Choosing the right excavator bucket teeth for a specific job is crucial for maximizing efficiency and productivity. The type of teeth you select depends on the material you’ll be excavating, the ground conditions, and the specific requirements of the project. Here are some key factors to consider when choosing excavator bucket teeth:
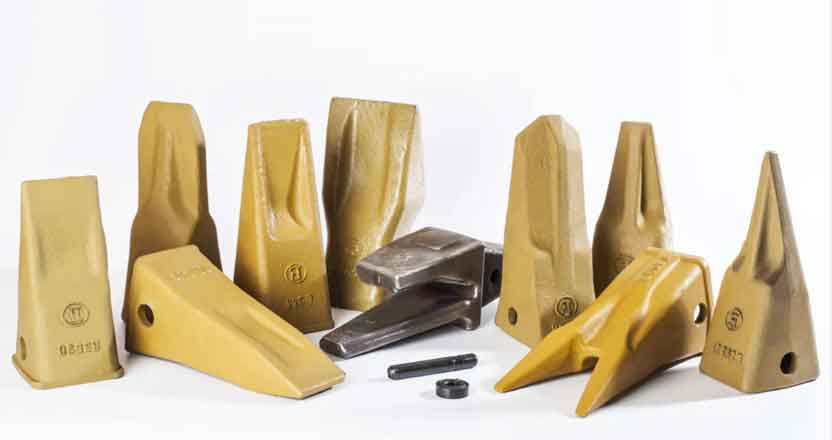
- Tooth Type: There are various types of excavator bucket teeth available, each designed for specific applications. Common types include standard teeth, rock teeth, heavy-duty teeth, tiger teeth, and more. Standard teeth are suitable for general digging in normal soil conditions, while rock teeth are designed for excavating in rocky terrain. Heavy-duty teeth offer increased durability for demanding applications, and tiger teeth provide extra penetration power. Assess the material you’ll be excavating and choose the tooth type that best suits your needs.
- Tooth Configuration: Excavator bucket teeth come in different configurations, such as single-point, twin tiger, or wide-tip. Single-point teeth offer a narrow point for precise digging, while twin tiger teeth provide enhanced cutting and penetration abilities. Wide-tip teeth are suitable for handling loose materials and increasing bucket capacity. Consider the nature of the material and the desired digging performance to determine the appropriate tooth configuration.
- Tooth Size: The size of the excavator bucket teeth should match the size of the bucket and the excavator itself. Choosing the right tooth size ensures proper fitment, optimal performance, and efficient digging. Oversized or undersized teeth can lead to reduced productivity, increased wear, and potential damage to the bucket or excavator. Refer to the manufacturer’s guidelines or consult with industry experts to select the correct tooth size for your equipment.
- Tooth Material: Excavator bucket teeth are typically made of durable materials like alloy steel or cast manganese steel. The material’s hardness, toughness, and wear resistance are important considerations. Harder materials offer better resistance against abrasion, while tougher materials can handle impact and shock loads effectively. Evaluate the anticipated ground conditions and the abrasive nature of the material you’ll be excavating to choose the appropriate tooth material that balances durability and performance.
- Tooth Adapter System: The tooth adapter system connects the teeth to the excavator bucket. It should be sturdy, reliable, and easy to use for efficient tooth replacement. Quick coupler systems or hammerless locking systems allow for rapid tooth changes, reducing downtime and improving productivity. Consider the ease of tooth replacement and the availability of compatible adapters when selecting the tooth and adapter system.
- Manufacturer’s Reputation and Support: Choose excavator bucket teeth from reputable manufacturers known for producing high-quality products. Reliable manufacturers provide warranties, technical support, and assistance in selecting the right teeth for specific applications. Research customer reviews, seek recommendations from industry professionals, and consult with authorized dealers to ensure you’re investing in reliable and durable bucket teeth.
Remember that selecting the right excavator bucket teeth is a balance between the requirements of the job, the equipment you’re using, and the ground conditions. Assessing these factors and consulting with experts can help you make an informed decision, leading to improved efficiency, increased productivity, and reduced maintenance costs.