1. Casting process
Adopt the core assembly and vertical pouring process, pre assemble the base core, water jacket core, airway core and end core (as shown in Figure 1), and then add a top cover core. Among them, the base, top cover, front and rear end cores and airway cores are cold cores, and the water jacket core is made of 100% ceramic sand, pre soaked with water-based paint, and used after drying to reduce gas generation.
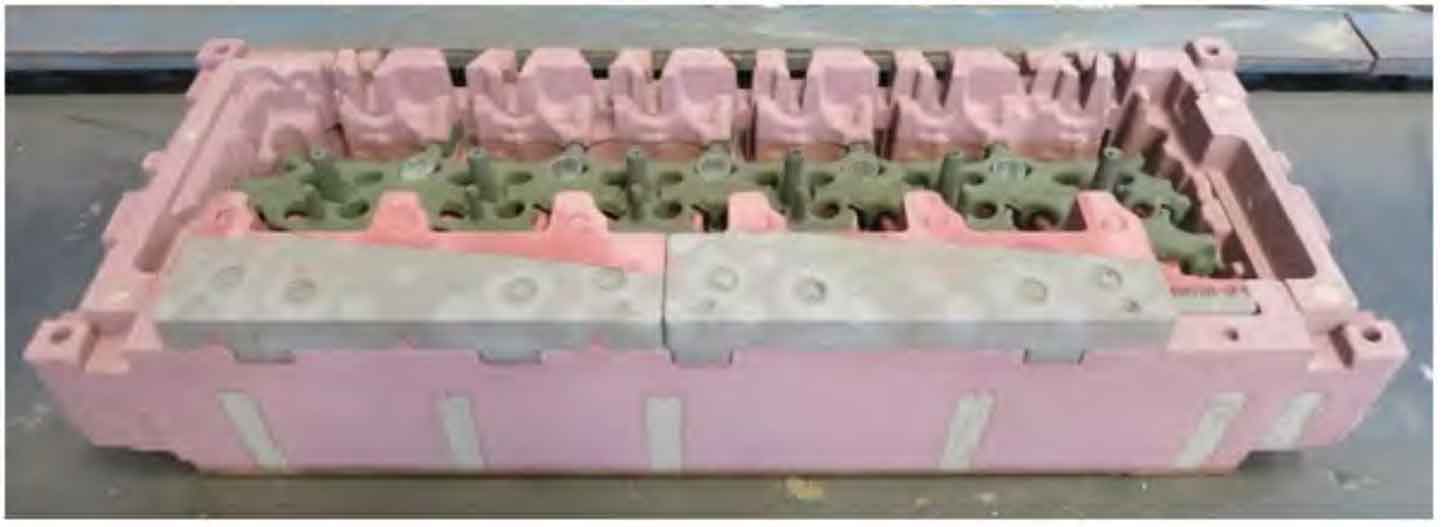
The open gating system is adopted, and the gating ratio is Σ F straight: Σ F horizontal: Σ In F =1:1.2:1.8, the gating system is shown in Figure 2. The gray cast iron cylinder head adopts the overall dip coating process, and the coating uses Fosco 3454 coating.
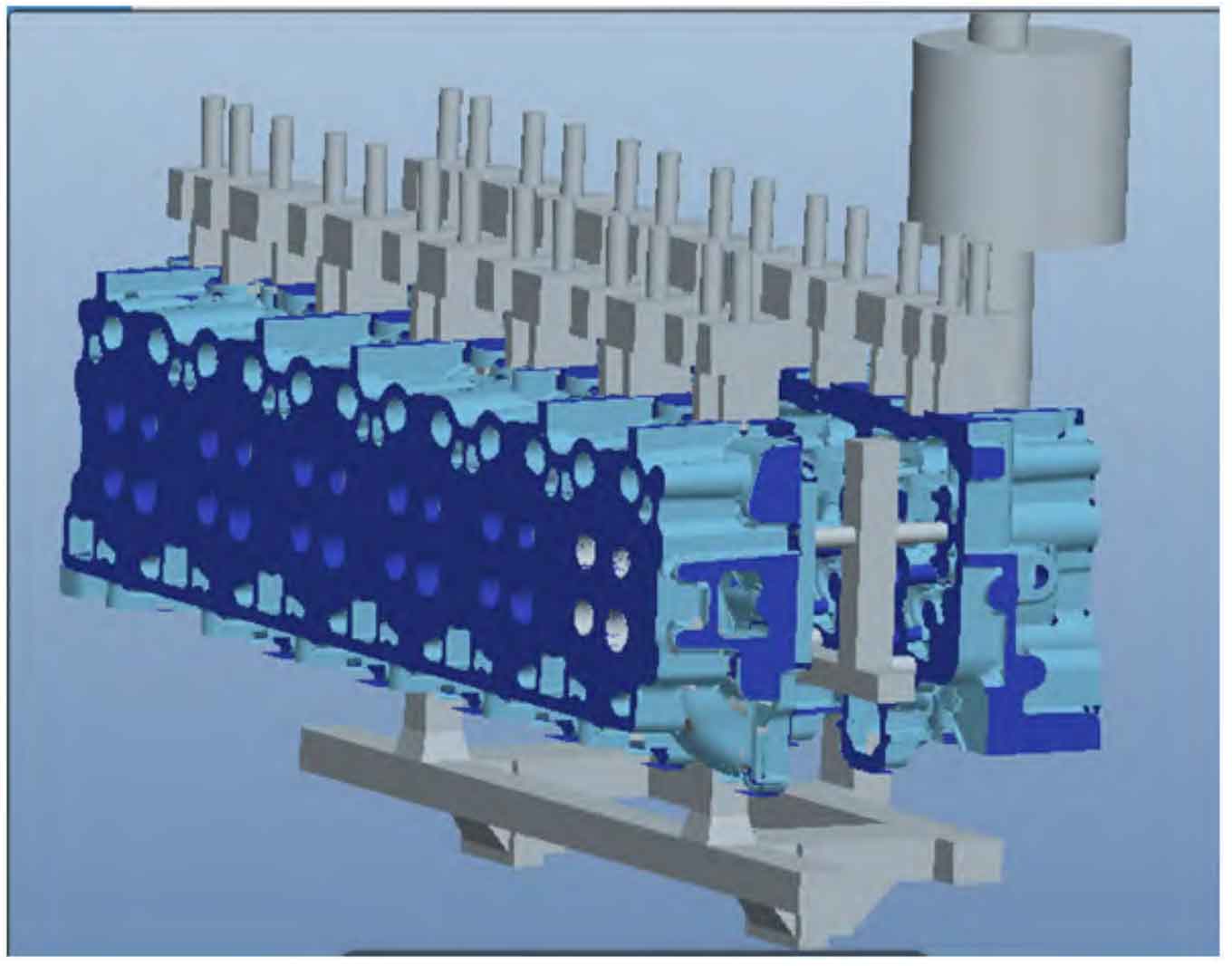
In order to meet the quality requirements that the tensile strength of the bolt hole body of the high-grade gray cast iron cylinder head of large diesel engines is ≥ 270 MPa, low carbon equivalent raw iron liquid, high alloying (Mo, Cr, Cu, Sn) treatment and high inoculation treatment processes