The steel casting of splay saddle saddle head is the first suspension bridge for both highway and railway in China, and also the key component of the world’s first high-speed railway suspension bridge Wufengshan Yangtze River Bridge. The splay saddle is composed of saddle groove, saddle body and base, which is a cast welded hybrid structure. It is installed on the top of the anchor splay saddle pier, and its main function is to divert the main cable in the horizontal and vertical directions after passing through the splay saddle, and connect it with the anchorage system.
The steel casting of splay saddle head is relatively large, the structure is as shown in the figure, the technical quality requirements are high, the mold manufacturing cycle is long, and the casting process design is difficult. The gross weight of the steel casting is 163 t, and the required molten steel weight is 264 t
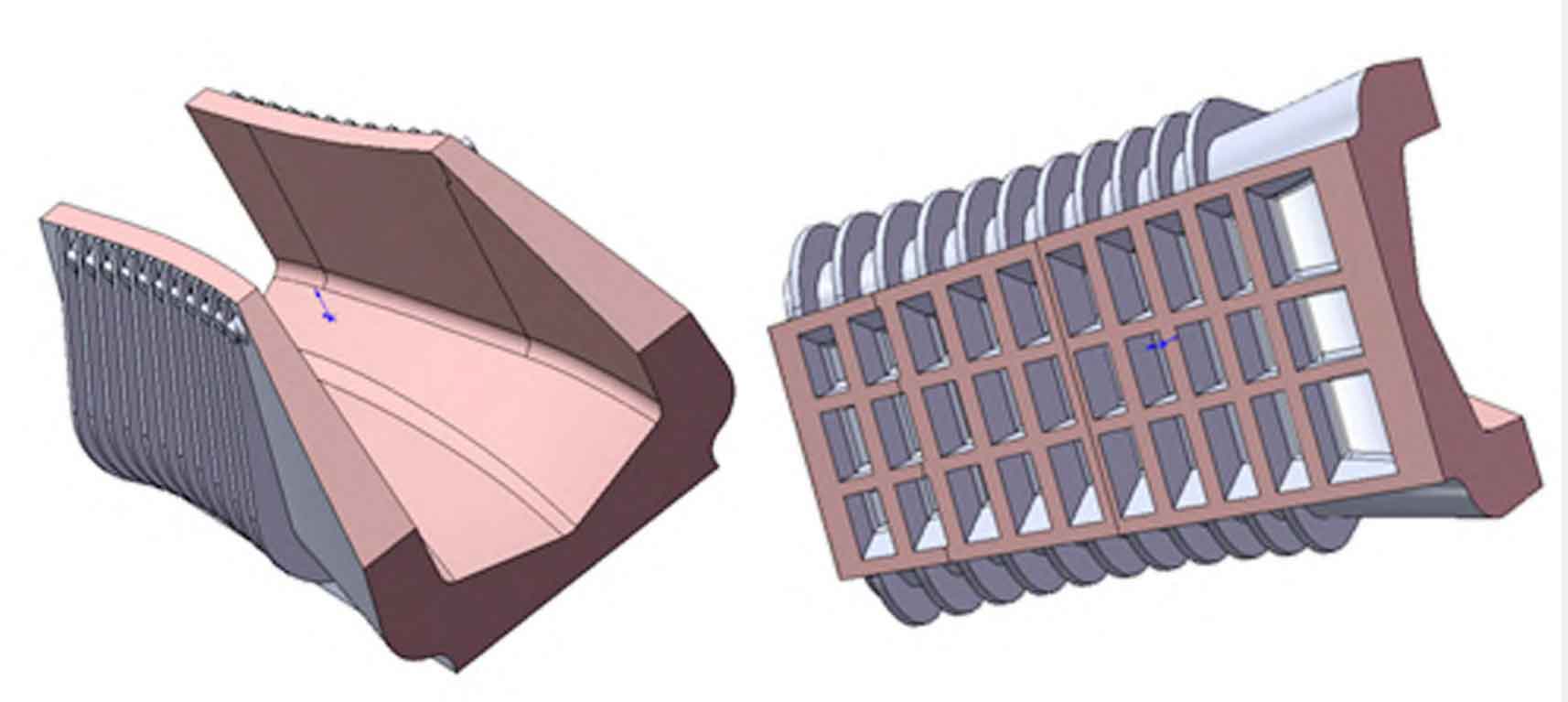
For the large, thick wall and high performance steel casting such as splay saddle head, strict design and calculation must be carried out from riser design, sand core design, allowance and flesh increase design, process parameters, gating system layout, steel casting cleaning and other aspects, and a reasonable casting process must be developed in combination with numerical simulation technology; The quality of steel castings can be guaranteed only by strict process procedures, ensuring the quality of each process and reducing the occurrence of various defects in steel castings during the production process.
The smooth production of splay saddle and saddle head steel castings has accumulated certain experience for the production of large-scale bridge parts in the future:
1) The model shall adopt real sample modeling as far as possible to ensure the rigidity of the core box, so as to ensure the quality and surface finish of the steel casting.
2) For large steel castings, it is necessary to ensure that the feeding channel of molten steel at the far end of the steel castings is unblocked, so as to improve the quality and meet the requirements.
3) For steel castings with high performance requirements, a special heat treatment process must be developed to meet the technical requirements.
4) Due to the different shrinkage of different parts, or the existence of obstacles to shrinkage, in order to ensure that the location and size meet the needs, it is necessary to set different correction amounts.
5) To ensure the surface quality of steel castings and reduce the sand hole and air hole defects of steel castings, it is necessary to ensure that the mold cavity is clean and free of floating sand, and the sand core is vented smoothly.
6) The larger riser or flesh on the steel casting must be cut at a certain temperature after annealing. If necessary, it should be put into the furnace for heat preservation to prevent cracks during cutting.