1.Determination of pouring mode
According to the current manufacturers of large-scale normal roll, due to the limitation of equipment, operation level and R & D and design ability, the pouring mode is relatively simple. Due to the lack of liquid steel rotating and rising process in the pouring process, inclusions in the mold cavity and liquid steel can not be effectively floated up, and product defects such as segregation, inclusions, cracks and slag inclusions can not be effectively solved, resulting in product quality Instability, poor durability and low life. The above problems can be effectively solved by using bottom injection mode. However, due to the increase of the amount of molten steel, the original single nozzle pouring method can not meet the requirements of instantaneous flow and erosion resistance. Therefore, considering the equipment conditions, the bridge casting with double ladle and double nozzle can be adopted.
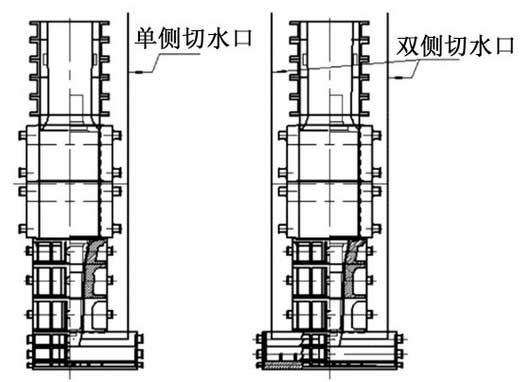
Because of the bridge pouring with large amount of water, there are risks of blocked sprue, backward pouring and steel running. Therefore, the height of the main gate is 400 mm ~ 500 mm higher than that of the auxiliary gate, and the gate box is punched and connected every 800 mm ~ 900 mm, and the iron chain is used to lock the box between the cold type and the riser box. In the pouring process, the secondary gate shall be opened first, and then the main gate shall be opened after the mold cavity enters the molten steel, so as to prevent the steel flow of the secondary gate from blocking and pouring backward.
2. Use of electric heating technology
In order to solve the problem of feeding riser effectively, the SCR heating power supply is used for electric heating and the electric heating parameters are improved.
The working principle of common SCR power supply is similar to that of transformer, which is a step-down transformer. At both ends of the secondary coil are the roller and graphite electrode, which ignite the arc and melt the upper part of the riser end of the roller under the high temperature of the arc to achieve the purpose of feeding.
3. Coating improvement and reasonable selection of molding sand
With the increase of the amount of molten steel, the pouring time and the heat storage increase obviously, which is a test for the fire resistance of the cavity coating. Through consultation with coating manufacturers, the company improved the composition ratio of the coating and developed a special water-based zircon coating with Baume degree greater than 90, which effectively avoided the problem of sand sticking on the lower roller neck, roller body and R part.
For the roller body molding material, the mixture clay sand with chrome ore sand and quartz sand ratio of 1:1 is creatively used to replace the pure zircon clay sand. The number of molding sand mesh is 40-70, which avoids the surface quality problems such as weak chilling effect and longitudinal sand sticking on the surface of the large normal roller body due to the large diameter of the roller body, and greatly reduces the cost.