I. Introduction
In the modern industrial landscape, the manufacturing of high-end equipment plays a crucial role in a country’s economic development and technological prowess. One such remarkable enterprise is the Shared Steel Casting Co., Ltd. (hereinafter referred to as “Shared Steel Casting”). This article will explore in detail the journey of Shared Steel Casting in the production of key components for pumped storage power stations, its technological breakthroughs, and its contributions to the energy sector and the manufacturing industry.
II. The Significance of Pumped Storage Power Stations
(A) Role in the New Power System
Pumped storage power stations are an essential part of the new power system. They possess the unique ability to store large amounts of energy and offer significant environmental advantages. In the context of the “dual-carbon” goal, they act as a cornerstone in the clean energy system, facilitating the transition of the energy structure towards green and low-carbon. This, in turn, lays a solid foundation for China’s energy security and sustainable development path.
(B) Comparison with Other Energy Storage Methods (Table 1)
Energy Storage Method | Advantages | Disadvantages |
---|---|---|
Pumped Storage | High energy storage capacity, long service life, mature technology | Site-dependent, high initial investment |
Battery Storage | Flexible installation, fast response | Limited energy density, short lifespan, environmental concerns |
Flywheel Storage | High power density, short charging time | High self-discharge rate, relatively low energy storage capacity |
III. Shared Steel Casting’s Contribution to Pumped Storage Power Stations
(A) Production of Key Components
- The “Heart” of the Power Station – the Cast Steel Runner
- The cast steel runner, with a diameter of 4 meters, is the core component of a pumped storage power station. Its manufacturing quality directly impacts the operational efficiency and safety of the power station. Shared Steel Casting has emerged as a leader in the casting industry, supplying 25 runner products to various pumped storage power stations across the country. Its market share in this segment has reached an impressive 45% or more.
- Meeting Stringent Requirements
- The runners produced by Shared Steel Casting need to meet extremely high standards. For example, in the case of the Three Gorges Group Changlongshan Pumped Storage Power Station project, which has the highest head in China, the runner must be able to withstand a rated head pressure of 710 meters and a reversible rated speed of 600 revolutions per minute. This requires not only advanced manufacturing techniques but also strict quality control measures.
(B) Quality Assurance Measures
- Rigorous Testing Procedures
- Before a runner is delivered, it undergoes a series of comprehensive tests. These include non-destructive testing methods such as ultrasonic testing and magnetic particle inspection to detect any internal defects. Additionally, dimensional accuracy measurements are carried out to ensure that the runner meets the precise specifications required for seamless integration into the power station.
- Material Selection and Certification
- Shared Steel Casting carefully selects high-quality materials for the production of runners. The materials are sourced from reliable suppliers and undergo strict quality certifications. This ensures that the runners have the necessary strength, durability, and resistance to corrosion, which are vital for their long-term performance in the harsh operating conditions of a pumped storage power station.
IV. Technological Breakthroughs in the Production Process
(A) Tackling the Challenge of Large-Scale Casting
- The Complexity of the Task
- When it came to manufacturing the runners for the Changlongshan Pumped Storage Power Station, Shared Steel Casting faced a formidable challenge. Although the volume of the part was relatively small compared to some other large castings, its functionality and shape were highly complex. The traditional casting methods were insufficient to meet the requirements, especially considering the need to achieve high precision and strength.
- The 3D Printing Solution
- The team at Shared Steel Casting decided to adopt 3D printing technology. However, the available 3D printing equipment could not directly print a complete runner sand mold with a diameter of 4 meters. To overcome this obstacle, they devised a novel segmentation printing strategy. The sand mold was divided into multiple smaller blocks, which were then printed individually.
(B) The Innovation of the Assembly Method
- Inspired by Traditional Woodworking
- After printing the individual sand mold blocks, the next challenge was to assemble them into a perfect whole. The team drew inspiration from the ancient Chinese mortise and tenon joint technique in traditional woodworking. By using an interlocking and overlapping arrangement, they managed to piece together the blocks to form a large circular structure with a diameter of around 4 meters.
