Blow hole defects represent a persistent challenge in resin coated sand castings, particularly for valve components produced via automated lines. These defects primarily manifest as intrusive or reactive blow holes, governed by distinct formation mechanisms:
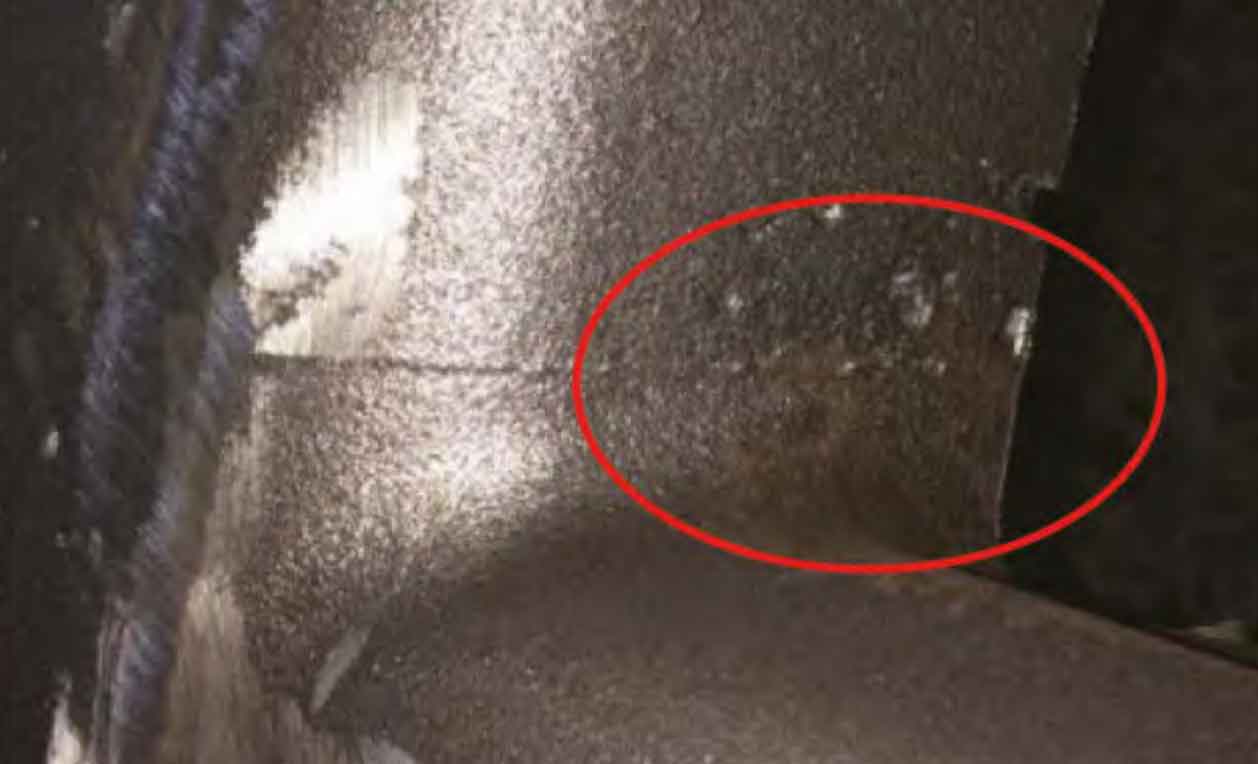
1. Formation Mechanisms of Blow Hole Defects
Intrusive blow hole defects occur when gas pressure at the mold-metal interface exceeds the metal’s surface tension before solidification initiates. The gas penetration follows:
$$ P_{\text{gas}} > \frac{2\sigma}{r} + \rho g h $$
where \( \sigma \) = surface tension, \( r \) = pore radius, \( \rho \) = density, \( g \) = gravity, \( h \) = metal head pressure. Characterized by spherical/pear-shaped cavities with smooth walls, these blow hole defects typically cluster in upper sections or near surfaces.
Reactive blow hole defects stem from nitrogen liberation during hexamine (C6H12N4) decomposition:
$$ \ce{C6H12N4 -> 4NH3 + 6CH2} $$
$$ \ce{NH3 <=> [N] + 3[H]} $$
Nitrogen solubility decreases during cooling (\( S_{\text{N}} \propto e^{-\Delta H/RT} \)), causing supersaturation and subcutaneous blow hole defects formation.
