1. Introduction to Low Pressure Casting
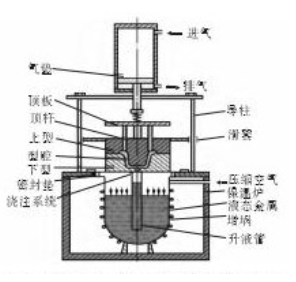
Low pressure casting is a casting process where molten metal is forced into a mold cavity under a relatively low pressure (0.02 MPa – 0.06 MPa). It was first proposed by British scientist E.F. LAKE over 100 years ago but only gained large-scale industrial application in 1945. The process involves using compressed air or inert gas to push the metal liquid up the riser tube and into the mold cavity. The basic steps are as follows:
- Gas Introduction: Dry compressed air or inert gas is introduced into a sealed crucible or tank.
- Metal Liquid Ascent: The metal liquid rises steadily along the riser tube due to gas pressure and enters the mold cavity through the ingate.
- Solidification under Pressure: The gas pressure is maintained until the casting solidifies completely.
- Pressure Release and Ejection: The gas pressure is released, and the unfrozen metal in the riser tube returns to the crucible. The casting is then ejected.
The following is a schematic diagram of the low pressure casting process:
2. Process Parameters in Low Pressure Casting
The quality of castings in low pressure casting is significantly influenced by various process parameters. The key parameters and their effects are as follows:
Parameter | Definition | Effect on Casting Quality | Optimal Range |
---|---|---|---|
Lifting Pressure (Pl) | Pressure required to raise the metal level to the gate. | Affects the rising speed of the metal liquid. A slow speed helps gas escape and prevents splashing. | N/A (Depends on specific casting requirements) |
Filling Pressure (Pf) | Pressure needed for the metal liquid to reach the top of the mold during filling. | Influences the filling process and the final quality of the casting. | N/A (Depends on the casting geometry and metal properties) |
Filling Speed (vf) | The rate at which the metal level rises during filling. | A proper filling speed is crucial to avoid defects like cold shuts and misruns. Too fast a speed can cause turbulence and oxide inclusions. | Depends on the casting design and metal characteristics |
Crystallization Pressure (Pc) | Pressure applied after the mold is filled to aid solidification. | Higher pressure leads to better feeding, denser microstructure, and improved mechanical properties. | 0.1 MPa – 0.25 MPa |
Holding Pressure Time (th) | The duration for which the pressure is maintained during solidification. | Insufficient time can cause casting “emptying,” while excessive time can lead to difficulties in ejecting the casting and reduce the process yield. | Depends on the casting size and metal type |
Mold Temperature (Tm) | Temperature of the mold. For non-metallic molds, it is usually room temperature. For metallic molds, it varies depending on the casting material. | Affects the solidification rate and the quality of the casting surface. | For aluminum alloy casting in metal molds: 200°C – 250°C (up to 300°C – 350°C for thin-walled complex parts) |
Pouring Temperature (Tp) | Temperature of the molten metal at pouring. | Lower pouring temperatures are preferred to reduce defects. | Generally 10°C – 20°C lower than gravity casting for aluminum alloys |
3. Technical Characteristics of Low Pressure Casting
3.1 Advantages
- High Metal Purity: The bottom-feeding process reduces the chance of slag entering the mold cavity, resulting in fewer inclusions in the casting.
- Smooth Filling: The balanced pressure and bottom-feeding technique ensure a stable filling process, minimizing turbulence and splash, and reducing defects like double oxide films and oxide inclusions.
- Enhanced Fluidity: The application of pressure improves metal fluidity, facilitating the formation of castings with good surface finish and clear contours, especially beneficial for complex thin-walled castings.
- Improved Solidification: Castings solidify under pressure with a top-down sequential solidification pattern, leading to better feeding, denser microstructure, and fewer shrinkage defects.
- High Metal Yield: Low pressure casting typically does not require risers, and the unfrozen metal in the riser tube can be recycled, resulting in a high metal yield, often above 90%.
3.2 Disadvantages
- High Equipment Cost: The equipment for low pressure casting is expensive, requiring a large initial investment.
- Low Production Efficiency: The process is relatively slow compared to some other casting methods.
- Material Compatibility Issues: When casting aluminum alloys, the crucible and riser tube can be eroded by the molten metal, leading to increased iron content in the metal and degraded casting properties.
4. Common Casting Defects and Solutions in Low Pressure Casting
Low pressure casting can encounter several common defects, and understanding their causes and implementing appropriate solutions is crucial for producing high-quality castings.
Defect Type | Appearance | Causes | Prevention and Solution Measures |
---|---|---|---|
Porosity | Circular or elliptical holes with smooth inner walls and a slight oxide color. | 1. High filling speed causing turbulence and gas entrapment. 2. Gas evolution from sand molds and cores during solidification. 3. Poor ventilation in the mold cavity. | 1. Optimize filling speed to ensure smooth filling. 2. Improve the venting conditions of sand molds and cores. Reduce resin content in molds to decrease gas generation. 3. Ensure proper functioning of vent holes and plugs. |
Shrinkage Cavity and Porosity | Irregular holes with rough inner walls and dendritic protrusions, usually at hot spots or the last solidifying areas. | Inadequate temperature gradient during solidification, preventing sequential solidification and proper feeding at hot spots. | 1. Enhance heat dissipation at hot spots (e.g., using chills). 2. Lower pouring temperature without causing cold shuts. 3. Increase the holding pressure during solidification to improve metal fluidity and feeding ability. |
Cold Shut | Cold shut lines where two metal fronts do not fuse properly. | 1. Low pouring temperature or high mold cooling rate. 2. Insufficient filling pressure leading to poor metal fluidity. | 1. Increase the pouring temperature appropriately. 2. Heat the chills if cold shut lines are caused by rapid cooling. 3. Raise the filling pressure to improve metal fluidity. |
Inclusion | Irregularly shaped defects with a color different from the casting body. | 1. Foreign materials in the mold cavity from the cleaning process. 2. Turbulent filling causing double oxide films. | 1. Ensure thorough cleaning of the mold cavity during the cleaning process. 2. Adjust the filling pressure to avoid turbulence. Install a filter at the riser tube to filter and stabilize the metal flow. |
5. Conclusion and Outlook
Low pressure casting offers several advantages in terms of casting quality and process yield, especially for large and complex thin-walled castings. However, it also has some limitations, such as high equipment costs and potential material compatibility issues.
To further improve the low pressure casting process, future research and development could focus on the following areas:
- Advanced Numerical Simulation: Develop more accurate models to simulate the metal filling, solidification, and crystallization processes, enabling better prediction and control of casting defects.
- In-situ Detection and Monitoring: Improve the in-situ detection capabilities of casting properties, such as using ultrasonic technology to detect residual stress and thermal analysis to predict mechanical properties. This would allow for real-time process control and reduce the need for destructive testing.
- Process Optimization and Innovation: Continuously optimize the process parameters and explore new techniques to enhance the efficiency and quality of low pressure casting, expanding its application range in various industries.
In summary, low pressure casting has significant potential for further development and improvement, and continued research and innovation will contribute to its wider application and better performance in the manufacturing of high-quality castings.