Investment casting is a versatile casting process known for its ability to produce complex and intricately detailed components. However, like any casting process, investment casting is susceptible to casting shrinkage, which can pose challenges in achieving dimensional accuracy and quality. In this article, we delve into the challenges and solutions related to casting shrinkage analysis in investment casting.
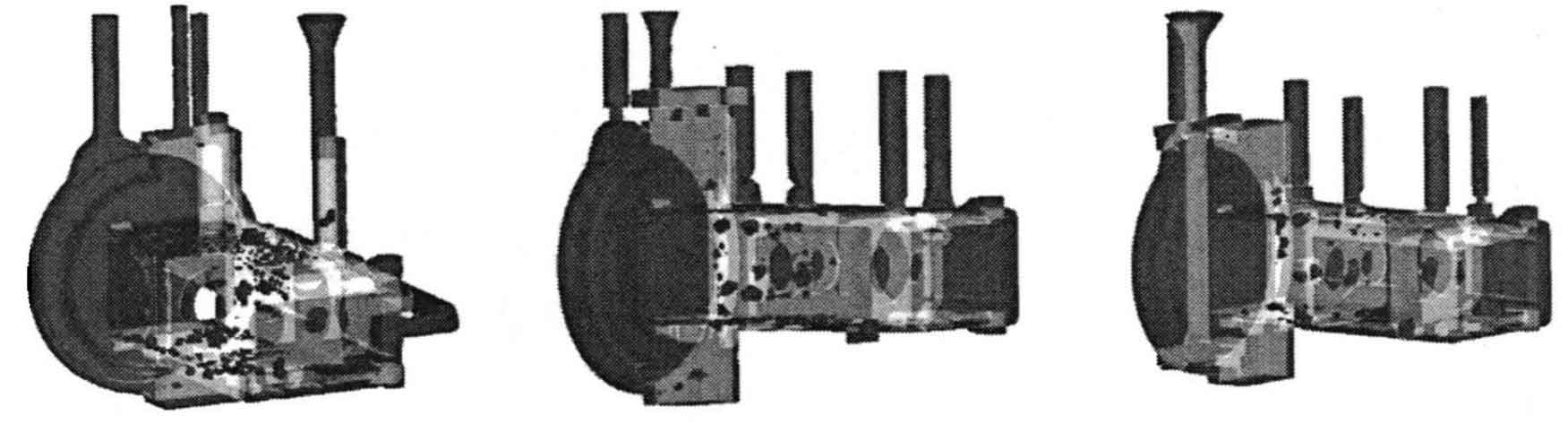
- Predicting Shrinkage: Accurately predicting shrinkage is crucial in investment casting to ensure the final component meets the desired dimensional specifications. However, predicting shrinkage in investment casting can be challenging due to the intricate geometries and complex solidification behavior. The use of advanced simulation software specifically tailored for investment casting can help in predicting shrinkage and identifying potential areas of concern.
- Investment Material Selection: The choice of investment material can significantly impact the casting shrinkage. Different investment materials have varying thermal properties, including thermal expansion and contraction rates, which affect the solidification behavior and subsequent shrinkage of the casting. Careful selection of the investment material based on the specific alloy being cast is necessary to minimize casting shrinkage.
- Wax Pattern and Mold Design: The design of the wax pattern and mold plays a critical role in controlling shrinkage. In investment casting, the wax pattern is created and then surrounded by a ceramic shell mold. Factors such as the wax pattern design, gating system, and mold composition can influence the solidification and cooling behavior, and consequently, the shrinkage of the casting. Optimal design practices, such as appropriate gating and venting, can help control the solidification and minimize shrinkage.
- Casting Process Parameters: Various process parameters, such as mold preheating temperature, casting temperature, and cooling rate, can impact the shrinkage behavior in investment casting. The control and optimization of these process parameters are essential to achieve uniform solidification and minimize shrinkage. Process monitoring and control techniques, such as thermal imaging and temperature sensors, can assist in ensuring the process parameters are properly controlled.
- Post-Casting Heat Treatment: Heat treatment processes, such as stress relieving, annealing, or solution heat treatment, can be employed after the casting process to minimize residual stresses and alleviate shrinkage. Heat treatment can help achieve dimensional stability and improve the mechanical properties of the casting.
- Quality Control and Inspection: Comprehensive quality control measures and inspection techniques are vital in detecting and addressing shrinkage defects. Non-destructive testing methods, such as X-ray, ultrasonic testing, and coordinate measuring machines (CMM), can be used to identify any shrinkage-related defects and ensure the casting meets the required dimensional accuracy.
Investment casting companies and foundries must overcome the challenges associated with casting shrinkage through a combination of design optimization, material selection, process control, and inspection techniques. Close collaboration between design engineers, casting experts, and quality control personnel is necessary to develop effective solutions and ensure the production of high-quality castings with minimal shrinkage defects. By addressing these challenges, investment casting can achieve precise and intricate components that meet the stringent dimensional requirements of various industries.