2. Material-Related Causes and Countermeasures
Resin coated sand properties critically influence blow hole defect incidence. Key parameters and standards:
Parameter | Target Value | Standard |
---|---|---|
Hot Flexural Strength | 2.6–3.6 MPa | JB/T 8583–2008 |
Room Temp. Strength | 4.0–5.0 MPa | |
Ignition Loss | <4.0% | |
Melting Point | 97–107°C | |
SiO2 Content | >94% | |
Gas Evolution | <25 mL/g |
Prevention strategies include:
- High-strength formulations reducing resin content
- Low-gas evolution sands with delayed gas release kinetics
- Hexamine minimization in reactive blow hole defect scenarios
3. Design-Induced Blow Hole Defects and Solutions
Process Design: Inadequate venting causes gas entrapment. Essential features:
- Minimum one open riser per system
- Conical vents (2–2.5 mm tip thickness) at flow termini
The gas escape efficiency \( \eta \) through vents follows:
$$ \eta = 1 – e^{-\frac{k A \Delta P t}{\mu V}} $$
where \( k \) = permeability, \( A \) = vent area, \( \Delta P \) = pressure differential, \( \mu \) = gas viscosity, \( V \) = cavity volume.
Tooling Design:
- Uniform shell thickness (3–8 mm) ensuring complete cure
- Hollow cores with V-section vents
- Interlocking mold geometry preventing sealant ingress
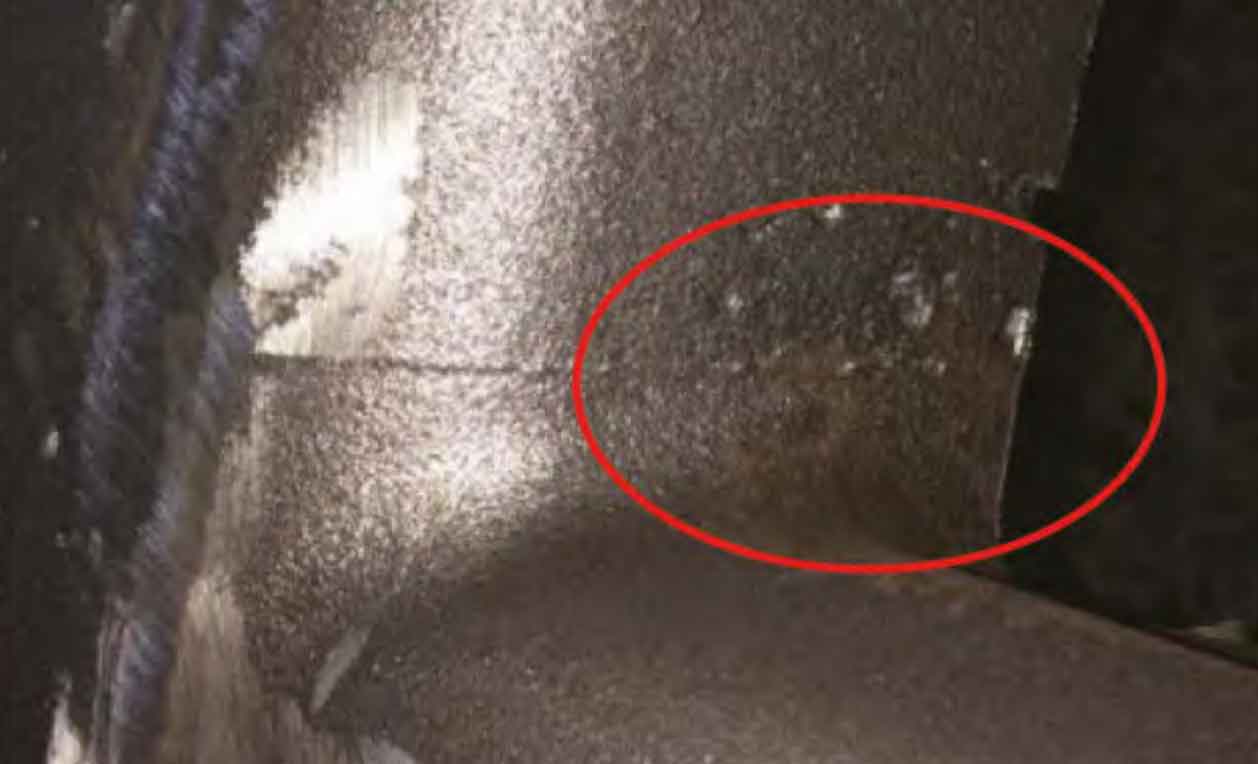
4. Process Control Mitigation Strategies
Mold Production: Parameter optimization prevents “green sand” inclusion. Critical controls:
Parameter | Effect |
---|---|
Curing Temperature | 240–280°C |
Curing Time | 30–60 s |
Sand Density | 1.5–1.7 g/cm³ |
Coating and Baking: Water-based coatings require sequential drying:
- Immediate torch drying after application
- Final baking at 160°C for 60 minutes
The moisture removal rate \( \dot{m} \) during baking:
$$ \dot{m} = h_m A (c_{\text{surf}} – c_{\infty}) $$
where \( h_m \) = mass transfer coefficient, \( A \) = surface area, \( c \) = vapor concentration.
