The material grade of the used steering knuckle is QT450-10, and its chemical composition mainly includes C, Si, Mn, S, P, residual magnesium and rare earth, which can be expressed by eutectic Sc, as shown in the formula:

Figure 1 shows the metallographic structure of ductile iron castings with different eutectic degrees under the same spheroidizing inoculation treatment conditions. It can be seen from the figure that the spheroidization grade of the metallographic structure is 1~2, and the size of the graphite ball is 7~8. Figure 1 (a) shows the lowest eutectic degree, with a small number of relatively large graphite spheres. This is because the hypoeutectic state first precipitates austenite, and the morphology of austenite phase is the driving force for the formation of other structures. The bifurcation and growth of austenite affect the final shape, size and distribution of graphite spheres. Large dendrite spacing will lead to the formation of large graphite balls, while small dendrite spacing will lead to small graphite balls, which is because some graphite is precipitated in the interdendritic liquid. The size of graphite sphere in Fig. 1 (b~c) tends to be consistent, and with the increase of carbon equivalent and the eutectic degree around 1, the number of graphite size is also the largest (Fig. 1 (d)).
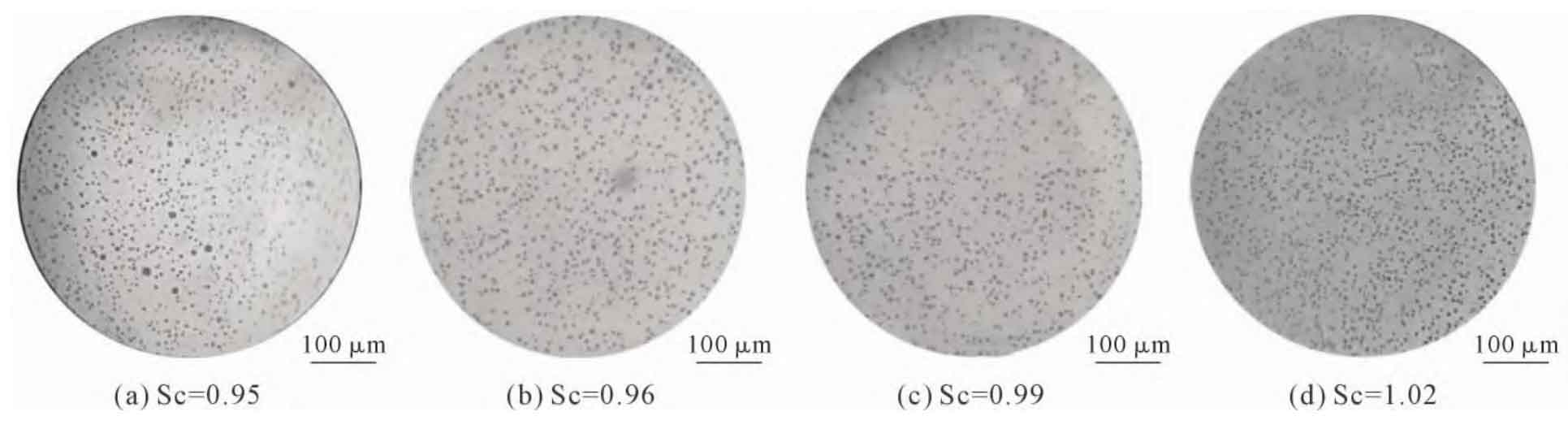
Figure 2 shows the shrinkage defects of the nodular cast iron of the steering knuckle corresponding to different eutectic degrees. Figure 2 (a) shows the smallest eutectic degree. It can be seen that a large area of shrinkage porosity appears at the hot spot. As the eutectic degree approaches 1, the shrinkage porosity becomes smaller and smaller, as shown in Figure 2 (b~c). It is well known that when the molding material is fixed, the cooling rate of a certain component of ductile iron castings in the mold is basically similar after pouring. Therefore, it can be considered that the chemical composition of ductile iron castings determines its solidification behavior, microstructure and mechanical properties. For spheroidal graphite cast iron, after spheroidization and inoculation, it is the best condition to obtain high spheroidization rate, high quantity of spheroidal graphite, low shrinkage cavity and shrinkage porosity risk when solidification happens in eutectic state, that is, eutectic degree Sc=1. Therefore, by controlling the eutectic degree, a large number of graphite spheres formed in the solidification process of molten iron with eutectic composition have strong self-expansion ability, which can play a certain role in feeding the ductile iron castings. On the contrary, the farther away the spheroidal graphite cast iron is from the separation eutectic point, the greater the solidification shrinkage, and the easier to produce shrinkage defects. The reason is that the large liquid-solid line distance leads to the difficulty of feeding, while the small amount of graphite, the small graphitization expansion, and the small effect of counteracting the solidification shrinkage.
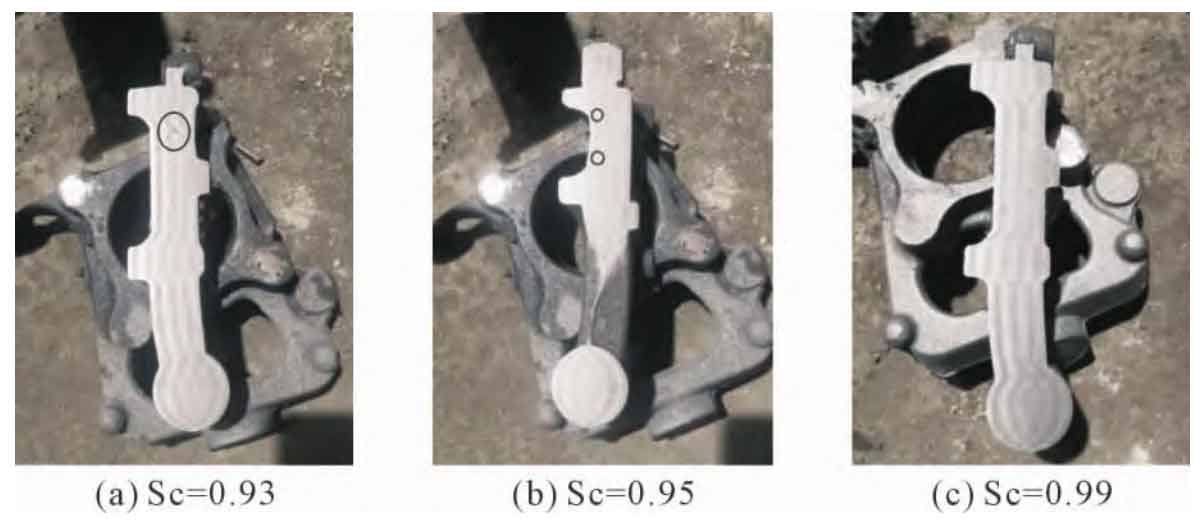
At the same time, the amount of w (Mg residue) should be strictly controlled for ductile iron castings. In order to obtain better spheroidization rate, the amount of w (Mg residue) is generally higher than 0.03%. Since Mg increases the shrinkage tendency of molten iron, the lower the amount of w (Mg residue) should be, the better for preventing shrinkage porosity; Considering the difficulty of process control, it is generally controlled at 0.035%~0.045% in actual production.