- Ensuring Stability during Casting
- To ensure that the assembled sand core could withstand the impact of molten steel during the casting process without collapsing or deforming, the team conducted numerous process adjustments. Through careful calculations and experimental trials, they optimized the assembly structure and the binding methods. As a result, the sand core remained intact and stable during the casting process, and the final runner product achieved excellent dimensional accuracy and structural integrity.
(C) The Significance of the Technological Achievement
- Breaking Foreign Monopoly
- The successful production of the runner for the Changlongshan Pumped Storage Power Station was a milestone. It not only enabled Shared Steel Casting to achieve a significant “from zero to one” breakthrough but also signaled the successful independent research and development of ultra-high head pumped storage runner technology in China. This achievement broke the long-standing monopoly of foreign companies in this critical technology area and placed China at the forefront of the world in pumped storage technology.
- Driving Industry Advancements
- The technological innovation at Shared Steel Casting has had a far-reaching impact on the casting industry as a whole. It has inspired other domestic enterprises to invest in research and development and adopt advanced manufacturing technologies. This has led to an overall improvement in the quality and competitiveness of the domestic casting industry, contributing to the growth and modernization of China’s manufacturing sector.
V. The Transformation from “Manufacturing” to “Intelligent Manufacturing”
(A) The Foundation of Technological Innovation
- Decades of Accumulation in Casting
- Shared Steel Casting’s ability to achieve such remarkable technological breakthroughs is rooted in its decades-long experience and deep expertise in the casting field. Over the years, the company has continuously refined its casting processes, improved its quality control systems, and built a strong technical team. This solid foundation has provided the necessary support for its foray into advanced manufacturing technologies such as 3D printing.
- Leading the Way in 3D Printing Technology
- Since 2013, Shared Steel Casting has been at the forefront of the industrialization research of casting 3D printing technology in China. In 2018, it achieved another significant milestone by successfully building the world’s first 10,000-ton casting 3D printing intelligent factory. This factory is equipped with state-of-the-art 3D printing equipment and automated production lines, enabling the company to produce high-quality castings with greater precision and efficiency.
(B) The Application and Impact of “Intelligent Manufacturing”
- Enhanced Product Quality and Performance
- The adoption of 3D printing technology in the production of castings has revolutionized the manufacturing process. It allows for more complex geometries and finer details to be achieved, resulting in products with improved performance characteristics. For example, the runners produced using 3D printing have better flow characteristics, which enhance the overall efficiency of the pumped storage power stations.
- Increased Production Efficiency and Cost Savings
- The intelligent manufacturing system at Shared Steel Casting has significantly increased production efficiency. The automated production lines reduce human errors and production cycle times. Additionally, the ability to optimize the design and manufacturing process through digital simulations and 3D printing has led to cost savings in material consumption and post-processing operations.
(C) The Future Prospects of “Intelligent Manufacturing” in the Industry
- Expanding Applications
- The success of Shared Steel Casting in applying 3D printing technology to the production of key components for pumped storage power stations paves the way for its wider application in other industries. In the future, we can expect to see 3D printing being used in the manufacturing of more complex and high-value-added products in sectors such as aerospace, automotive, and energy.
- Technological Advancements and Integration
- As technology continues to evolve, we can anticipate further advancements in 3D printing materials, equipment, and software. This will enable even more precise and efficient manufacturing processes. Moreover, the integration of 3D printing with other emerging technologies such as artificial intelligence, the Internet of Things, and big data analytics will create new opportunities for intelligent manufacturing. For example, real-time monitoring and optimization of the 3D printing process through the Internet of Things can enhance product quality and production efficiency.
VI. Shared Steel Casting’s Role in Regional and National Development
(A) Contribution to the Local Economy
- Job Creation and Skill Development
- Shared Steel Casting is a major employer in the region, providing a significant number of jobs. The company offers a wide range of employment opportunities, from skilled technicians and engineers to administrative and support staff. In addition to creating jobs, it also focuses on employee training and skill development. Through in-house training programs and collaboration with educational institutions, the company equips its employees with the latest technical knowledge and skills, enhancing their employability and career prospects.