are used to ensure that the mechanical properties of the castings meet the requirements. However, the processability of the molten iron is poor, the shrinkage tendency is large, the cylinder head shrinkage problem is serious, and the water leakage rate after processing is as high as 70%, It affects the batch production and development of gray cast iron cylinder head.
2. Existing problems
After dissecting the gray cast iron cylinder head, it is found that the defects of the gray cast iron cylinder head are mainly the shrinkage of the bolt holes, and the casting defects are basically fixed, mainly concentrated in the bolt holes numbered 6.35, 6.39, 6.43 and 6.47 (as shown in Figure 3). The analysis shows that the bolt hole of the high-grade gray cast iron cylinder head of large diesel engine is a non cast hole, and the structure in the area is thick, with a thickness of 30~35 mm. Therefore, it is considered that this part is not fully fed with molten iron during solidification, resulting in shrinkage porosity.
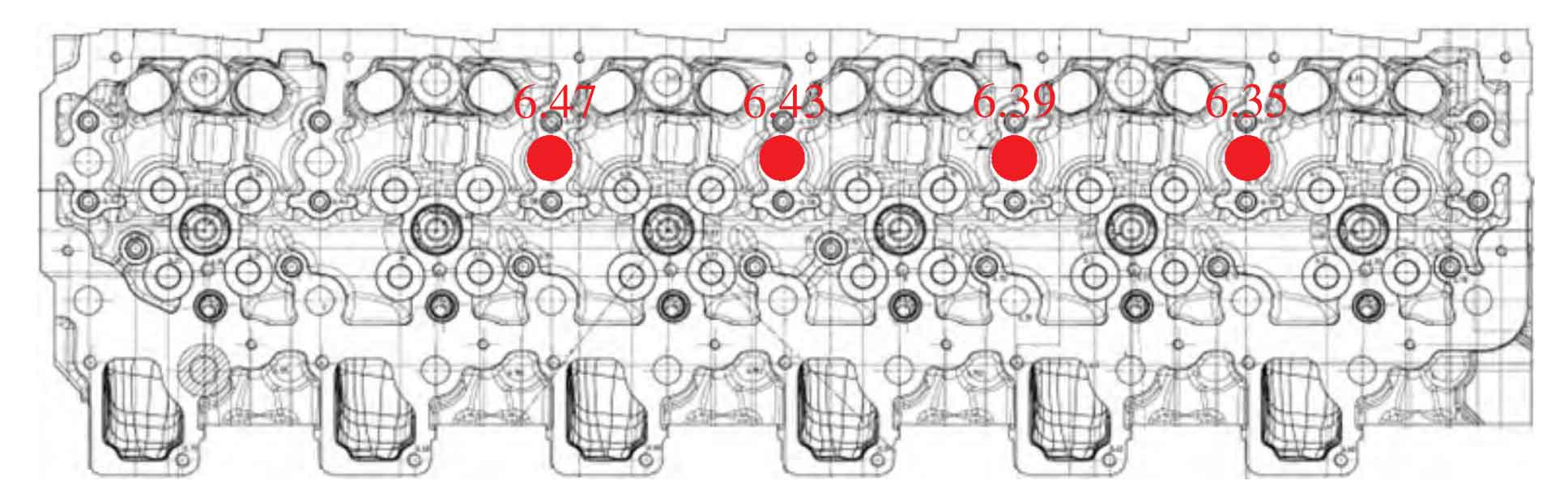