Melting and Pouring: Critical parameters for blow hole defect prevention:
Parameter | Target |
---|---|
Deoxidation | 0.08% Al + 0.08% Si-Ca |
Ladle Temperature | >800°C |
Pouring Temperature | 1,550–1,580°C |
Pouring Rate | 1.5–2.5 kg/s |
Temperature stratification management is vital – lower-temperature metal from ladle ends is diverted to non-critical castings.
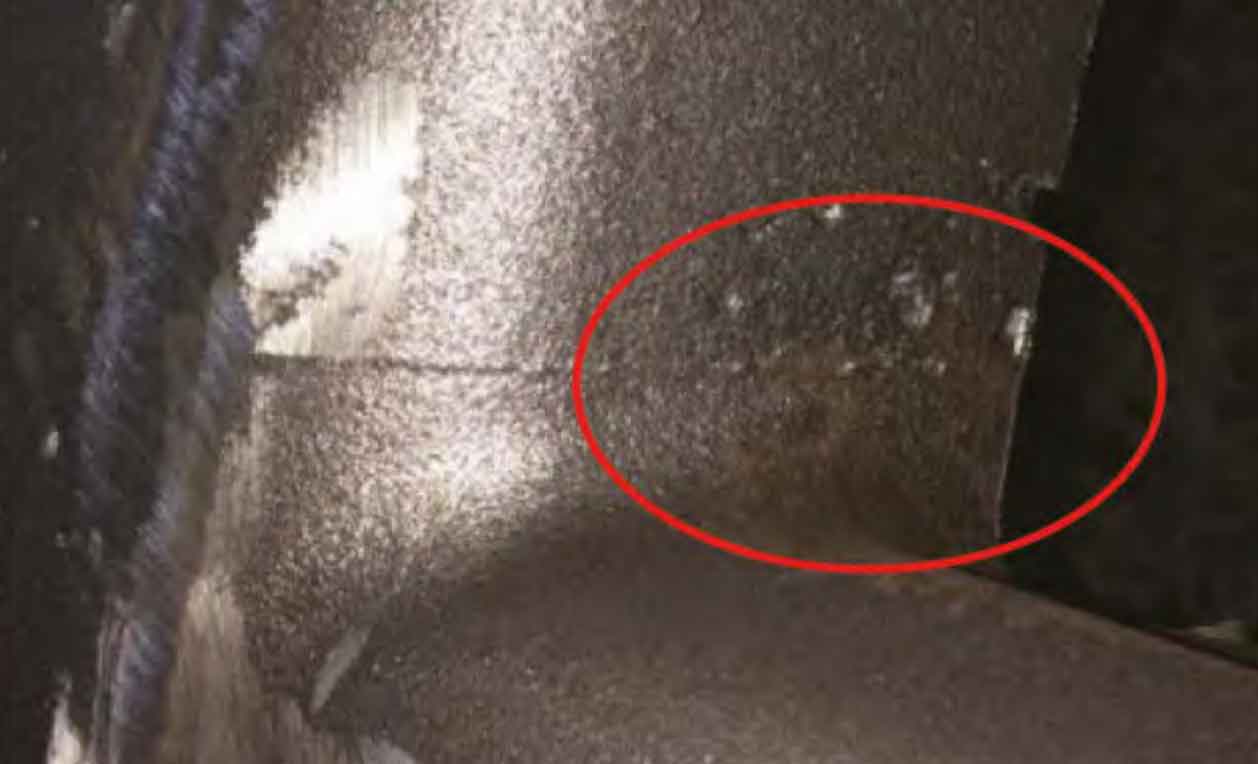
5. Integrated Prevention Framework
A comprehensive approach minimizes blow hole defects through:
- Material Selection: Low-gas evolution resin coated sand with <25 mL/g gas evolution
- Design Principles: Mandatory venting systems + thermal modulus analysis
- Process Controls: Real-time monitoring of curing kinetics and pouring parameters
The blow hole defect occurrence probability \( P_d \) integrates these factors:
$$ P_d = k \cdot G_v^{a} \cdot t_c^{b} \cdot \Delta T^{-c} $$
where \( G_v \) = gas volume, \( t_c \) = core curing time, \( \Delta T \) = superheat, \( k \), \( a \), \( b \), \( c \) = process constants.
Implementation reduces blow hole defect rates by 60–80%, decreasing scrap costs by 25% while improving pressure integrity in valve castings. Continuous monitoring of these parameters remains essential for sustainable blow hole defect prevention.