pouring temperature is increased to 1360 ℃, the mass gain per unit area of the sample reaches the minimum value of 2.1mg/cmm22, which is 64.4% less than that of 1320 ℃. At this time, the high temperature oxidation resistance is the best. However, the higher the pouring temperature is, the better it is. When the pouring temperature is further increased to 1380 ℃ and 1400 ℃, the mass increment value per unit area of the sample increases to 3.6mg/cm2 and 5.1mg/cm2, which is higher than that of 1360 ℃, and the high-temperature oxidation resistance of the samples shows a downward trend.
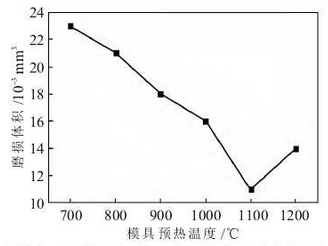
Fig. 2 is the curve of mass increment per unit area of Superalloy samples prepared by different mold preheating temperatures. It can be seen from the figure that with the mold preheating temperature increasing from 700 ℃ to 1200 ℃, the mass increment per unit area of Superalloy samples first decreases and then increases, and the high temperature oxidation resistance first increases and then decreases. When the preheating temperature of the die is 700 ℃, the mass increase value per unit area of the sample is 5.2mg/cmm22, and the mass increase value per unit area is the largest, and the high temperature oxidation resistance is the worst.
With the increase of mold preheating temperature, the mass gain per unit area of the sample decreases. When the preheating temperature of the mould is increased to 1100 ℃, the mass gain per unit area of the sample reaches the minimum value of 2.1mg/cmm22, which is 59.6% less than that of the mold prepared at 700 ℃. The oxidation resistance at high temperature is the best. However, the higher the mold preheating temperature is, the better it is. When the mold preheating temperature is further increased to 1200 ℃, the mass increase value per unit area of the sample is 3.2mg/cm2, which is higher than that when the mold preheating temperature is 1100 ℃, and the high-temperature oxidation resistance of the sample shows a downward trend.
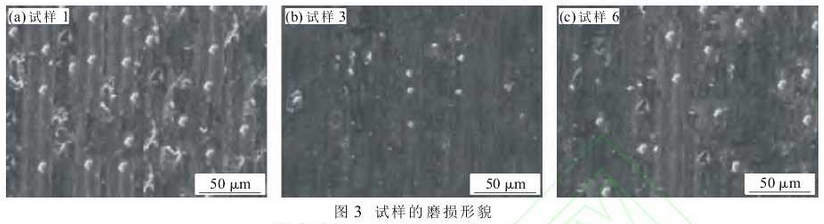
Figure 3 shows the surface morphology of Superalloy samples cast at different pouring temperature and mold preheating temperature after high temperature wear test. According to Fig. 3, it can be clearly seen that after the high temperature wear test, the surface wear degree of sample 1 is the most serious, and the wear mark is large and long, with a few corrosion pits; the wear degree of sample 3 is the least, and the wear mark on the surface is significantly improved, which is short and small, and almost no pit; the wear degree of sample 6 is between sample 1 and sample 3, This is consistent with the results of the wear volume test at high temperature.