- Driving the Growth of the Industrial Chain
- The success of Shared Steel Casting has a positive spillover effect on the local industrial chain. It stimulates the growth of upstream and downstream industries, such as raw material suppliers, equipment manufacturers, and logistics providers. This creates a vibrant industrial ecosystem that promotes economic growth and diversification in the region.
(B) National Significance in Energy and Manufacturing Sectors
- Ensuring Energy Security
- By manufacturing high-quality components for pumped storage power stations, Shared Steel Casting plays a crucial role in ensuring the stable operation of these power stations. This, in turn, contributes to the reliability and security of the national energy grid. Pumped storage power stations are essential for balancing the electricity supply and demand, especially in the context of the increasing penetration of renewable energy sources.
- Enhancing National Manufacturing Competitiveness
- Shared Steel Casting’s achievements in technological innovation and high-quality manufacturing represent a significant contribution to enhancing China’s manufacturing competitiveness on the global stage. Its success in breaking foreign monopolies and achieving world-class manufacturing standards serves as an inspiration and model for other domestic enterprises. This helps to promote the development of high-end manufacturing in China and upgrade the overall industrial structure.
VII. Conclusion
Shared Steel Casting has emerged as a leading force in the manufacturing of key components for pumped storage power stations. Through its continuous technological innovation, from the development of 3D printing strategies for large-scale casting to the transformation towards intelligent manufacturing, it has achieved remarkable results. Its contributions not only ensure the efficient and reliable operation of pumped storage power stations, which are vital for the energy sector, but also drive the growth and modernization of the manufacturing industry. As Shared Steel Casting continues to pursue excellence and innovation, it will undoubtedly play an even more significant role in the future development of China’s energy and manufacturing landscapes, contributing to the realization of the “tech-powerful country” and national rejuvenation dreams.
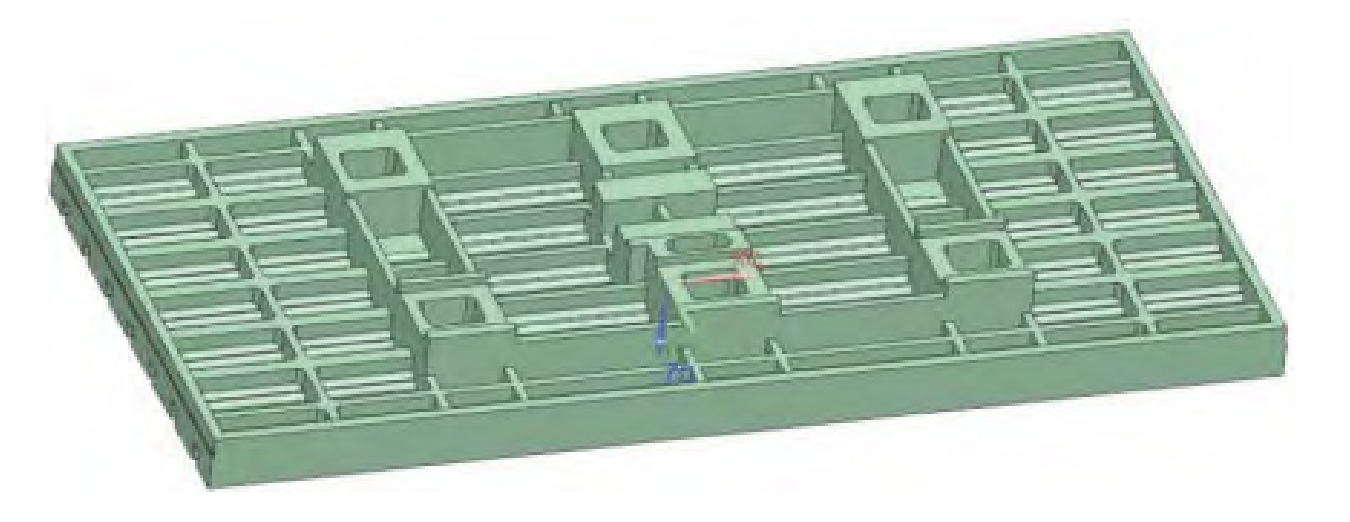